An annealing oven, also known as an annealing furnace, is a specialized piece of equipment used in the heat treatment process for materials like glass and soft metals. Its primary purpose is to alter the physical and sometimes chemical properties of these materials to achieve desired characteristics such as reduced hardness, increased ductility, and the elimination of internal stresses. This is accomplished by heating the material to a specific temperature and then allowing it to cool at a controlled, slow rate. The process is crucial in industries where material strength, durability, and workability are essential.
Key Points Explained:
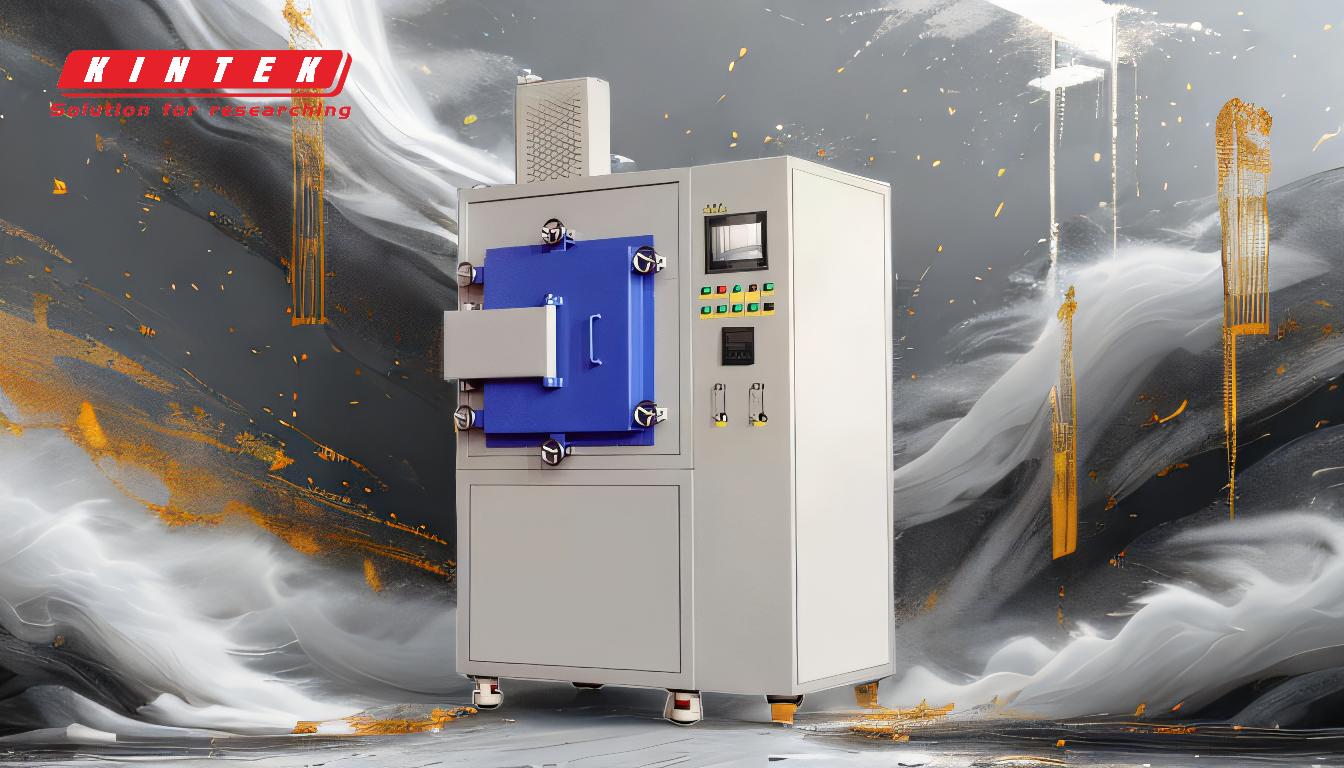
-
Purpose of Annealing:
- Annealing is a heat treatment process designed to modify the properties of materials, particularly glass and soft metals. The process aims to reduce hardness, increase ductility, and eliminate internal stresses within the material. This makes the material more workable and less prone to cracking or breaking under stress.
-
Function of an Annealing Oven:
- An annealing oven is specifically designed to facilitate the annealing process. It heats the material to a precise temperature, which is critical for achieving the desired material properties. The oven then allows the material to cool slowly, which is essential for the successful completion of the annealing process. The controlled environment of the oven ensures uniform heating and cooling, which is crucial for consistent results.
-
Applications of Annealing Ovens:
- Glass Industry: In the glass industry, annealing ovens are used to relieve internal stresses that occur during the manufacturing process. This makes the glass more durable and less likely to shatter.
- Metalworking: In metalworking, annealing ovens are used to soften metals, making them easier to machine, shape, or form. This is particularly important for metals that will undergo further processing or shaping.
- Electronics: Annealing ovens are also used in the electronics industry to treat semiconductor materials, improving their electrical properties and performance.
-
Benefits of Using an Annealing Oven:
- Improved Material Properties: The primary benefit of using an annealing oven is the improvement in material properties, such as increased ductility and reduced hardness. This makes the material more suitable for various applications.
- Stress Relief: Annealing ovens help eliminate internal stresses within the material, which can lead to cracking or failure under stress. This is particularly important in applications where material integrity is critical.
- Enhanced Workability: By softening the material, annealing ovens make it easier to machine, shape, or form, which can lead to more efficient manufacturing processes.
-
Considerations for Purchasing an Annealing Oven:
- Temperature Control: Precise temperature control is essential for the annealing process. When purchasing an annealing oven, it is important to consider the temperature range and control mechanisms to ensure they meet the specific requirements of your application.
- Cooling Rate: The ability to control the cooling rate is another critical factor. The oven should allow for slow, controlled cooling to achieve the desired material properties.
- Size and Capacity: The size and capacity of the oven should be appropriate for the volume of material you need to process. Consider both the physical size of the oven and its capacity in terms of the amount of material it can handle at once.
- Energy Efficiency: Energy efficiency is an important consideration, especially for large-scale operations. Look for ovens that offer good insulation and efficient heating elements to reduce energy consumption.
- Safety Features: Safety features such as temperature monitoring, automatic shut-off, and ventilation are important to ensure safe operation and prevent accidents.
In summary, an annealing oven is a vital piece of equipment in various industries, used to enhance the properties of materials through controlled heating and cooling. Understanding its purpose, applications, and key considerations for purchase can help ensure that you select the right oven for your specific needs.
Summary Table:
Key Aspect | Details |
---|---|
Purpose | Modifies material properties (e.g., reduced hardness, increased ductility) |
Function | Heats materials to precise temperatures, followed by controlled cooling |
Applications | Glass industry, metalworking, electronics |
Benefits | Stress relief, improved workability, enhanced material properties |
Purchase Considerations | Temperature control, cooling rate, size, energy efficiency, safety features |
Ready to enhance your material processing? Contact us today to find the perfect annealing oven for your needs!