Fused Deposition Modeling (FDM) is a widely used additive manufacturing process where thermoplastic material is extruded through a heated nozzle and deposited layer by layer to create a three-dimensional object. The process involves precise horizontal movement of the nozzle and vertical movement of the build platform, allowing for the creation of complex geometries. FDM is known for its simplicity, cost-effectiveness, and versatility in material usage, making it a popular choice for prototyping, functional testing, and end-use part production.
Key Points Explained:
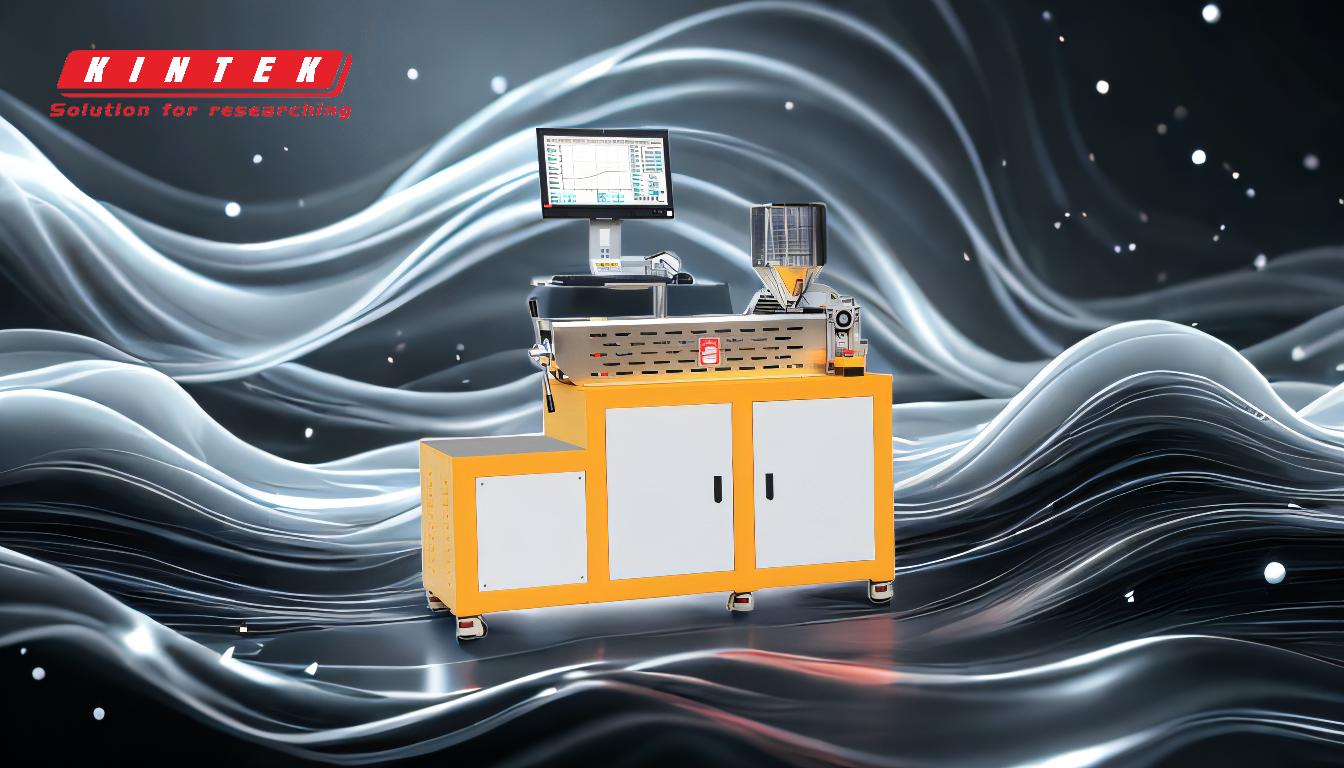
-
Definition and Overview of FDM:
- Fused Deposition Modeling (FDM) is a type of additive manufacturing process that builds objects layer by layer using thermoplastic materials.
- It is trademarked by Stratasys, but the term is often used generically to describe similar extrusion-based 3D printing technologies.
-
Material Extrusion Process:
- The process begins with a thermoplastic filament, which is fed into a heated nozzle.
- The nozzle heats the material to its melting point, allowing it to be extruded in a semi-liquid state.
- The extruded material is deposited onto a build platform in a controlled manner, following a predefined path based on the 3D model.
-
Layer-by-Layer Deposition:
- The nozzle moves horizontally to deposit material in the shape of the current layer.
- After each layer is completed, the build platform moves down (or the nozzle moves up) to allow for the deposition of the next layer.
- This layer-by-layer approach continues until the entire object is fully formed.
-
Movement and Precision:
- The nozzle is capable of precise horizontal movement, controlled by stepper motors or servo motors, ensuring accurate material placement.
- The vertical movement of the build platform is equally precise, allowing for consistent layer thickness and overall dimensional accuracy.
-
Materials Used in FDM:
- Common materials include ABS (Acrylonitrile Butadiene Styrene), PLA (Polylactic Acid), PETG (Polyethylene Terephthalate Glycol), and various engineering-grade thermoplastics.
- These materials are chosen based on their mechanical properties, thermal stability, and ease of extrusion.
-
Applications of FDM:
- Prototyping: FDM is widely used for creating prototypes due to its speed and cost-effectiveness.
- Functional Testing: Parts produced via FDM can be used for functional testing, as the materials can mimic the properties of final production parts.
- End-Use Parts: In some cases, FDM is used to produce end-use parts, especially when custom or low-volume production is required.
-
Advantages of FDM:
- Cost-Effective: FDM is one of the most affordable 3D printing technologies, making it accessible for small businesses and hobbyists.
- Material Versatility: A wide range of thermoplastic materials can be used, allowing for flexibility in material properties.
- Ease of Use: FDM printers are relatively easy to operate and maintain, making them suitable for users with varying levels of expertise.
-
Limitations of FDM:
- Surface Finish: Parts produced via FDM often have a rough surface finish, which may require post-processing for aesthetic or functional purposes.
- Layer Adhesion: The strength of FDM parts can be limited by the adhesion between layers, which may affect the overall mechanical performance.
- Speed: While FDM is faster than some other 3D printing methods, it can still be slower compared to traditional manufacturing processes for large or complex parts.
-
Post-Processing:
- Sanding and Polishing: To improve surface finish, FDM parts can be sanded and polished.
- Painting and Coating: Parts can be painted or coated to enhance their appearance or provide additional protection.
- Annealing: Some materials may benefit from annealing, a heat treatment process that can improve mechanical properties.
-
Future Developments in FDM:
- Material Innovations: Ongoing research is focused on developing new materials with enhanced properties, such as higher strength, better thermal resistance, and improved biocompatibility.
- Multi-Material Printing: Advances in FDM technology are enabling the use of multiple materials in a single print, allowing for more complex and functional parts.
- Increased Automation: Future FDM systems may incorporate more automation, such as automatic material changing and part removal, to further streamline the manufacturing process.
In summary, Fused Deposition Modeling (FDM) is a versatile and cost-effective 3D printing technology that uses thermoplastic extrusion to build objects layer by layer. Its simplicity, material versatility, and wide range of applications make it a popular choice for both prototyping and end-use part production. However, it does have limitations, such as surface finish quality and layer adhesion, which can be addressed through post-processing and ongoing technological advancements.
Summary Table:
Aspect | Details |
---|---|
Process | Layer-by-layer thermoplastic extrusion using a heated nozzle. |
Materials | ABS, PLA, PETG, and engineering-grade thermoplastics. |
Applications | Prototyping, functional testing, and end-use part production. |
Advantages | Cost-effective, material versatility, and ease of use. |
Limitations | Rough surface finish, layer adhesion issues, and slower speed for large parts. |
Post-Processing | Sanding, polishing, painting, coating, and annealing. |
Future Developments | New materials, multi-material printing, and increased automation. |
Discover how FDM can transform your prototyping process—contact us today for expert advice!