Hot forging is a manufacturing process that involves shaping metal using compressive forces at elevated temperatures. This method is widely used because it enhances the material's ductility, reduces the risk of cracking, and allows for the production of complex shapes. The materials suitable for hot forging are primarily metals and alloys that can withstand high temperatures and exhibit good plasticity under such conditions. Common materials include carbon steels, alloy steels, stainless steels, aluminum, copper, titanium, and nickel-based alloys. Each material has specific properties that make it suitable for hot forging, such as high strength, corrosion resistance, or lightweight characteristics. The choice of material depends on the intended application, desired mechanical properties, and cost considerations.
Key Points Explained:
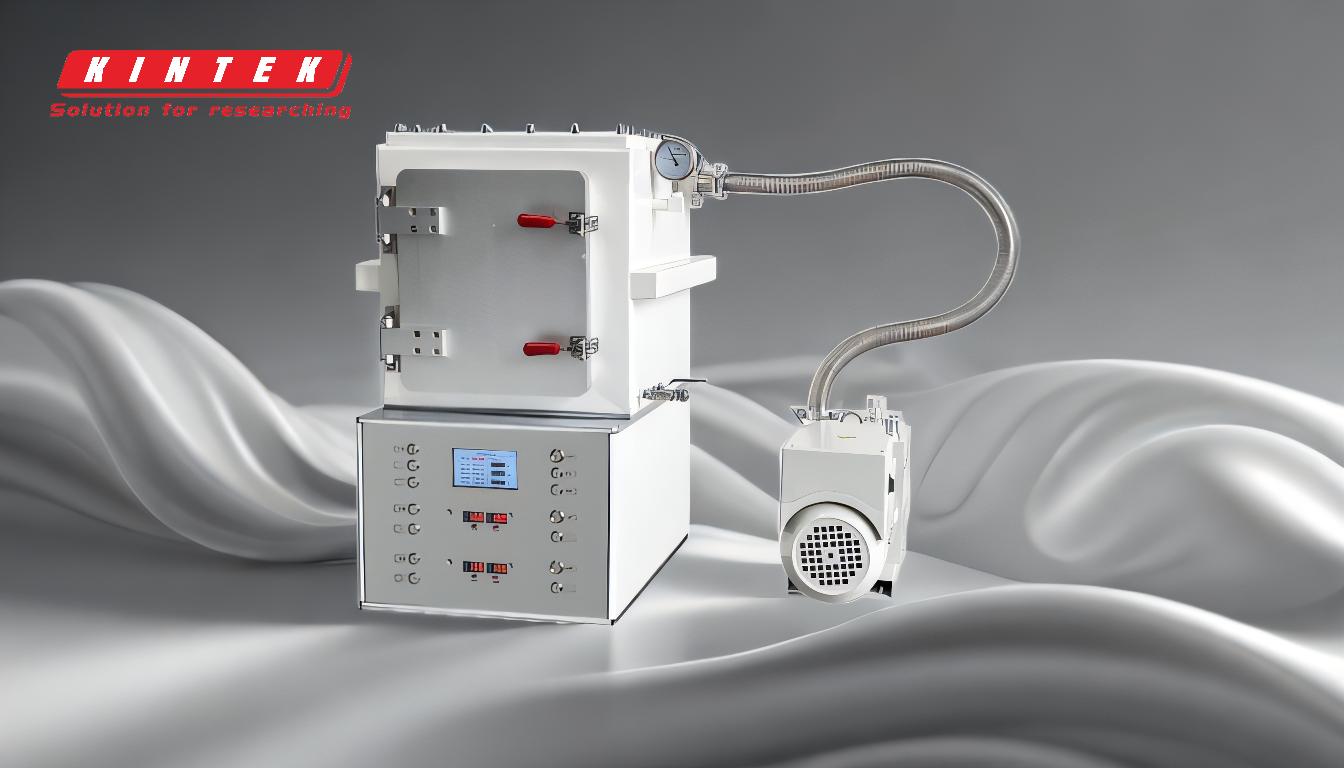
-
Carbon Steels:
- Carbon steels are one of the most commonly hot forged materials due to their excellent strength and durability. They contain varying amounts of carbon, which directly influences their hardness and tensile strength.
- Hot forging improves the grain structure of carbon steels, resulting in enhanced mechanical properties and better fatigue resistance.
- Applications include automotive components, tools, and machinery parts.
-
Alloy Steels:
- Alloy steels are carbon steels with additional alloying elements such as manganese, nickel, chromium, and molybdenum. These elements improve specific properties like hardness, toughness, and wear resistance.
- Hot forging of alloy steels allows for the production of high-strength components used in demanding environments, such as aerospace and heavy machinery.
-
Stainless Steels:
- Stainless steels are known for their corrosion resistance, making them ideal for applications in harsh environments, such as marine and chemical industries.
- Hot forging of stainless steels enhances their mechanical properties while maintaining their resistance to corrosion and oxidation.
- Common grades include 304, 316, and 17-4 PH, each suited for different applications based on their specific properties.
-
Aluminum Alloys:
- Aluminum and its alloys are lightweight and have excellent corrosion resistance, making them suitable for aerospace, automotive, and consumer electronics applications.
- Hot forging of aluminum alloys improves their strength and fatigue resistance, allowing for the production of lightweight yet durable components.
- Common alloys include 6061 and 7075, which are widely used in structural applications.
-
Copper and Copper Alloys:
- Copper and its alloys, such as brass and bronze, are highly malleable and have excellent electrical and thermal conductivity.
- Hot forging of copper alloys enhances their mechanical properties, making them suitable for electrical components, plumbing fittings, and decorative items.
- The process also improves their resistance to wear and corrosion.
-
Titanium Alloys:
- Titanium alloys are known for their high strength-to-weight ratio, corrosion resistance, and biocompatibility, making them ideal for aerospace, medical, and marine applications.
- Hot forging of titanium alloys improves their structural integrity and fatigue resistance, allowing for the production of high-performance components.
- Common alloys include Ti-6Al-4V, which is widely used in the aerospace industry.
-
Nickel-Based Alloys:
- Nickel-based alloys are highly resistant to heat, corrosion, and oxidation, making them suitable for extreme environments such as jet engines and chemical processing plants.
- Hot forging of nickel-based alloys enhances their mechanical properties, allowing for the production of components that can withstand high temperatures and corrosive environments.
- Common alloys include Inconel and Hastelloy, which are used in high-stress applications.
-
Material Selection Considerations:
- The choice of material for hot forging depends on several factors, including the intended application, required mechanical properties, and cost.
- Engineers must consider the material's ability to withstand high temperatures, its plasticity, and the desired final properties of the forged component.
- Cost considerations include the material's availability, ease of forging, and post-forging treatments required to achieve the desired properties.
In conclusion, hot forging is a versatile process suitable for a wide range of materials, each offering unique properties that make them ideal for specific applications. The selection of the appropriate material is crucial to achieving the desired performance and cost-effectiveness of the final product.
Summary Table:
Material | Key Properties | Common Applications |
---|---|---|
Carbon Steels | High strength, durability, improved grain structure | Automotive, tools, machinery parts |
Alloy Steels | Enhanced hardness, toughness, wear resistance | Aerospace, heavy machinery |
Stainless Steels | Corrosion resistance, mechanical strength | Marine, chemical industries |
Aluminum Alloys | Lightweight, corrosion resistance, improved strength | Aerospace, automotive, electronics |
Copper Alloys | Malleability, electrical/thermal conductivity, wear resistance | Electrical components, plumbing, decor |
Titanium Alloys | High strength-to-weight ratio, corrosion resistance, biocompatibility | Aerospace, medical, marine |
Nickel Alloys | Heat/corrosion resistance, oxidation resistance | Jet engines, chemical processing |
Need help selecting the right material for your hot forging project? Contact our experts today for tailored advice!