An induction furnace is a highly efficient and precise melting system used primarily in metallurgical processes. Its construction is centered around three main components: a power supply, an induction coil, and a crucible made of refractory materials. The power supply generates a high-frequency alternating current, which flows through the induction coil, creating a rapidly reversing magnetic field. This magnetic field induces eddy currents in the metal charge placed inside the crucible, generating heat through resistance and melting the metal. The crucible, made of non-conductive and heat-resistant materials, holds the metal charge, which effectively acts as the secondary winding of a transformer. The entire system is designed to ensure that heat is generated directly within the metal, minimizing energy loss and providing precise control over the melting process.
Key Points Explained:
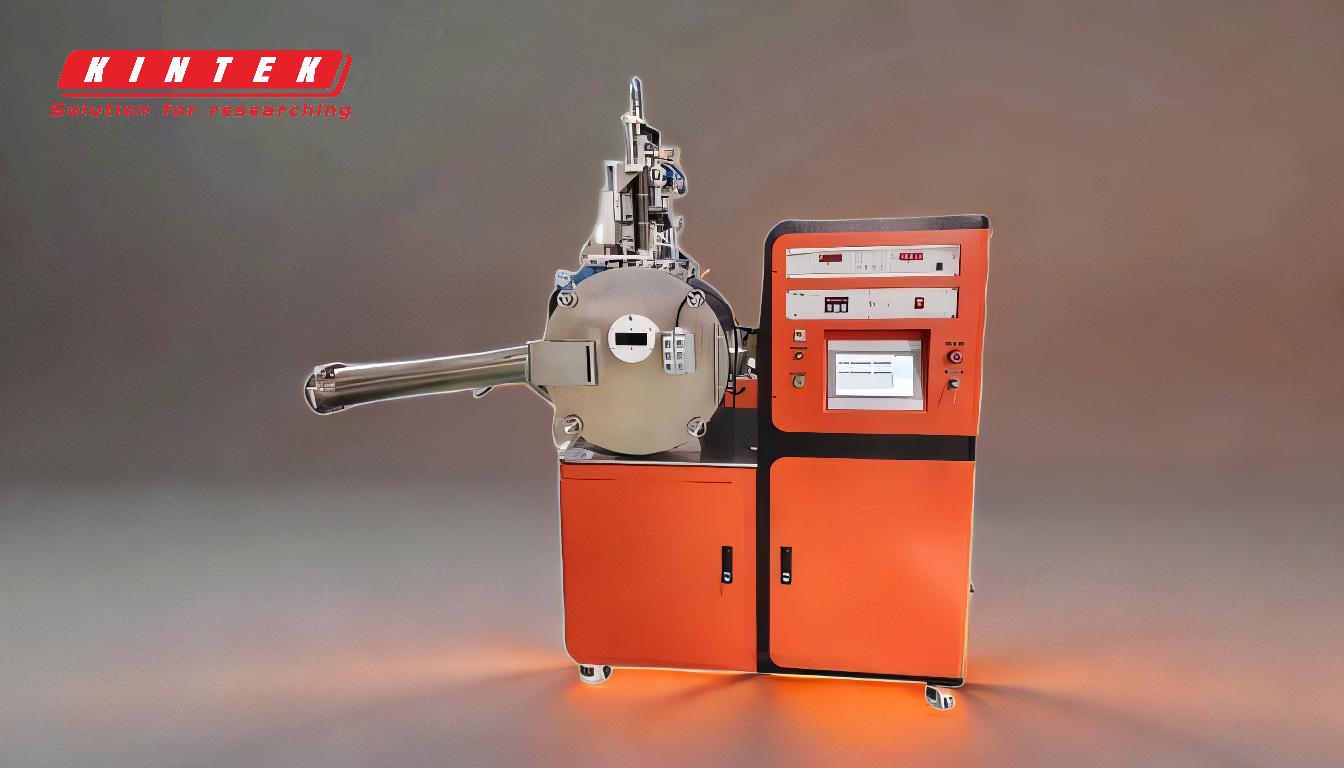
-
Power Supply:
- The power supply is the heart of the induction furnace, providing the alternating current (AC) required for the induction process.
- It generates high-frequency AC, which is essential for creating the rapidly reversing magnetic field.
- The frequency of the AC can vary depending on the application, with higher frequencies typically used for smaller furnaces and lower frequencies for larger ones.
- The power supply must be robust and reliable to ensure consistent performance and to handle the high energy demands of the melting process.
-
Induction Coil:
- The induction coil, usually made of hollow copper tubing, surrounds the crucible and carries the alternating current from the power supply.
- The coil is designed to create a strong and uniform magnetic field that penetrates the metal charge within the crucible.
- The hollow design of the copper tubing allows for water cooling, which is necessary to prevent the coil from overheating due to the high currents passing through it.
- The number of turns and the geometry of the coil are carefully calculated to optimize the magnetic field and ensure efficient heating of the metal charge.
-
Crucible:
- The crucible is a container made of refractory materials, such as ceramic or graphite, that can withstand extremely high temperatures and are non-conductive.
- It holds the metal charge, which is the material to be melted, such as steel, iron, aluminum, or other metals.
- The crucible is placed inside the induction coil, and the metal charge acts as the secondary winding of a transformer, where eddy currents are induced.
- The design of the crucible must ensure that it can contain the molten metal without degrading or reacting with the metal, maintaining the purity of the melt.
-
Metal Charge:
- The metal charge is the material that is to be melted within the crucible.
- When the alternating magnetic field from the induction coil penetrates the metal charge, it induces eddy currents within the metal.
- These eddy currents generate heat through the resistance of the metal, causing it to melt.
- The metal charge effectively acts as the secondary winding of a transformer, with the induction coil being the primary winding.
-
Cooling System:
- The induction coil, due to the high currents passing through it, generates significant heat and requires cooling to prevent damage.
- A cooling system, typically using water, circulates through the hollow copper tubing of the induction coil to dissipate the heat.
- Proper cooling is essential to maintain the efficiency and longevity of the induction furnace.
-
Control System:
- Modern induction furnaces are equipped with sophisticated control systems that allow for precise regulation of the melting process.
- These systems monitor and control parameters such as temperature, power input, and cooling rates, ensuring consistent and high-quality results.
- The control system also provides safety features, such as over-temperature protection and fault detection, to prevent accidents and equipment damage.
-
Advantages of Induction Furnaces:
- Energy Efficiency: Induction furnaces generate heat directly within the metal charge, minimizing energy loss and making them highly efficient.
- Precision: The ability to precisely control the melting process allows for the production of alloys with exact compositions and properties.
- Cleanliness: Since the heat is generated within the metal, there is minimal contamination from external sources, resulting in cleaner melts.
- Speed: Induction furnaces can melt metals very quickly, reducing production times and increasing throughput.
In summary, the construction of an induction furnace is a sophisticated integration of electrical and mechanical components designed to efficiently and precisely melt metals. The power supply, induction coil, and crucible work in harmony to create a controlled environment where heat is generated directly within the metal charge, ensuring high efficiency, precision, and cleanliness in the melting process. The inclusion of a cooling system and advanced control mechanisms further enhances the performance and safety of the furnace, making it an essential tool in modern metallurgical applications.
Summary Table:
Component | Function |
---|---|
Power Supply | Generates high-frequency AC to create a magnetic field for induction heating. |
Induction Coil | Carries AC, creates a magnetic field, and induces eddy currents in the metal. |
Crucible | Holds the metal charge and withstands high temperatures without degrading. |
Metal Charge | Acts as the secondary winding of a transformer, generating heat when melted. |
Cooling System | Prevents overheating of the induction coil using water cooling. |
Control System | Regulates temperature, power, and cooling for precise and safe operation. |
Advantages | Energy efficiency, precision, cleanliness, and fast melting capabilities. |
Ready to optimize your metal melting process? Contact us today to learn more about induction furnaces!