To provide an inert atmosphere for welding, gases such as argon, nitrogen, and helium are commonly used. These gases are chemically inert, meaning they do not react with the materials being welded, thereby preventing oxidation and other unwanted chemical reactions. Argon is particularly favored in welding due to its effectiveness in shielding the weld area from contaminants. Nitrogen is also widely used, especially in high-heat zones, where it can be injected through specialized ports to create a protective environment. The choice of gas depends on the specific welding process and materials involved, ensuring optimal results and high-quality welds.
Key Points Explained:
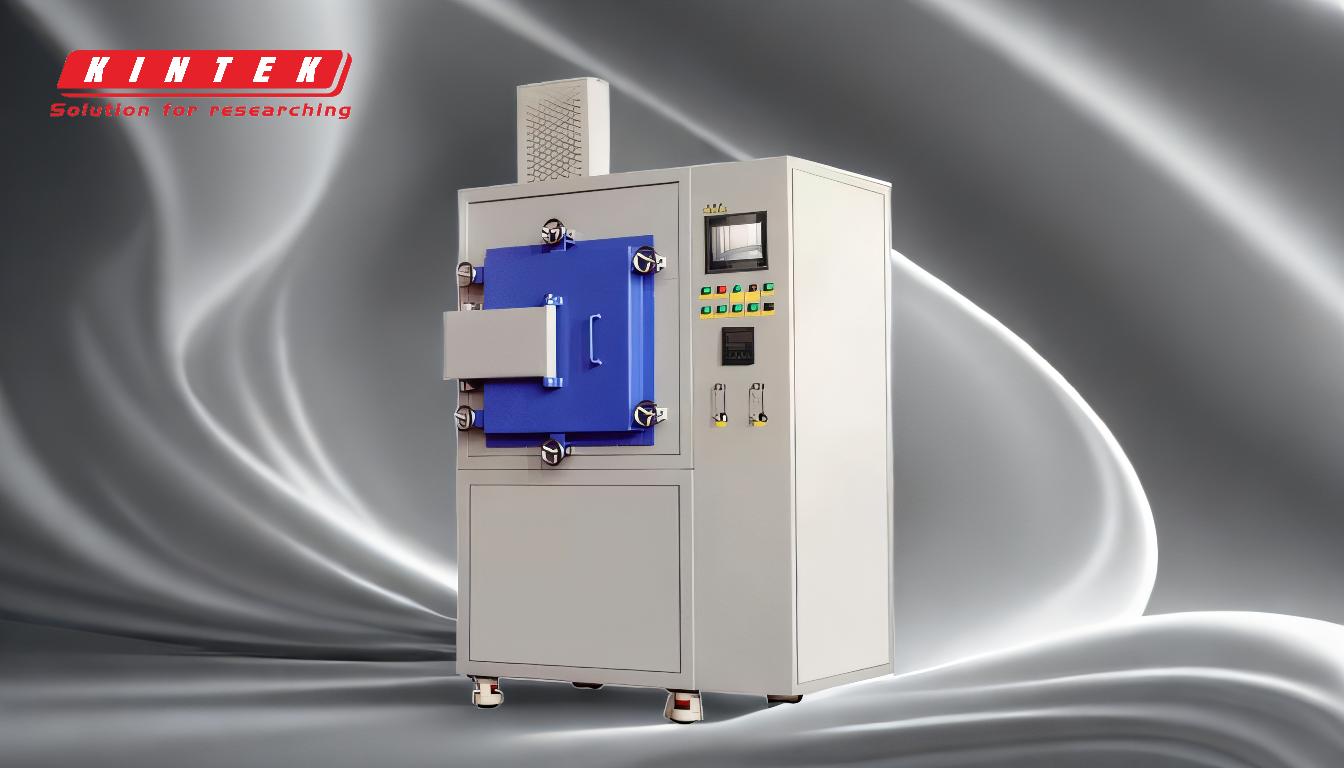
-
Argon as a Preferred Inert Gas:
- Argon is a noble gas, making it chemically inert and ideal for welding applications. It effectively shields the weld pool from atmospheric gases like oxygen and nitrogen, which can cause defects such as porosity and oxidation.
- It is commonly used in processes like TIG (Tungsten Inert Gas) welding and MIG (Metal Inert Gas) welding due to its ability to maintain a stable arc and produce clean welds.
-
Nitrogen for High-Heat Applications:
- Nitrogen is another widely used inert gas, particularly in high-temperature welding environments. It can be injected through angularly adjusted ports or as nitrogen "curtains" using advanced gas injection technology.
- This creates transverse laminar jet streams that remove oxygen from the environment, preventing oxidation and ensuring a clean weld.
-
Helium and Other Inert Gases:
- Helium is sometimes used in welding, especially for materials that require higher heat input. It has a higher thermal conductivity than argon, which can improve weld penetration and speed.
- Carbon dioxide is also mentioned as an option, though it is less common for creating inert atmospheres due to its reactivity compared to noble gases.
-
Industrial Applications and Gas Selection:
- In industrial settings, purified argon and nitrogen are often chosen for creating inert atmospheres in furnaces and welding processes. Their high natural abundance and chemically inactive properties make them cost-effective and reliable.
- The selection of gas depends on the specific requirements of the welding process, including the type of material, desired weld quality, and operational conditions.
-
Advantages of Inert Atmospheres in Welding:
- Prevents oxidation and contamination of the weld pool.
- Ensures consistent and high-quality welds by maintaining a stable environment.
- Reduces the risk of defects such as porosity, cracking, and inclusions.
By using these inert gases, welders can achieve precise and reliable results, making them essential for both industrial and specialized welding applications.
Summary Table:
Inert Gas | Key Properties | Common Applications |
---|---|---|
Argon | Chemically inert, shields weld pool | TIG welding, MIG welding |
Nitrogen | High-temperature stability | High-heat welding zones |
Helium | High thermal conductivity | Materials requiring higher heat input |
Carbon Dioxide | Less common, reactive | Limited use in inert atmospheres |
Achieve flawless welds with the right inert gas—contact our experts today for tailored solutions!