The hot isostatic pressing (HIP) process is a manufacturing technique that combines high temperature and high pressure to improve the properties of materials. It involves loading parts or components into a heating chamber, where inert argon gas is applied. The chamber heats up, and the temperature, pressure, and total process time are closely monitored and controlled. The process ends with a depressurization phase and a cool-down period to ensure the parts are safe to remove. HIP enhances material properties such as wear resistance, corrosion resistance, and mechanical performance, and can increase fatigue life by 10 to 100 times. It also enables the bonding of two or more materials together, either in solid or powder form.
Key Points Explained:
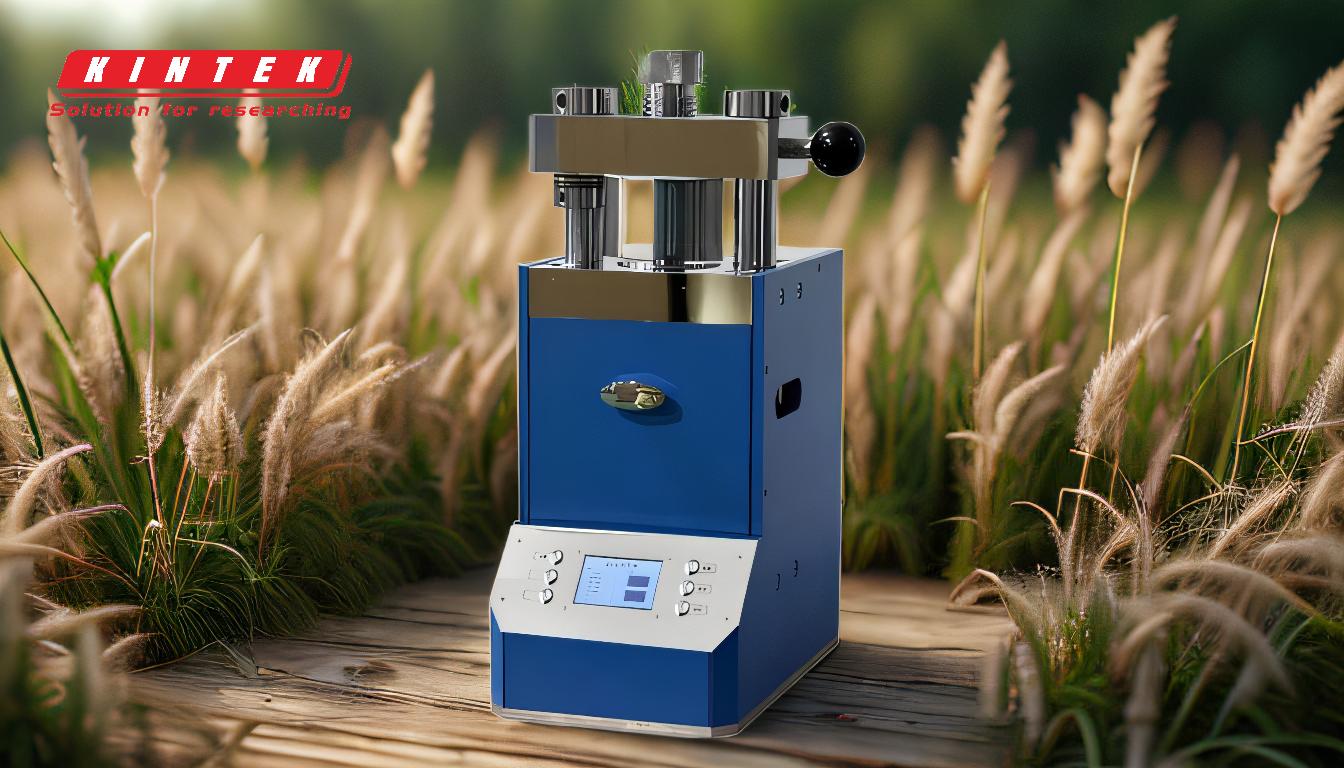
-
Process Overview:
- The hot isostatic pressing process involves loading parts or components into a heating chamber.
- Inert argon gas is applied, and the chamber heats up.
- Temperature, pressure, and total process time are closely monitored and controlled.
- The process ends with a depressurization phase and a cool-down period to ensure the parts are safe to remove.
-
Uniform Pressure Application:
- During Hot Isostatic Pressing, pressure is applied uniformly to a material from all directions using an inert gas, such as Argon, in a pressurized vessel.
- Heat is applied to the containment chamber to increase the pressure over time, typically below the melting point of the material.
- The simultaneous application of heat and pressure on all surfaces of the material helps eliminate small gaps (pores), increasing density and uniform composition.
-
Material Property Enhancement:
- Hot isostatic pressing treatment improves material properties such as wear resistance, corrosion resistance, and mechanical performance.
- It can increase fatigue life by 10 to 100 times and results in a material density close to the theoretical density.
-
Bonding and Cladding:
- Hot isostatic pressing enables the bonding, or cladding, of two or more materials together, either in solid or powder form.
-
Techniques:
- Isostatic pressing can be done using either the wet-bag technique, where the flexible bag containing the powder is submerged in a pressure vessel with pressurising fluid, or the dry-bag technique, where the flexible bag is fixed in the pressure vessel and powder is loaded without removing the bag.
-
Warm Isostatic Press:
- A warm isostatic press is usually heated to the temperature of the liquid medium first.
- Then, through a booster source, the heated liquid medium is continuously injected into the sealed pressing cylinder.
- The pressing cylinder is equipped with a heat generator to ensure accurate temperature control.
By understanding these key points, one can appreciate the complexity and benefits of the hot isostatic pressing process, making it a valuable technique in material science and manufacturing.
Summary Table:
Key Aspect | Description |
---|---|
Process Overview | Combines high temperature and pressure using inert argon gas in a heating chamber. |
Uniform Pressure Application | Pressure applied uniformly from all directions, eliminating pores and increasing density. |
Material Property Enhancement | Improves wear resistance, corrosion resistance, and fatigue life by 10-100 times. |
Bonding and Cladding | Enables bonding of two or more materials in solid or powder form. |
Techniques | Uses wet-bag or dry-bag techniques for isostatic pressing. |
Warm Isostatic Press | Heats liquid medium first, ensuring precise temperature control. |
Want to enhance your materials with hot isostatic pressing? Contact our experts today!