A muffle furnace capable of reaching 1800°C is a high-temperature furnace designed for applications requiring extreme heat in a controlled environment. It is commonly used in industries such as ceramics, metallurgy, glass, and semiconductor manufacturing, as well as in laboratories for material testing and research. The furnace isolates materials from combustion byproducts, ensuring precise and contamination-free heating. Applications include sintering, heat treatment, ash content analysis, and high-temperature material testing. For temperatures exceeding 1800°C, specialized furnaces like cold wall furnaces are required, especially when using gases like hydrogen. The muffle furnace's versatility and precision make it indispensable for high-temperature processes.
Key Points Explained:
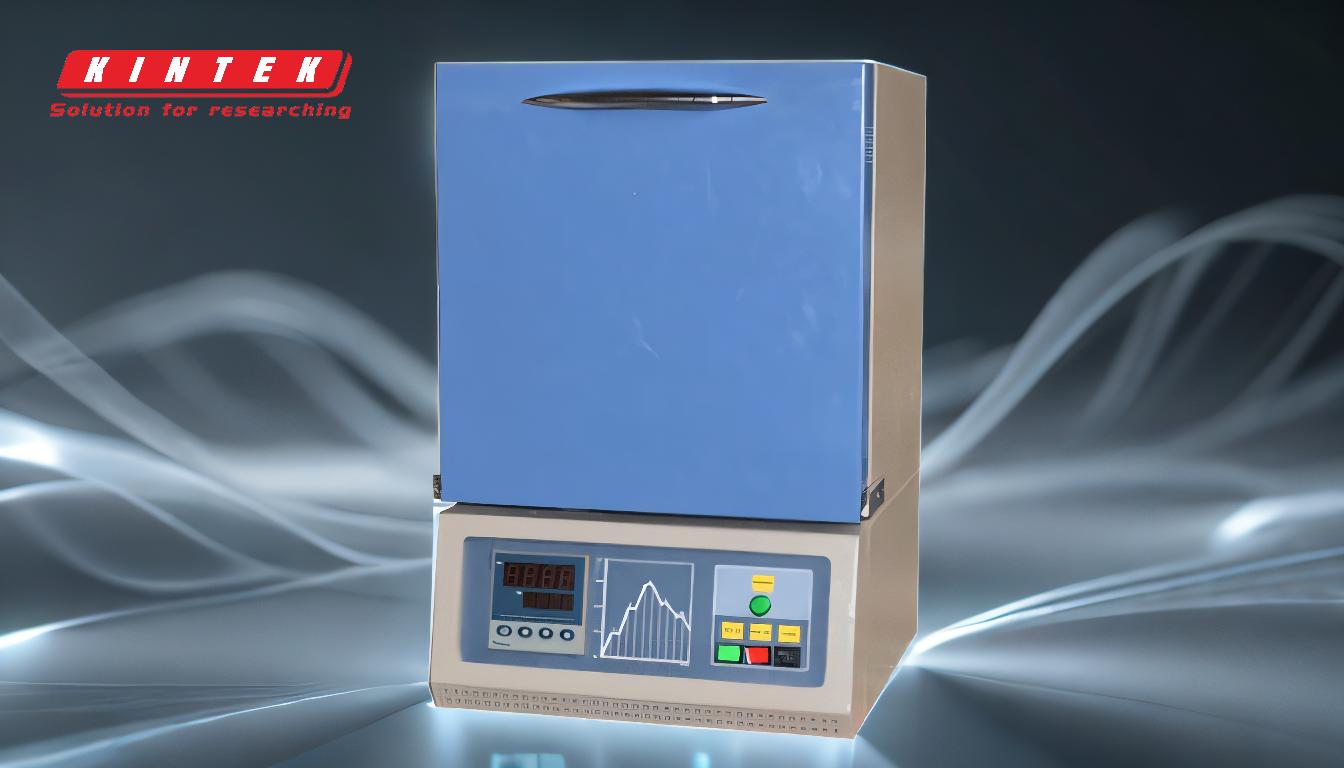
-
Definition and Purpose of a Muffle Furnace:
- A muffle furnace is a high-temperature heating device used to heat materials uniformly without exposing them to direct flame or combustion byproducts.
- The 1800°C variant is designed for extreme heat applications, making it suitable for processes like sintering, annealing, and material testing.
-
Key Applications:
- Material Testing and Research: Used to determine ash content, analyze chemical properties of materials, and conduct high-temperature experiments.
- Industrial Processes: Essential in industries like ceramics, glass, metallurgy, and semiconductors for processes such as melting, sintering, and heat treatment.
- Laboratory Use: Employed for drug inspections, medical sample pretreatment, and quality control in various industries.
-
Temperature Capabilities:
- The 1800°C muffle furnace is ideal for applications requiring extreme heat, such as sintering ceramics or melting glass.
- For processes requiring temperatures above 1800°C, specialized furnaces like cold wall furnaces are necessary, particularly when using reactive gases like hydrogen.
-
Design and Features:
- Insulation and Heating Elements: Designed with advanced insulation materials and high-performance heating elements to withstand extreme temperatures.
- Controlled Atmosphere: Some models allow the introduction of inert gases (e.g., nitrogen, argon) to create a controlled environment for specific applications.
-
Industries and Use Cases:
- Ceramics and Glass: Used for sintering, melting, and shaping materials.
- Metallurgy: Employed for heat treatment processes like annealing, tempering, and normalizing.
- Semiconductors and Petrochemicals: Essential for material research and quality control.
-
Safety and Precision:
- The muffle furnace ensures precise temperature control, critical for achieving consistent results in high-temperature processes.
- Its design minimizes contamination, making it ideal for applications requiring purity, such as drug inspections and nuclear fuel disposal.
-
Specialized Requirements:
- For applications involving hydrogen or other reactive gases at temperatures above 1800°C, cold wall furnaces are recommended to ensure safety and performance.
By combining high-temperature capabilities with precise control, the 1800°C muffle furnace is a versatile tool for industries and laboratories requiring reliable and contamination-free heating solutions.
Summary Table:
Feature | Details |
---|---|
Temperature Range | Up to 1800°C, ideal for extreme heat applications |
Applications | Sintering, heat treatment, ash content analysis, material testing |
Industries | Ceramics, glass, metallurgy, semiconductors, petrochemicals, laboratories |
Key Features | Precise temperature control, contamination-free heating, inert gas options |
Specialized Use Cases | Requires cold wall furnaces for temperatures above 1800°C or reactive gases |
Looking for a reliable 1800°C muffle furnace? Contact us today to find the perfect solution for your high-temperature needs!