The heat treatment process of quench hardening involves heating a metal to a specific temperature, holding it at that temperature to achieve uniform heating, and then rapidly cooling it (quenching) to achieve desired mechanical properties such as increased hardness and strength. This process is critical for enhancing the durability and performance of metal components. The controlled atmosphere during heat treatment prevents oxidation and decarburization, ensuring the workpiece retains its integrity. Quench hardening is widely used in industries requiring high-strength components, such as automotive and aerospace.
Key Points Explained:
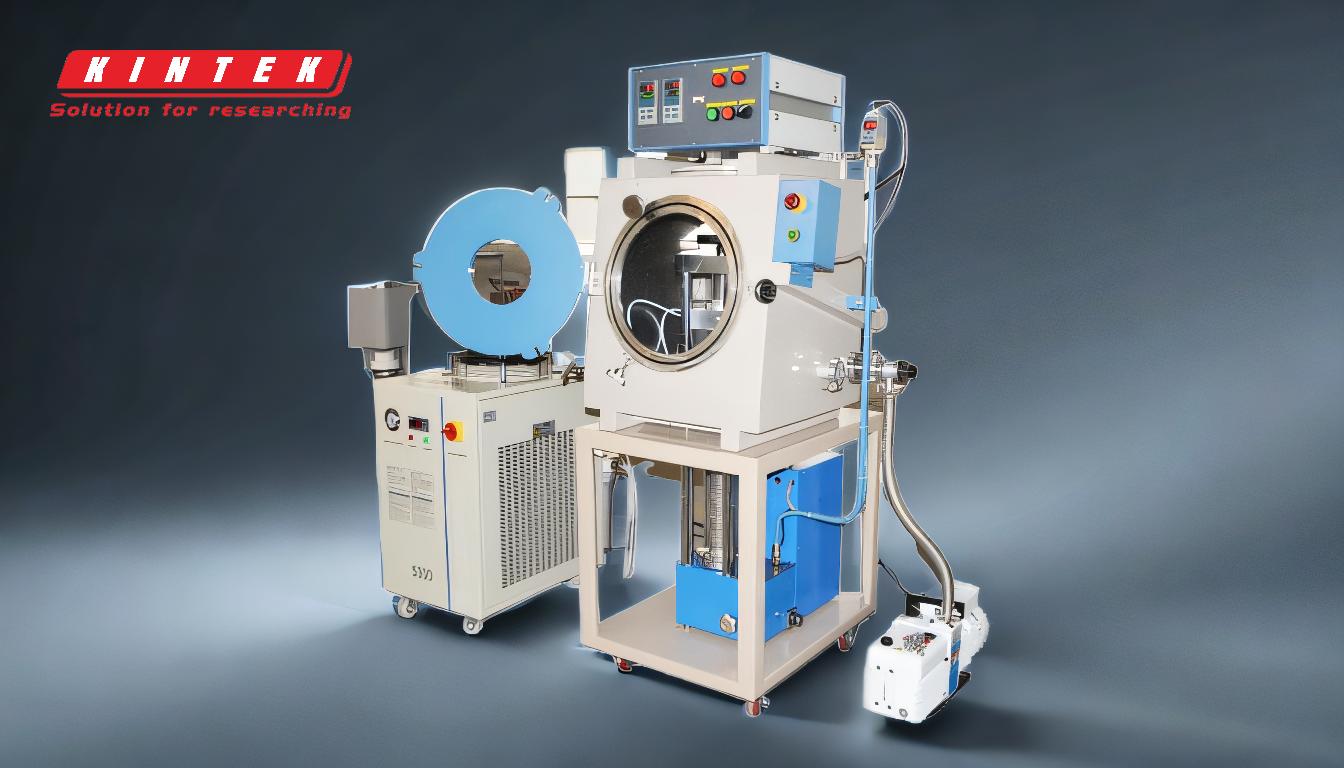
-
Heating the Metal:
- The metal is heated to a temperature above its critical transformation point, typically between 800°C and 900°C for steel. This temperature ensures the metal's microstructure transforms into austenite, a phase that allows for uniform hardening.
- The heating process is often conducted in a controlled atmosphere to prevent oxidation and decarburization. This is achieved by regulating the levels of O2, CO, and water vapor in the chamber.
-
Holding at Temperature:
- Once the metal reaches the desired temperature, it is held at that temperature for a specific duration. This ensures uniform heating throughout the workpiece, which is critical for achieving consistent mechanical properties after quenching.
- The holding time depends on the material's thickness and composition. Thicker materials require longer holding times to ensure even heat distribution.
-
Quenching:
- After the holding period, the metal is rapidly cooled by immersing it in a quenching medium such as water, oil, or polymer solutions. The rapid cooling locks the austenite phase into martensite, a hard and brittle microstructure.
- The choice of quenching medium depends on the material and the desired hardness. Water provides the fastest cooling rate, while oil offers a slower cooling rate, reducing the risk of cracking.
-
Controlled Atmosphere:
- A controlled atmosphere is essential during the heating phase to prevent oxidation and decarburization. Oxidation can lead to surface scaling, while decarburization reduces the carbon content on the surface, weakening the material.
- The atmosphere is carefully regulated to maintain low levels of oxygen and moisture, ensuring the workpiece remains free from defects.
-
Applications and Benefits:
- Quench hardening is widely used in industries requiring high-strength components, such as automotive, aerospace, and tool manufacturing. It enhances the wear resistance, hardness, and overall durability of metal parts.
- The process can be combined with other heat treatment methods, such as tempering, to achieve a balance between hardness and toughness.
-
Role of Equipment:
- Specialized equipment, such as furnaces and quenching tanks, is used to ensure precise control over temperature and cooling rates. For example, a horizontal shaker can be used to agitate the quenching medium, ensuring uniform cooling and minimizing distortion.
- Advanced techniques like induction heating utilize the skin effect to achieve localized heating, making the process more efficient for specific applications.
By following these steps, quench hardening transforms the microstructure of metals, resulting in components with superior mechanical properties and extended service life.
Summary Table:
Step | Details |
---|---|
Heating the Metal | Heat to 800°C–900°C in a controlled atmosphere to transform microstructure. |
Holding at Temperature | Maintain temperature for uniform heating and consistent properties. |
Quenching | Rapidly cool in water, oil, or polymer to lock in hardness. |
Controlled Atmosphere | Prevent oxidation and decarburization for defect-free results. |
Applications | Used in automotive, aerospace, and tool manufacturing for high-strength parts. |
Equipment | Furnaces, quenching tanks, and advanced techniques like induction heating. |
Discover how quench hardening can optimize your metal components—contact our experts today!