The sintering process in the steel industry is a critical step in transforming powdered metals, particularly iron ore, into a solid, durable material suitable for use in blast furnaces. This process involves several stages, including powder preparation, compaction, and heating in a sintering furnace to bond particles without melting them. The result is a thermally resistant, open-grained material called sinter, which is ideal for steel production. The process is energy-efficient and allows for precise control over the material's properties, making it a cornerstone of modern steel manufacturing.
Key Points Explained:
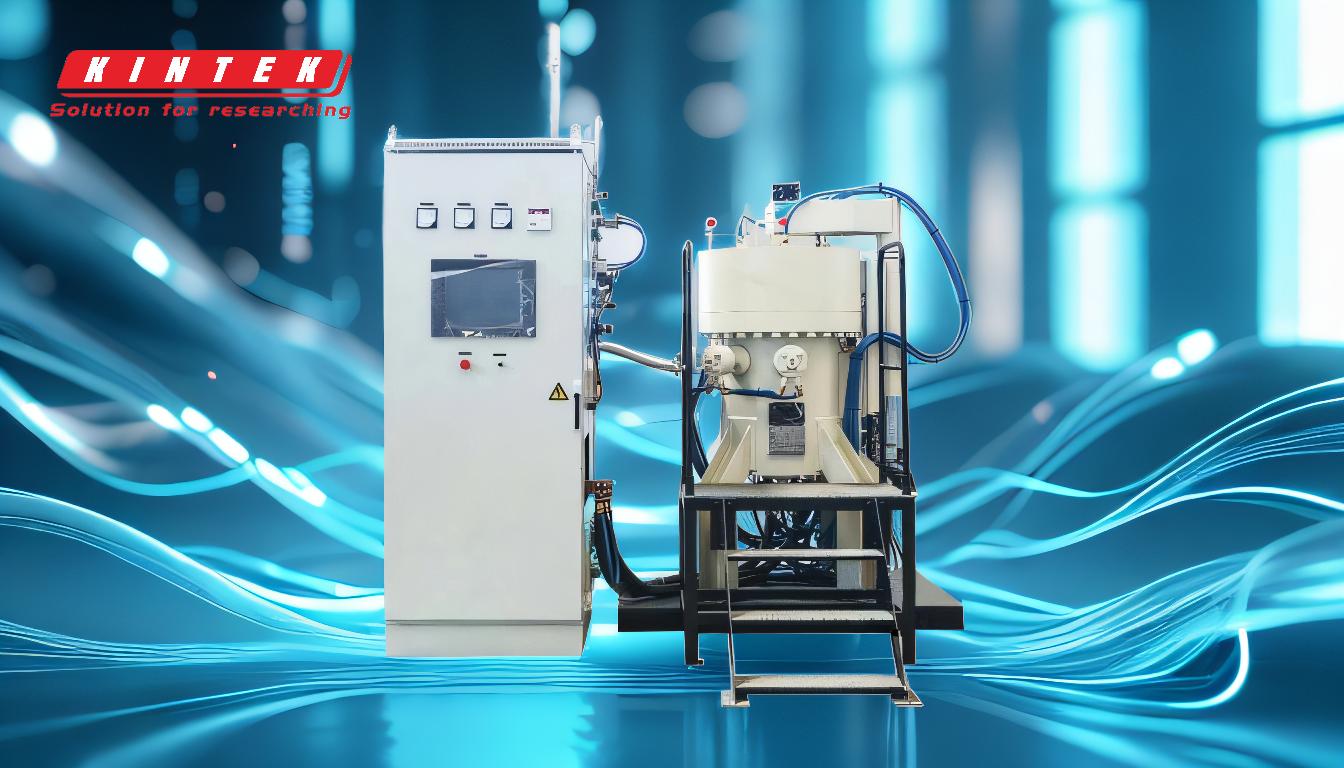
-
Definition and Purpose of Sintering in the Steel Industry:
- Sintering is a process that converts powdered metals, such as iron ore, into a solid mass by heating the material below its melting point. This process is essential in the steel industry because it creates sinter, a material with consistent properties that is optimal for use in blast furnaces. Sintering improves the efficiency of steel production by enhancing the material's thermal resistance and structural integrity.
-
Stages of the Sintering Process:
-
Powder Preparation:
- The process begins with the preparation of raw materials, including iron ore powder, fluxes, and recycled substances from the steel plant. These materials are mixed to create a homogeneous blend.
-
Compaction:
- The powder mixture is then compacted using mechanical methods, such as cold or hot pressing, to form a "green part." This step ensures the material has the desired shape and density before sintering.
-
Sintering:
- The green part is placed in a sintering furnace, where it is heated to a temperature just below the melting point of the metal. This causes the particles to bond together through solid-state diffusion, forming a solid, cohesive mass.
-
Cooling and Screening:
- After sintering, the material is cooled and screened to remove dust and ensure uniformity. The final product, sinter, is then ready for use in blast furnaces.
-
Powder Preparation:
-
Role of the Sintering Furnace:
- The sintering furnace is a critical component of the process. It provides the controlled environment needed to heat the material uniformly and achieve the desired bonding of particles. The furnace operates below the melting point of the metal, ensuring that the material retains its shape while becoming more durable.
-
Advantages of Sintering in Steel Production:
- Energy Efficiency: Sintering requires less energy than melting, making it a cost-effective method for producing high-quality materials.
- Material Consistency: The process allows for precise control over the composition and properties of the sinter, ensuring consistent performance in blast furnaces.
- Recycling: Sintering incorporates recycled materials from the steel plant, reducing waste and promoting sustainability.
-
Applications of Sintered Materials:
- Sintered materials, particularly sintered iron ore, are primarily used in blast furnaces for steel production. The open-grained structure of sinter allows for efficient gas flow and heat transfer, making it ideal for this application.
-
Variations in the Sintering Process:
- Depending on the desired properties of the final product, additional steps such as liquid phase sintering (LPS) or the addition of binders and lubricants may be incorporated. These variations can enhance the density and strength of the sintered material.
By understanding the sintering process and the role of the sintering furnace, manufacturers can optimize steel production, reduce costs, and improve the quality of the final product. This process is a testament to the innovative techniques that drive the steel industry forward.
Summary Table:
Stage | Description |
---|---|
Powder Preparation | Mixing iron ore powder, fluxes, and recycled materials to create a homogeneous blend. |
Compaction | Compressing the powder mixture to form a 'green part' with desired shape and density. |
Sintering | Heating the green part in a sintering furnace to bond particles without melting. |
Cooling and Screening | Cooling and screening the sintered material to ensure uniformity and remove dust. |
Advantages | Benefits |
Energy Efficiency | Requires less energy than melting, making it cost-effective. |
Material Consistency | Ensures precise control over sinter properties for consistent performance. |
Recycling | Incorporates recycled materials, promoting sustainability. |
Optimize your steel production with advanced sintering solutions—contact our experts today!