SPS, or Spark Plasma Sintering, is a field-assisted sintering technique that enables the production of fully dense materials at lower temperatures and shorter processing times compared to traditional methods like hot pressing or pressureless sintering. Its key advantages include high heating and cooling rates, enhanced densification through pulsed current, and precise control over sintering parameters. This makes SPS highly versatile, capable of processing a wide range of materials, from low melting point metals to ultra-high temperature ceramics, while significantly reducing cycle times and energy consumption.
Key Points Explained:
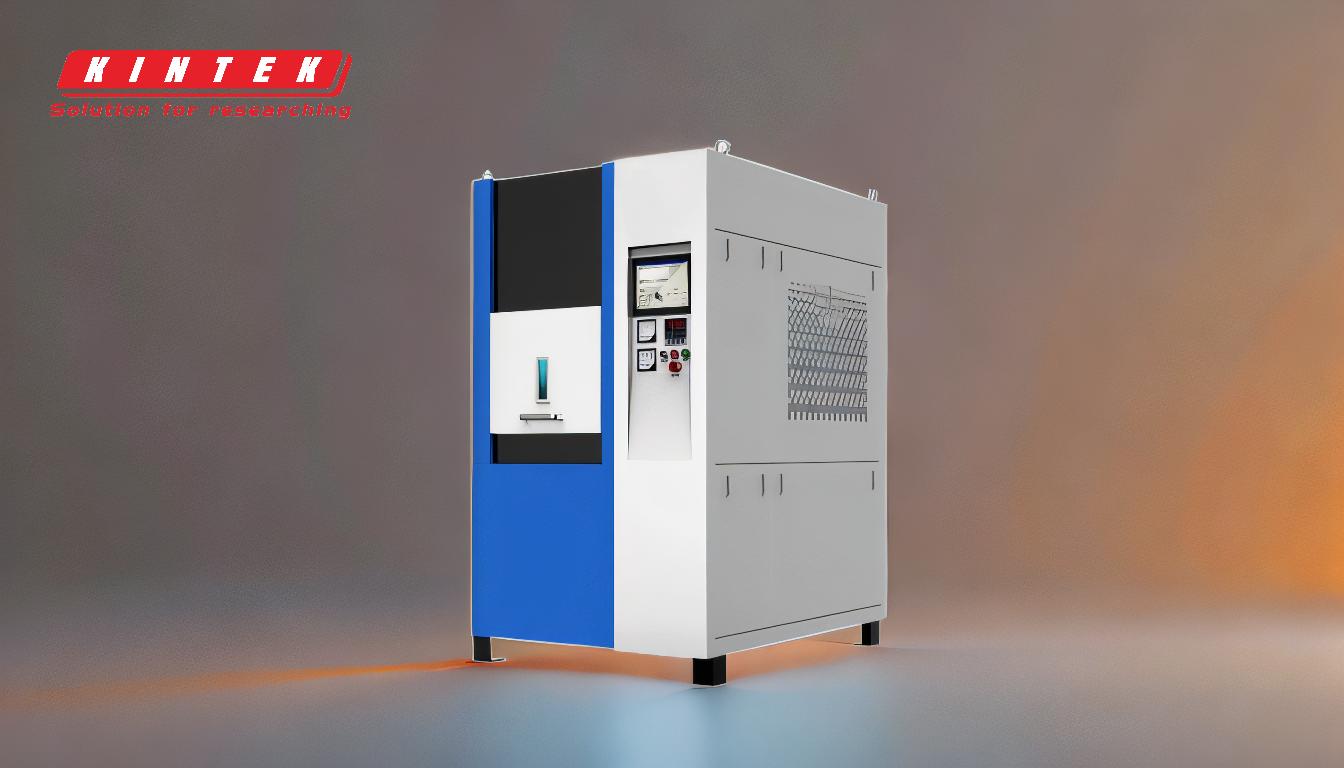
-
Definition of SPS:
- SPS (Spark Plasma Sintering) is a field-assisted sintering technique that uses pulsed electric current and mechanical pressure to densify materials.
- It is known for achieving fully dense billets at lower temperatures and in shorter times compared to conventional methods.
-
Advantages of SPS:
-
High Heating and Cooling Rates:
- SPS systems can heat and cool materials rapidly, reducing overall processing times from hours or days to just minutes.
- This is particularly beneficial for industrial applications where time efficiency is critical.
-
Enhanced Densification:
- The pulsed current used in SPS improves densification, especially in electrically conductive materials.
- This results in materials with higher density and improved mechanical properties.
-
Lower Sintering Temperatures:
- SPS operates at lower temperatures compared to traditional sintering methods, which reduces energy consumption and minimizes thermal degradation of materials.
-
Versatility:
- SPS can process a wide range of materials, including low melting point metals and ultra-high temperature ceramics, making it suitable for diverse applications.
-
Precision Control:
- The process allows for fine-tuning of sintering parameters (temperature, pressure, and time), enabling optimal material properties and consistency.
-
Multi-Field Coupling:
- SPS combines electrical, mechanical, and thermal fields, which enhances the sintering process and allows for adjustable sintering pressure and tailored material outcomes.
-
High Heating and Cooling Rates:
-
Applications and Benefits:
-
Short Cycle Times:
- SPS significantly reduces processing times, making it ideal for high-throughput manufacturing environments.
-
Energy Efficiency:
- Lower sintering temperatures and shorter processing times contribute to reduced energy consumption.
-
Material Diversity:
- SPS can densify materials that are challenging to process using conventional methods, expanding the range of possible applications.
-
High-Quality Output:
- The precise control over sintering parameters ensures consistent and high-quality material properties, which is critical for advanced engineering applications.
-
Short Cycle Times:
-
Comparison to Conventional Methods:
-
Hot Pressing and Pressureless Sintering:
- Traditional methods require longer sintering times (hours to days) and higher temperatures to achieve similar densities.
- These methods are less efficient and may result in material degradation due to prolonged exposure to high temperatures.
-
SPS Efficiency:
- SPS achieves comparable or superior results in a fraction of the time, with better control over material properties.
-
Hot Pressing and Pressureless Sintering:
In summary, SPS is a highly efficient and versatile sintering technique that offers significant advantages over traditional methods, including faster processing times, lower energy consumption, and the ability to produce high-quality, fully dense materials across a wide range of applications. Its precision and adaptability make it a valuable tool in advanced material manufacturing.
Summary Table:
Aspect | Details |
---|---|
Definition | Field-assisted sintering using pulsed electric current and mechanical pressure. |
Key Advantages | - High heating/cooling rates - Enhanced densification - Lower sintering temperatures - Versatility - Precision control |
Applications | - Short cycle times - Energy efficiency - Material diversity - High-quality output |
Comparison to Traditional Methods | - Faster processing - Lower energy use - Better material properties |
Ready to transform your material manufacturing process? Contact us today to learn more about SPS!