The heat treatment process for castings involves a series of controlled heating and cooling operations designed to alter the physical and mechanical properties of metallic alloys. This process is crucial for improving the material's hardness, strength, toughness, ductility, and elasticity, as well as reducing undesirable properties like magnetic permeability in certain environments. Heat treatment can be tailored to specific materials and applications, such as annealing to reduce magnetism in work-hardened metals like 1008 or 316, or vacuum heat treatment to enhance corrosion resistance and mechanical strength. The process is essential for ensuring that castings meet the required performance standards for their intended use.
Key Points Explained:
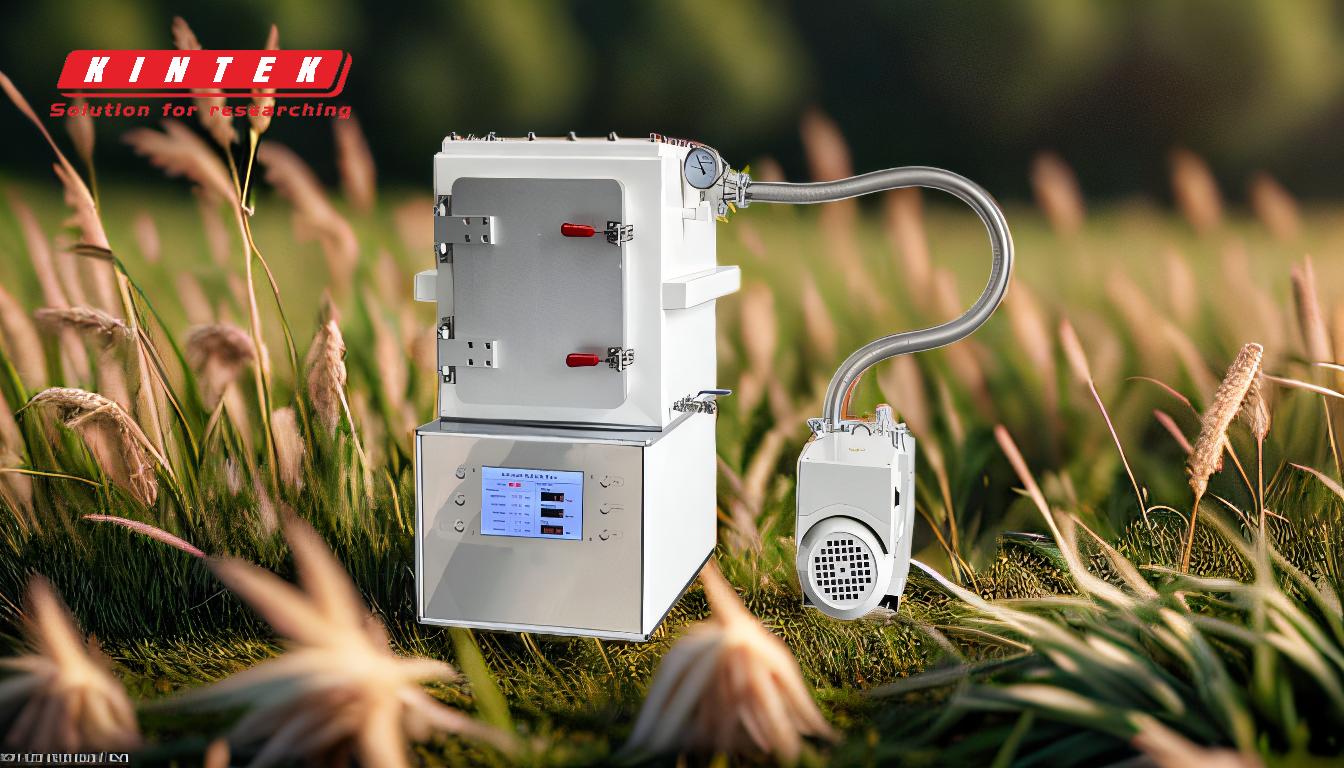
-
Purpose of Heat Treatment for Castings:
- Heat treatment is used to modify the mechanical and physical properties of castings, ensuring they meet specific performance criteria.
- It can improve hardness, strength, toughness, ductility, and elasticity, while also addressing issues like magnetic permeability in certain materials.
-
Annealing to Reduce Magnetic Permeability:
- Materials such as 1008 or 316 can become magnetic when work-hardened through processes like machining, forming, or bending.
- Annealing is a heat treatment process that reduces magnetic permeability, making the material more suitable for electronic environments where magnetism is undesirable.
-
Control of Microstructural Changes:
- Heat treatment works by controlling the rate of diffusion and cooling within the metal's microstructure.
- This manipulation of the microstructure allows for precise adjustments to the material's properties, such as increasing hardness or improving ductility.
-
Vacuum Heat Treatment for Enhanced Properties:
- Vacuum heat treatment is a specialized process that improves the chemical and mechanical properties of metals.
- Benefits include increased resistance to corrosion, higher hardness and elasticity, and improved shear strength, making the treated metals suitable for more demanding applications.
-
Applications of Heat-Treated Castings:
- Heat-treated castings are used in a wide range of industries, including automotive, aerospace, electronics, and manufacturing.
- The process ensures that castings can withstand the stresses and environmental conditions they will encounter in their specific applications.
-
Customization for Specific Materials:
- The heat treatment process can be customized based on the type of metal and its intended use.
- For example, annealing is particularly effective for reducing magnetism in stainless steels, while vacuum heat treatment is ideal for enhancing the properties of high-performance alloys.
By understanding and applying these key points, manufacturers can optimize the heat treatment process for castings, ensuring they achieve the desired properties and performance for their specific applications.
Summary Table:
Key Aspect | Details |
---|---|
Purpose | Improves hardness, strength, toughness, ductility, and elasticity. |
Annealing | Reduces magnetic permeability in work-hardened metals like 1008 or 316. |
Microstructural Control | Adjusts material properties by controlling diffusion and cooling rates. |
Vacuum Heat Treatment | Enhances corrosion resistance, hardness, elasticity, and shear strength. |
Applications | Used in automotive, aerospace, electronics, and manufacturing industries. |
Customization | Tailored for specific materials and applications for optimal performance. |
Optimize your castings with expert heat treatment solutions—contact us today!