Deposition in chemistry is a phase transition process where a gas transforms directly into a solid without passing through the liquid phase. This phenomenon is commonly observed in nature, such as frost forming on surfaces or the creation of cirrus clouds. In industrial and scientific contexts, deposition also refers to techniques like Chemical Vapor Deposition (CVD), where thin or thick layers of a material are deposited onto a substrate to modify its properties. This process is crucial in applications ranging from electronics to material science.
Key Points Explained:
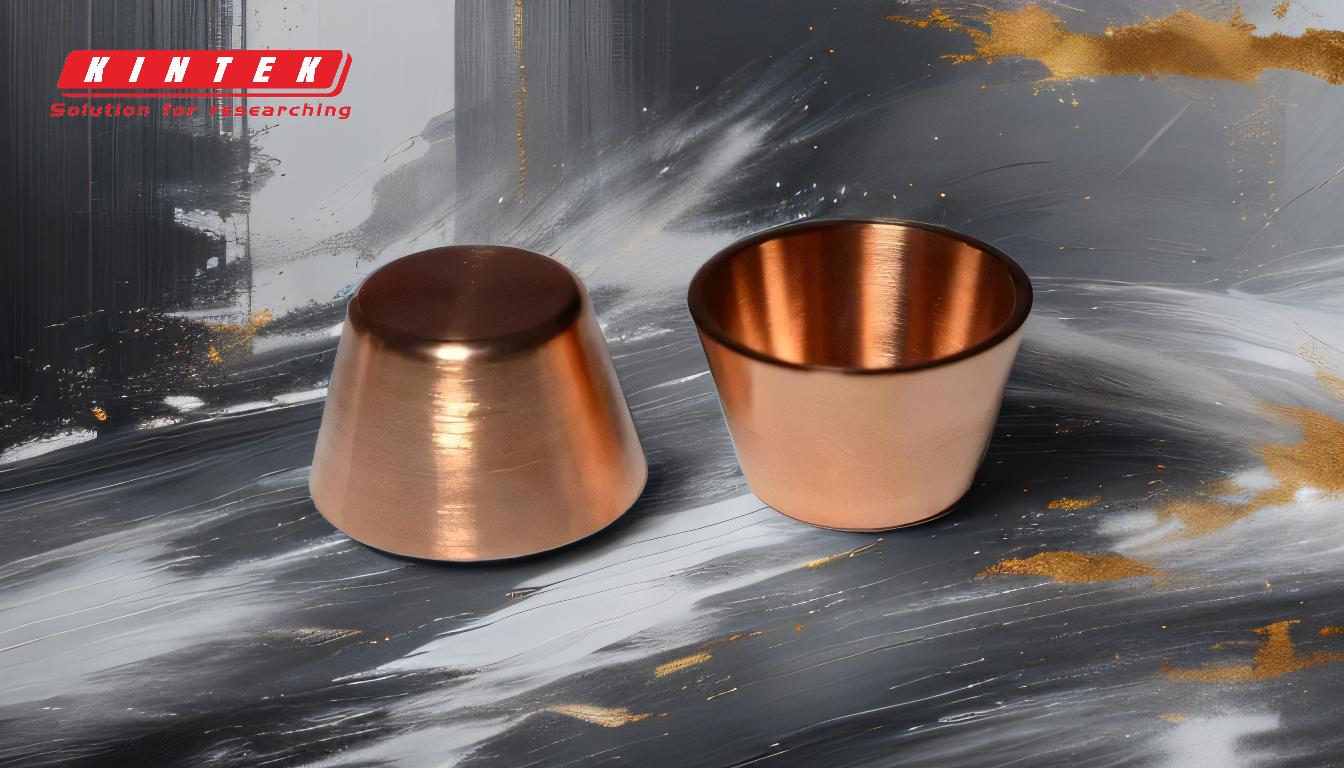
-
Definition of Deposition in Chemistry:
- Deposition is a phase transition where a gas changes directly into a solid, bypassing the liquid state.
- This process is the reverse of sublimation, where a solid turns directly into a gas.
-
Examples of Deposition in Nature:
- Frost Formation: Water vapor in the air directly forms ice crystals on cold surfaces, such as grass or windows, during freezing temperatures.
- Cirrus Clouds: High-altitude clouds composed of ice crystals form through the deposition of water vapor in the atmosphere.
-
Deposition in Industrial and Scientific Contexts (Chemical Vapor Deposition - CVD):
- Process Overview: CVD involves the deposition of thin or thick layers of a substance onto a solid surface, atom-by-atom or molecule by molecule.
-
Applications:
- Electronics: Used to create semiconductor devices, such as transistors and integrated circuits.
- Material Science: Enhances the properties of materials, such as hardness, corrosion resistance, or electrical conductivity.
- Coatings: Provides protective or functional coatings on various substrates.
-
How Deposition Works in CVD:
- A gaseous precursor is introduced into a reaction chamber.
- The gas undergoes a chemical reaction, often aided by heat, plasma, or catalysts, to form solid material.
- The solid material deposits onto the substrate, forming a uniform layer.
-
Importance of Deposition:
- Precision: Allows for the creation of highly controlled and uniform layers, essential for advanced technologies.
- Versatility: Can be applied to a wide range of materials and substrates.
- Innovation: Enables the development of new materials and devices with tailored properties.
By understanding deposition, both in natural and industrial contexts, we can appreciate its significance in both everyday phenomena and cutting-edge technologies.
Summary Table:
Aspect | Details |
---|---|
Definition | Phase transition where gas transforms directly into a solid. |
Natural Examples | - Frost formation: Ice crystals on surfaces. - Cirrus clouds: Ice crystals in the atmosphere. |
Industrial Applications | - Electronics: Semiconductor devices. - Material Science: Enhanced properties. - Coatings: Protective layers. |
CVD Process | - Gaseous precursor reacts to form solid material. - Deposits uniformly on substrates. |
Importance | - Precision in layer creation. - Versatility across materials. - Drives innovation in technology. |
Discover how deposition can revolutionize your projects—contact our experts today!