Refractory kilns are constructed using a variety of materials designed to withstand extreme temperatures and provide thermal insulation. The choice of materials depends on the specific application, process requirements, and desired performance characteristics. Common materials include firebricks, ceramic fibers, alumina-based materials, silicon carbide (SiC), and specialized castables. These materials are often arranged in multi-layer designs to optimize insulation, reduce heat loss, and ensure durability. For example, lightweight alumina ceramic fibers, high-quality insulation boards, and SiC heating rods are frequently used in modern kilns. The selection of refractory materials is tailored to the kiln's operating conditions, such as temperature ranges and chemical environments, to ensure efficiency and longevity.
Key Points Explained:
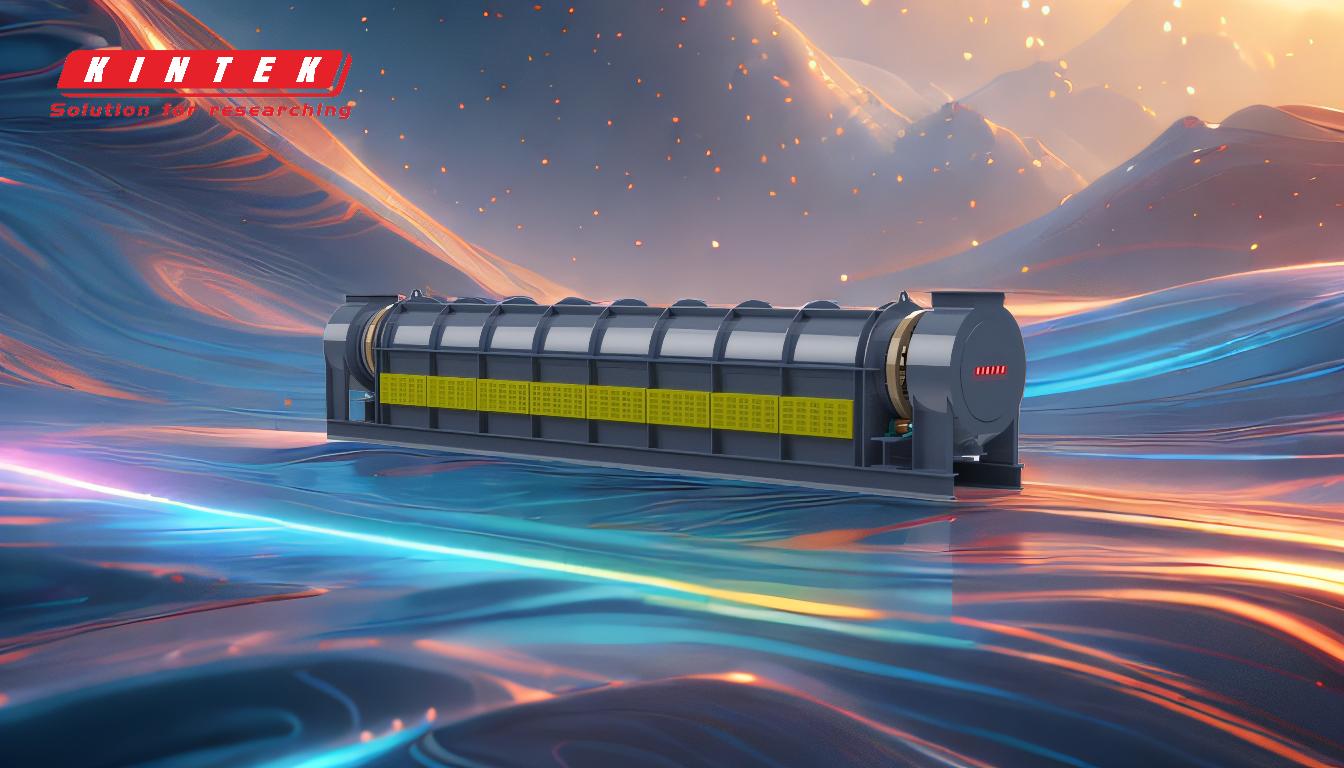
-
Firebricks and Ceramic Fibers
- Firebricks are one of the most common refractory materials used in kilns due to their ability to retain strength at high temperatures (above 1000°F). They are often made from materials like alumina or magnesite, depending on the kiln's application.
- Ceramic fibers, such as alumina-based fibers, are lightweight and provide excellent thermal insulation. They are often used in multi-layer designs to reduce heat loss and improve energy efficiency.
-
Alumina-Based Materials
- High-purity alumina fibers and alumina ceramic fibers are widely used in kiln linings due to their high service temperature, rapid heat and cold resistance, and excellent thermal insulation properties.
- Lightweight alumina plates or hollow aluminum oxide plates are also used to minimize heat storage capacity and improve thermal efficiency.
-
Silicon Carbide (SiC)
- SiC is a high-strength material used in heating elements (e.g., SiC heating rods) and refractory linings. It provides excellent thermal conductivity, resistance to thermal shock, and durability in high-temperature environments.
- SiC is often used in muffle furnaces and other specialized kilns where uniform heating and precise temperature control are required.
-
Multi-Layer Insulation Design
- Modern kilns often use a combination of materials in a multi-layer insulation design. For example, lightweight ceramic fibers are paired with high-quality insulation boards to create a robust and energy-efficient lining.
- This design ensures low heat loss, reduced energy consumption, and improved performance.
-
Specialized Refractory Castables
- Rotary kilns and other high-performance furnaces may use refractory castables, which are mixtures of refractory materials combined with binders. These castables are applied as linings to provide superior thermal insulation, reduce furnace skin temperature, and enhance durability.
-
Material Selection Based on Application
- The choice of refractory materials is highly dependent on the kiln's specific application and operating conditions. For example:
- Low-iron alumina or magnesium-spinel bricks are used in iron ore reduction kilns.
- Magnesite bricks are preferred in cement kilns due to their resistance to high temperatures and chemical corrosion.
- The thickness, physical properties, and chemical composition of the refractory materials are tailored to meet the demands of the process.
- The choice of refractory materials is highly dependent on the kiln's specific application and operating conditions. For example:
-
Non-Asbestos Components
- Modern refractory materials are designed to be asbestos-free, ensuring safety and compliance with environmental regulations. Materials like alumina ceramic fibers and insulation boards are used as alternatives.
-
Structural Components
- While refractory materials form the lining, the kiln's structural components (e.g., the outer shell) are typically made from carbon steel for direct-fired kilns or heat-resistant alloys for indirect-fired kilns. These materials provide structural integrity and support for the refractory lining.
By carefully selecting and combining these materials, refractory kilns achieve optimal performance, energy efficiency, and durability, tailored to the specific needs of the application.
Summary Table:
Material | Key Properties | Common Applications |
---|---|---|
Firebricks | High strength at >1000°F, made from alumina or magnesite | General kiln linings, high-temperature environments |
Ceramic Fibers | Lightweight, excellent thermal insulation, energy-efficient | Multi-layer insulation designs, reducing heat loss |
Alumina-Based | High service temperature, rapid heat/cold resistance, superior insulation | Kiln linings, lightweight plates for thermal efficiency |
Silicon Carbide (SiC) | High thermal conductivity, resistance to thermal shock, durable | Heating elements, muffle furnaces, specialized kilns |
Refractory Castables | Superior insulation, reduced furnace skin temperature, enhanced durability | Rotary kilns, high-performance furnaces |
Non-Asbestos | Asbestos-free, safe, compliant with environmental regulations | Modern kiln linings, insulation boards |
Structural Components | Carbon steel or heat-resistant alloys for structural integrity | Outer shell of direct/indirect-fired kilns |
Need help selecting the right refractory materials for your kiln? Contact our experts today for tailored solutions!