A furnace operates on the principle of generating and transferring heat to materials or products for industrial processes. It achieves this through the combustion of fuels or gases, which produces heat. This heat is then transferred to the target materials either directly (through direct contact with flames or hot gases) or indirectly (through heat exchangers or radiant heating). Furnaces are designed to handle high temperatures, typically exceeding 752 °F (400 °C), making them suitable for processes like metal smelting, glass manufacturing, and chemical reactions. The efficiency and design of a furnace depend on factors such as fuel type, combustion method, and heat transfer mechanisms.
Key Points Explained:
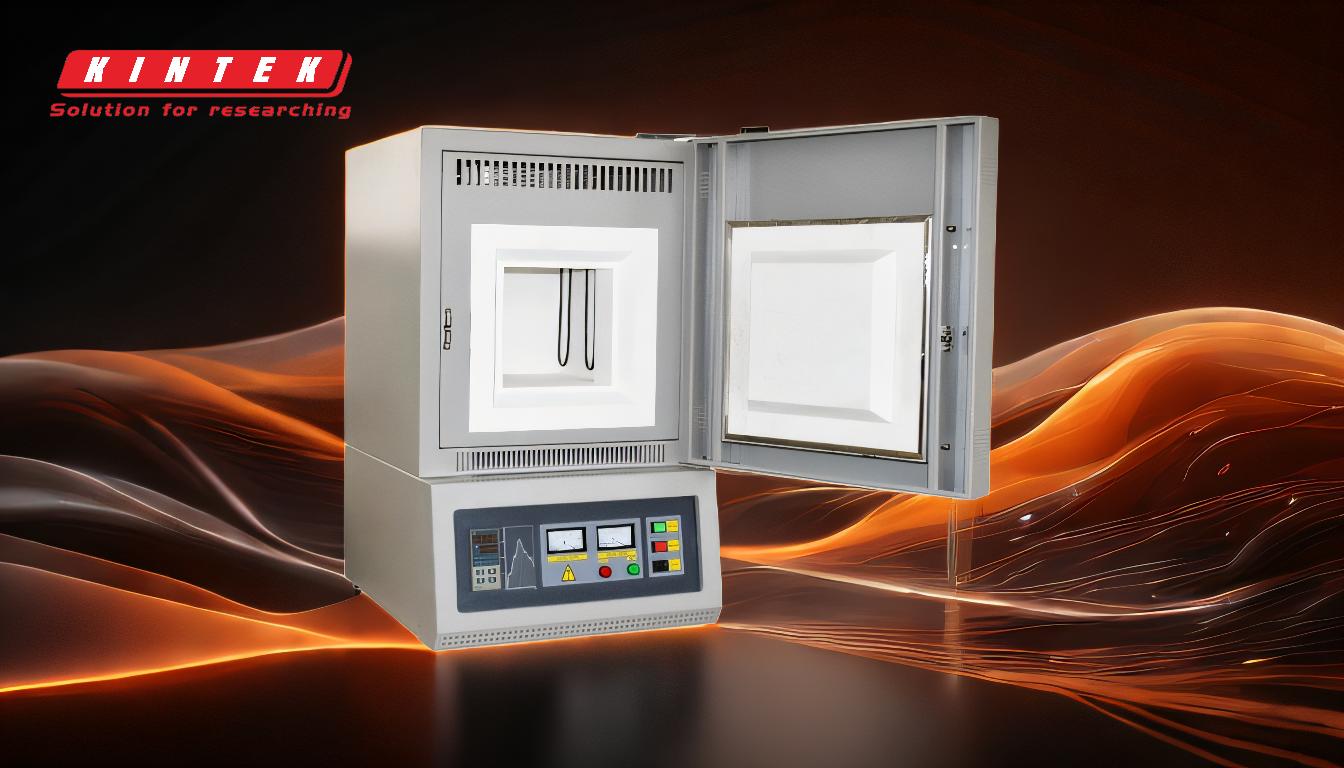
-
Heat Generation Through Combustion:
- Furnaces generate heat by burning fuels such as natural gas, oil, coal, or other combustible materials. This process releases energy in the form of heat.
- The combustion process involves mixing the fuel with an oxidizer (usually air) and igniting it. The chemical reaction produces hot gases and radiant energy.
- The efficiency of combustion depends on factors like fuel quality, air-to-fuel ratio, and burner design.
-
Heat Transfer Mechanisms:
- Direct Heat Transfer: In this method, the material being heated comes into direct contact with the flames or hot gases produced by combustion. This is common in processes like metal smelting or glass melting.
- Indirect Heat Transfer: Here, heat is transferred to the material through an intermediary, such as a heat exchanger or radiant heating elements. This is used in processes where direct contact with flames could contaminate or damage the material.
-
Temperature Control:
- Furnaces are designed to operate at high temperatures, often exceeding 752 °F (400 °C). Temperature control is critical for ensuring the desired chemical or physical changes in the material.
- Advanced furnaces use sensors, thermocouples, and control systems to maintain precise temperature levels. This ensures consistent results and prevents overheating or underheating.
-
Applications of Furnaces:
- Furnaces are used in various industries, including metallurgy (e.g., steel production), glass manufacturing, ceramics, and chemical processing.
- They are essential for processes like annealing, tempering, sintering, and calcination, where controlled high-temperature environments are required.
-
Types of Furnaces:
- Batch Furnaces: These are used for heating a specific quantity of material at a time. They are ideal for small-scale or customized processes.
- Continuous Furnaces: These are designed for large-scale production, where materials move through the furnace on conveyors or rollers, ensuring a steady flow of heated products.
-
Energy Efficiency and Environmental Considerations:
- Modern furnaces are designed to maximize energy efficiency by optimizing combustion and heat transfer processes.
- Environmental regulations often require furnaces to include features like emissions control systems (e.g., scrubbers or filters) to reduce pollutants released during combustion.
By understanding these principles, a purchaser can evaluate furnace designs based on their specific industrial needs, ensuring optimal performance, energy efficiency, and compliance with environmental standards.
Summary Table:
Key Aspect | Description |
---|---|
Heat Generation | Combustion of fuels (natural gas, oil, coal) produces heat and hot gases. |
Heat Transfer | Direct (flame contact) or indirect (heat exchangers) methods for material heating. |
Temperature Control | Sensors and control systems maintain precise temperatures above 752 °F (400 °C). |
Applications | Used in metallurgy, glass manufacturing, ceramics, and chemical processing. |
Types of Furnaces | Batch (small-scale) or continuous (large-scale) furnaces. |
Energy Efficiency | Optimized combustion and heat transfer for reduced energy consumption. |
Environmental Features | Emissions control systems (e.g., scrubbers) to minimize pollutants. |
Need a furnace tailored to your industrial needs? Contact our experts today for a customized solution!