The process of making rubber sheets involves several key stages, starting from the preparation of raw materials to the final vulcanization process. The primary steps include compounding, where raw rubber is mixed with additives to achieve desired properties, followed by calendering, which shapes the rubber into sheets using heavy rollers. The calendering process often involves combining rubber with fabrics or other materials. Finally, the rubber sheets undergo vulcanization to enhance their durability and elasticity. Each step is crucial in ensuring the final product meets specific quality and performance standards.
Key Points Explained:
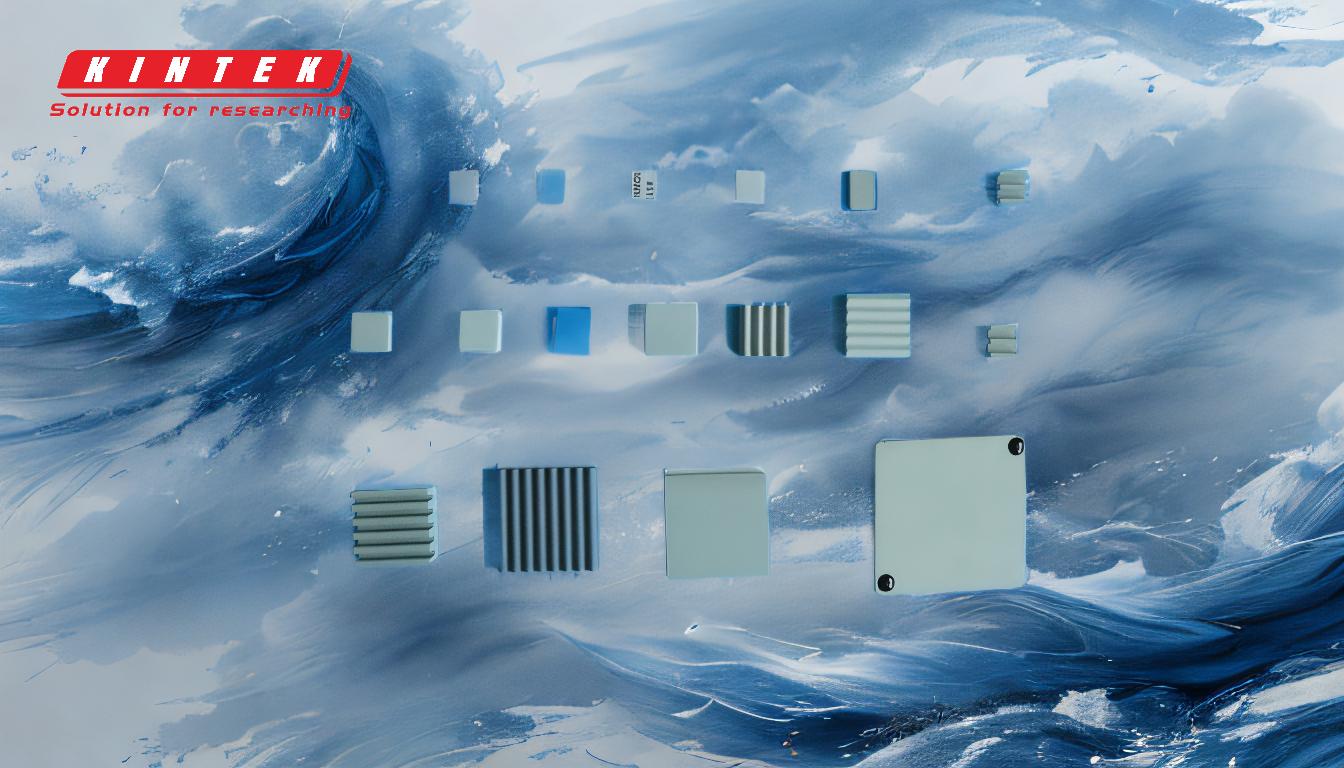
-
Compounding:
- Compounding is the first step in rubber sheet manufacturing. It involves mixing raw rubber with various additives such as fillers, plasticizers, curing agents, and accelerators. This process is essential to achieve the desired physical and chemical properties of the rubber, such as elasticity, strength, and resistance to environmental factors.
- The compounding process typically takes place in a mixer, where the ingredients are thoroughly blended to ensure uniformity. The compounded rubber is then ready for the next stage of processing.
-
Calendering:
- Calendering is the process of shaping the compounded rubber into sheets. This is done using a rubber calender, which consists of heavy rollers that press the rubber into thin, uniform sheets. The calendering process can also involve combining rubber with fabrics or other materials, a process known as frictioning or combining.
- The calendering machine uses horizontal rollers to pass the rubber material through, ensuring that the sheets are of consistent thickness and quality. This step is crucial for producing rubber sheets that are suitable for various applications, such as in the automotive, construction, and industrial sectors.
-
Vulcanization:
- Vulcanization is the final step in the rubber sheet manufacturing process. It involves heating the rubber sheets in the presence of sulfur or other curing agents to create cross-links between the polymer chains. This process enhances the rubber's mechanical properties, such as tensile strength, elasticity, and resistance to heat and chemicals.
- Vulcanization can be carried out using various methods, including hot air vulcanization, steam vulcanization, and microwave vulcanization. The choice of method depends on the specific requirements of the rubber product being manufactured.
-
Quality Control:
- Throughout the manufacturing process, quality control is essential to ensure that the rubber sheets meet the required specifications. This includes monitoring the compounding process to ensure the correct mix of ingredients, checking the thickness and uniformity of the sheets during calendering, and verifying the vulcanization process to ensure the rubber has the desired properties.
- Quality control measures may include visual inspections, mechanical testing, and chemical analysis. Any deviations from the specified standards are corrected to ensure the final product meets the desired quality and performance criteria.
-
Applications of Rubber Sheets:
- Rubber sheets produced through this process are used in a wide range of applications. They are commonly used as gaskets, seals, and insulation materials in the automotive and construction industries. They are also used in the production of conveyor belts, flooring, and protective coatings.
- The specific properties of the rubber sheets, such as their thickness, elasticity, and resistance to environmental factors, determine their suitability for different applications. The manufacturing process is tailored to produce rubber sheets that meet the specific requirements of each application.
By following these key steps, manufacturers can produce high-quality rubber sheets that meet the diverse needs of various industries. Each stage of the process, from compounding to vulcanization, plays a critical role in ensuring the final product's performance and durability.
Summary Table:
Step | Description | Key Details |
---|---|---|
Compounding | Mixing raw rubber with additives to achieve desired properties. | Additives include fillers, plasticizers, curing agents, and accelerators. |
Calendering | Shaping rubber into sheets using heavy rollers, often combined with fabrics. | Ensures uniform thickness and quality for applications like gaskets and seals. |
Vulcanization | Heating rubber with sulfur to enhance durability, elasticity, and strength. | Methods include hot air, steam, and microwave vulcanization. |
Quality Control | Monitoring each step to ensure specifications are met. | Includes visual inspections, mechanical testing, and chemical analysis. |
Applications | Used in automotive, construction, and industrial sectors for various purposes. | Examples include conveyor belts, flooring, and protective coatings. |
Need high-quality rubber sheets for your industry? Contact our experts today to learn more about our manufacturing solutions!