Flux plays a critical role in brazing by removing oxides from the surfaces of the materials being joined, ensuring effective wetting of the braze alloy. It chemically cleans the metal surfaces, facilitates capillary action, and promotes the flow of filler metal. Flux is stable at room temperature but becomes highly reductive at high temperatures, dissolving oxides and preventing their reformation. It can be applied in various forms, such as pastes, liquids, or powders, and is essential for creating strong, clean brazed joints. In furnace brazing, the atmosphere often replaces the need for flux by removing oxides.
Key Points Explained:
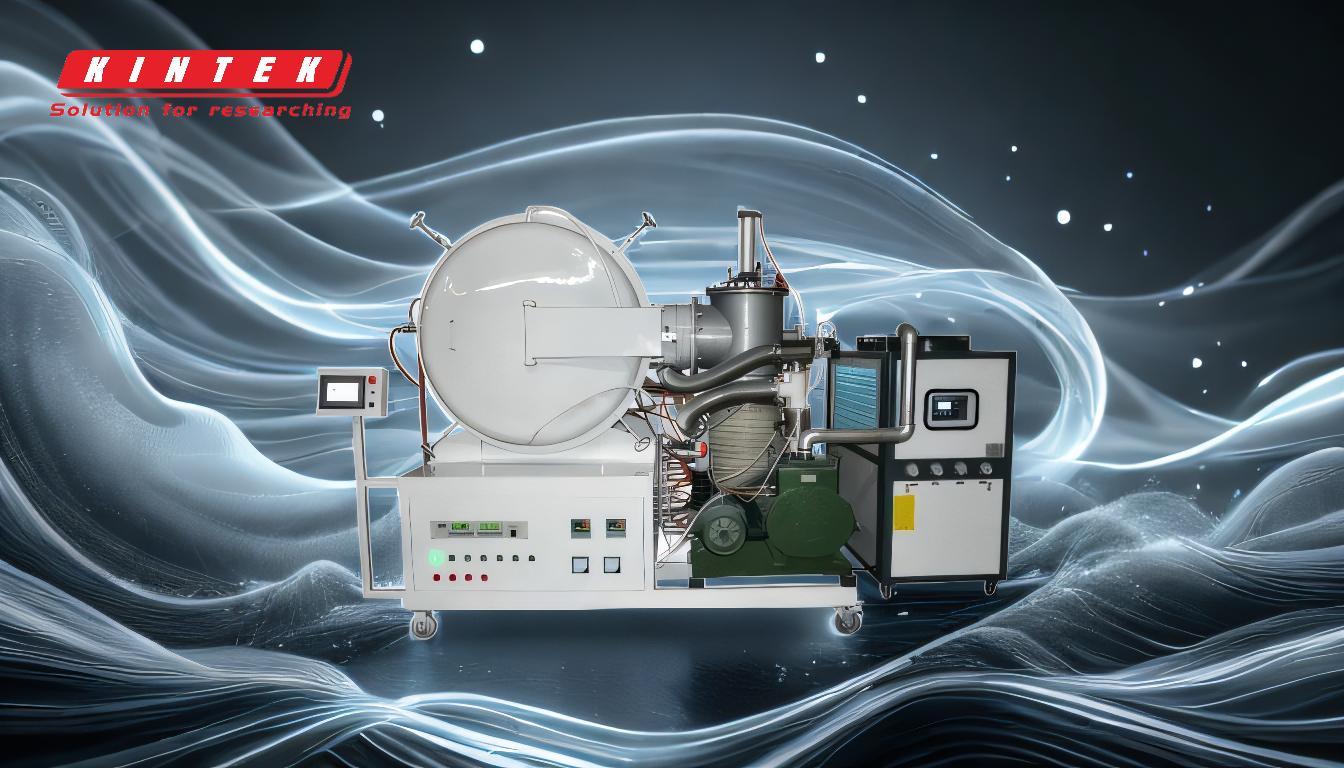
-
Oxide Removal:
- Flux dissolves and removes oxides from the metal surfaces being joined. Oxides can hinder the wetting process, preventing the braze alloy from adhering properly.
- By chemically cleaning the surface, flux ensures a clean, oxide-free interface for the filler metal to bond effectively.
-
Promoting Wetting:
- Wetting refers to the ability of the braze alloy to spread evenly over the base metal surfaces.
- Flux lowers the surface tension of the molten filler metal, allowing it to flow smoothly and form a strong bond with the base metal.
-
Cleaning the Surface:
- Flux removes contaminants, such as dirt, grease, and oxidation, from the metal surfaces.
- This cleaning action ensures that the filler metal can flow freely and create a uniform joint without defects.
-
Capillary Action:
- Flux enables capillary action, which is the movement of the molten filler metal into the narrow gaps between the surfaces being joined.
- This ensures that the filler metal fills all voids, creating a strong and continuous joint.
-
Preventing Oxide Formation:
- During the brazing process, high temperatures can cause new oxides to form on the metal surfaces.
- Flux acts as a protective barrier, preventing the formation of these oxides and maintaining a clean surface for bonding.
-
Forms of Flux:
- Flux is available in various forms, including pastes, liquids, powders, and pre-made brazing pastes.
- The choice of form depends on the specific application, material, and brazing method being used.
-
High-Temperature Reductive Properties:
- Flux is stable at room temperature but becomes highly reductive at the elevated temperatures used in brazing.
- This reductive property allows it to dissolve oxides and clean the metal surfaces effectively.
-
Role in Furnace Brazing:
- In furnace brazing, the controlled atmosphere (e.g., hydrogen or vacuum) can remove oxides, reducing or eliminating the need for flux.
- This method is particularly useful for materials that are sensitive to flux residues or for applications requiring high-purity joints.
-
Post-Brazing Residue:
- After cooling, flux often leaves a fine, adhesive layer on the joint.
- While this residue can provide some protection, it may need to be removed depending on the application requirements.
By addressing these key points, flux ensures the creation of strong, durable, and defect-free brazed joints, making it an indispensable component in the brazing process.
Summary Table:
Key Function | Description |
---|---|
Oxide Removal | Dissolves and removes oxides, ensuring a clean surface for bonding. |
Promoting Wetting | Lowers surface tension, allowing filler metal to spread evenly. |
Cleaning the Surface | Removes contaminants like dirt, grease, and oxidation for defect-free joints. |
Capillary Action | Enables molten filler metal to flow into narrow gaps, creating strong joints. |
Preventing Oxide Formation | Acts as a barrier to prevent new oxides from forming during brazing. |
Forms of Flux | Available as pastes, liquids, powders, or pre-made brazing pastes. |
High-Temperature Properties | Becomes highly reductive at high temperatures, dissolving oxides effectively. |
Role in Furnace Brazing | Controlled atmosphere can replace flux for high-purity or sensitive materials. |
Post-Brazing Residue | Leaves a fine layer that may need removal depending on application requirements. |
Learn more about how flux can enhance your brazing process—contact our experts today!