Plasma arc melting (PAM) is a specialized metallurgical process used to melt and refine metals, particularly those with high melting points or those that are highly reactive or volatile. The process involves the use of a plasma arc torch, which generates an extremely high-temperature plasma arc (exceeding 15,000 K) to melt the metal under an inert gas atmosphere, typically helium or argon. This controlled environment prevents oxidation and contamination, making it ideal for producing high-purity metals and complex alloys, such as titanium alloys and titanium aluminides. The process also minimizes the evaporation of volatile alloying elements, ensuring precise control over the final alloy composition.
Key Points Explained:
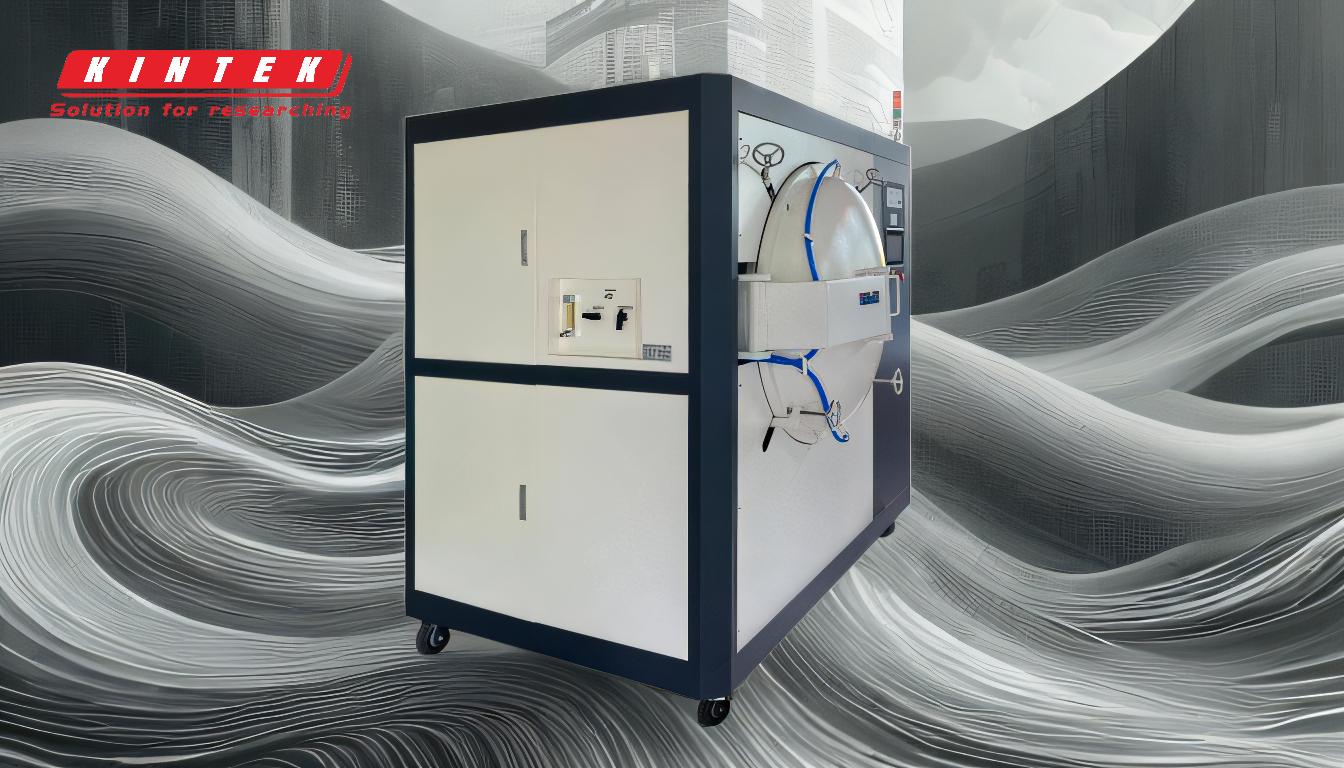
-
What is Plasma Arc Melting?
- Plasma arc melting is a high-temperature melting process that uses a plasma arc torch to generate heat. The torch produces a plasma arc with temperatures exceeding 15,000 K, which is capable of melting even the most refractory metals.
- The process is conducted under an inert gas atmosphere, such as helium or argon, to prevent oxidation and contamination of the metal.
-
Inert Gas Atmosphere
- The use of inert gases like helium or argon ensures that the metal does not react with oxygen or other atmospheric gases during the melting process.
- This is particularly important for reactive metals like titanium, which can easily form oxides or nitrides if exposed to air.
-
Pressure Range
- The process operates within a pressure range of 400 to 1,200 mbar absolute. This controlled pressure environment helps in maintaining the stability of the plasma arc and the quality of the melted metal.
-
Suppression of Evaporation
- One of the key advantages of plasma arc melting is its ability to suppress the evaporation of volatile alloying elements. This is crucial for producing complex alloys with precise compositions, such as titanium alloys and titanium aluminides.
- Traditional melting processes often lead to the loss of volatile elements, which can alter the desired properties of the alloy.
-
Applications in Complex Alloys
- Plasma arc melting is particularly useful for producing high-performance alloys that require precise control over their composition. For example, titanium alloys and titanium aluminides are widely used in aerospace and automotive industries due to their high strength-to-weight ratio and excellent corrosion resistance.
- The ability to maintain the integrity of volatile elements during the melting process makes PAM an ideal choice for these applications.
-
Advantages of Plasma Arc Melting
- High Purity: The inert gas atmosphere and controlled environment result in high-purity metals with minimal contamination.
- Precision: The process allows for precise control over the alloy composition, ensuring that the final product meets stringent specifications.
- Versatility: Plasma arc melting can be used for a wide range of metals, including those with high melting points and those that are highly reactive or volatile.
-
Plasma Arc Furnace
- The plasma arc furnace is the key equipment used in this process. It consists of a plasma torch, a crucible to hold the metal, and a system to maintain the inert gas atmosphere and pressure.
- The furnace is designed to handle the extreme temperatures and provide a stable environment for the melting process.
In summary, plasma arc melting is a highly advanced and precise method for melting and refining metals, particularly those that are difficult to process using conventional methods. Its ability to operate under controlled conditions and suppress the evaporation of volatile elements makes it indispensable for producing high-performance alloys in industries where material purity and composition are critical.
Summary Table:
Aspect | Details |
---|---|
Temperature | Exceeds 15,000 K |
Atmosphere | Inert gases (helium or argon) |
Pressure Range | 400 to 1,200 mbar absolute |
Key Benefit | Suppresses evaporation of volatile elements, ensuring precise alloy composition |
Applications | Titanium alloys, titanium aluminides, aerospace, and automotive industries |
Advantages | High purity, precision, and versatility |
Discover how plasma arc melting can revolutionize your metal refining process—contact our experts today!