Induction heating and resistance heating are two distinct methods of generating heat, each with unique mechanisms and applications. Induction heating relies on electromagnetic induction to generate heat directly within a conductive material, while resistance heating uses the principle of electrical resistance to produce heat as current passes through a resistive element. Induction heating is contactless, highly efficient, and allows for precise control over heating depth and intensity. Resistance heating, on the other hand, involves direct contact with a heating element and is commonly used in applications like electric stoves and space heaters. The choice between the two depends on factors such as efficiency, precision, and the specific requirements of the application.
Key Points Explained:
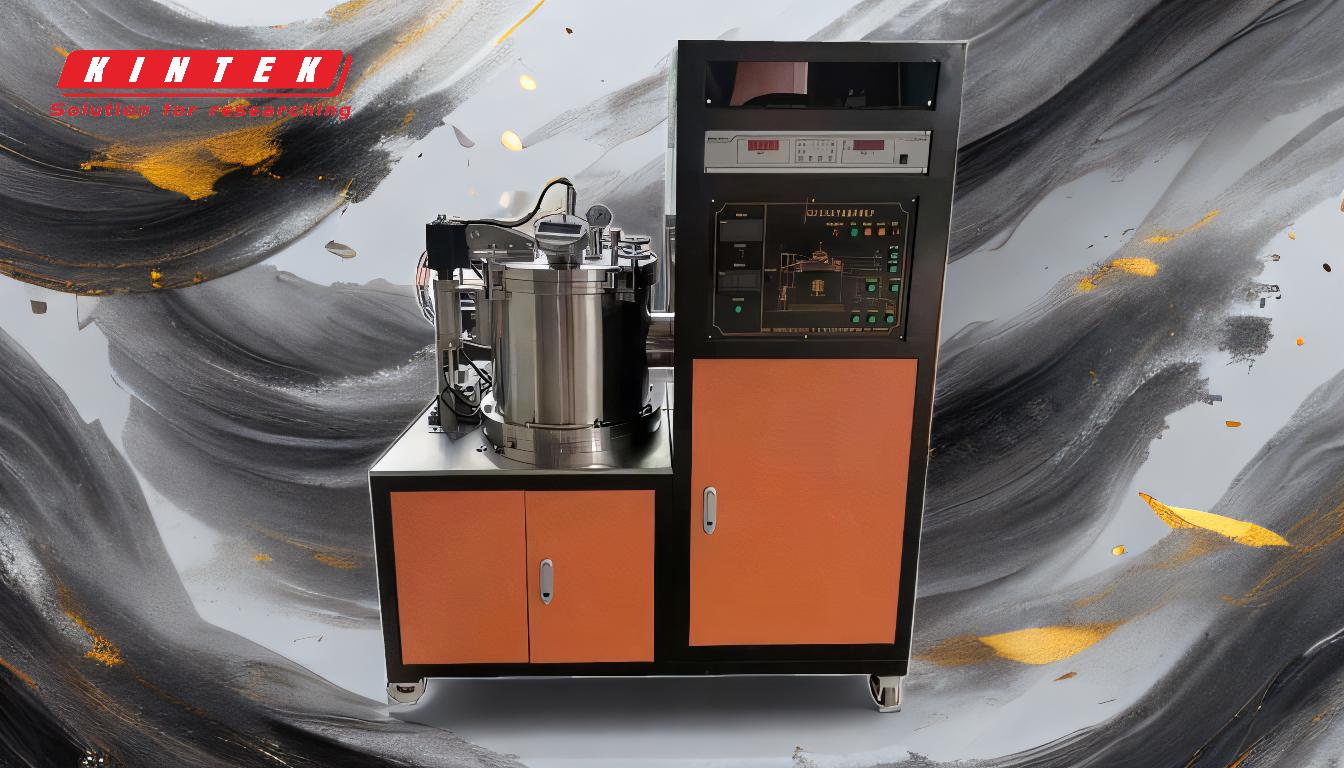
-
Mechanism of Heat Generation:
- Induction Heating: Heat is generated within the conductive material itself through electromagnetic induction. An alternating magnetic field induces eddy currents in the material, which produce heat due to electrical resistance.
- Resistance Heating: Heat is generated by passing an electric current through a resistive element, such as a metal coil or wire. The resistance of the material to the flow of electricity causes it to heat up.
-
Contact vs. Non-Contact Heating:
- Induction Heating: This method is contactless, meaning there is no physical contact between the heating source and the material being heated. This is particularly useful in applications where contamination must be avoided.
- Resistance Heating: Requires direct contact with the heating element. The heat is transferred to the material through conduction, which can lead to contamination or uneven heating in some cases.
-
Efficiency and Speed:
- Induction Heating: Known for its high efficiency and rapid heating capabilities. Since heat is generated directly within the material, there is minimal energy loss, and heating can be very fast.
- Resistance Heating: Generally less efficient due to energy losses in the form of heat dissipation from the resistive element to the surrounding environment. Heating speed can be slower compared to induction heating.
-
Precision and Control:
- Induction Heating: Offers precise control over the heating process, including the ability to heat specific depths within the material by adjusting the frequency of the alternating current. This makes it ideal for applications requiring localized heating.
- Resistance Heating: Less precise in terms of localized heating, as the entire resistive element heats up, and the heat is then transferred to the material. This can lead to less control over the heating depth and intensity.
-
Applications:
- Induction Heating: Widely used in industrial applications such as metal hardening, brazing, and annealing. It is also used in medical applications for sterilization and in domestic applications like induction cooktops.
- Resistance Heating: Commonly used in household appliances like electric stoves, space heaters, and toasters. It is also used in industrial applications where direct heating of materials is required.
-
Energy Source and Setup:
- Induction Heating: Requires an alternating current (AC) power source and an induction coil to generate the magnetic field. The setup can be more complex and costly compared to resistance heating.
- Resistance Heating: Typically uses direct current (DC) or alternating current (AC) and a simple resistive element. The setup is generally simpler and less expensive.
-
Heat Transfer Mechanism:
- Induction Heating: Heat is generated directly within the material, and the heat transfer occurs through thermal conduction within the material itself. This allows for more uniform heating and reduces the risk of overheating.
- Resistance Heating: Heat is generated in the resistive element and then transferred to the material through conduction, convection, or radiation. This can lead to uneven heating and potential hotspots.
-
Environmental and Safety Considerations:
- Induction Heating: Safer in terms of fire hazards and contamination, as there is no open flame or direct contact with the heating source. It is also more energy-efficient, reducing environmental impact.
- Resistance Heating: Can pose fire hazards if the resistive element overheats, and there is a risk of contamination from the heating element. It is generally less energy-efficient, leading to higher energy consumption and environmental impact.
In summary, induction heating and resistance heating differ fundamentally in their mechanisms, efficiency, precision, and applications. Induction heating is ideal for applications requiring rapid, precise, and contactless heating, while resistance heating is more suited for simpler, direct heating tasks. The choice between the two methods depends on the specific requirements of the application, including factors like efficiency, control, and safety.
Summary Table:
Aspect | Induction Heating | Resistance Heating |
---|---|---|
Mechanism | Heat generated via electromagnetic induction within the material. | Heat generated by electrical resistance in a resistive element. |
Contact | Contactless heating, no physical contact required. | Direct contact with the heating element. |
Efficiency | Highly efficient with minimal energy loss. | Less efficient due to heat dissipation. |
Precision | Precise control over heating depth and intensity. | Less precise, with potential for uneven heating. |
Applications | Metal hardening, brazing, annealing, medical sterilization, induction cooktops. | Electric stoves, space heaters, toasters, industrial direct heating. |
Energy Source | Requires AC power and an induction coil. | Uses DC or AC with a simple resistive element. |
Heat Transfer | Heat generated within the material for uniform heating. | Heat transferred via conduction, convection, or radiation. |
Safety | Safer, no open flame or contamination risk. | Risk of fire hazards and contamination from the heating element. |
Still unsure which heating method is right for your needs? Contact our experts today for personalized advice!