Tempering is a heat treatment process primarily applied to ferrous alloys, such as steel, to improve their mechanical properties. It involves heating the metal to a specific temperature below its critical point and then cooling it at a controlled rate. This process reduces brittleness, increases toughness, and relieves internal stresses. While tempering is most commonly associated with steel, it can also be applied to certain non-ferrous metals and alloys, though the process and outcomes may differ. The effectiveness of tempering depends on the metal's composition, structure, and intended application.
Key Points Explained:
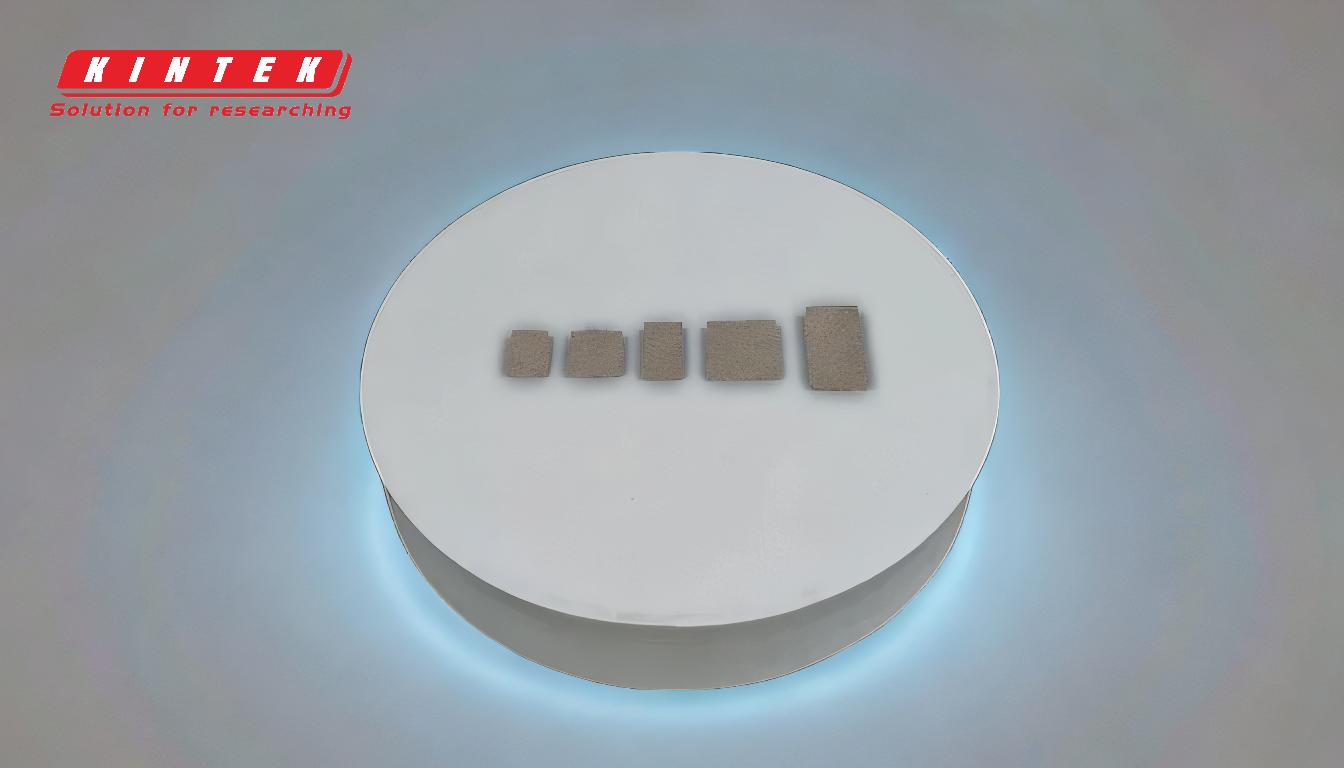
-
What is Tempering?
- Tempering is a heat treatment process used to improve the mechanical properties of metals, particularly steel.
- It involves heating the metal to a temperature below its critical point and then cooling it at a controlled rate.
- The primary goals are to reduce brittleness, increase toughness, and relieve internal stresses.
-
Metals Commonly Tempered
- Steel: The most common metal subjected to tempering. Different grades of steel (e.g., carbon steel, alloy steel, tool steel) respond well to tempering, enhancing their hardness, strength, and ductility.
- Cast Iron: Certain types of cast iron, such as malleable cast iron, can be tempered to improve their mechanical properties.
- Non-Ferrous Metals: While less common, some non-ferrous metals like titanium and certain aluminum alloys can undergo tempering-like processes to achieve desired properties.
-
Factors Influencing Tempering
- Composition: The alloying elements in the metal (e.g., carbon content in steel) significantly affect the tempering process.
- Temperature: The tempering temperature determines the final properties of the metal. Higher temperatures generally result in softer, more ductile materials.
- Cooling Rate: Controlled cooling is essential to achieve the desired balance of hardness and toughness.
-
Applications of Tempered Metals
- Steel: Used in construction, automotive, and tool manufacturing due to its enhanced strength and durability.
- Cast Iron: Applied in machinery and automotive components where toughness and wear resistance are required.
- Non-Ferrous Metals: Used in aerospace, medical devices, and high-performance applications where lightweight and corrosion resistance are critical.
-
Limitations of Tempering
- Not all metals can be tempered effectively. For example, pure iron and some non-ferrous metals do not respond well to tempering.
- The process requires precise control of temperature and cooling rates, making it more complex for certain alloys.
-
Alternative Processes for Non-Temperable Metals
- For metals that cannot be tempered, other heat treatment processes like annealing, quenching, or precipitation hardening may be used to achieve similar improvements in mechanical properties.
By understanding these key points, a purchaser can make informed decisions about which metals and alloys are suitable for tempering based on their specific application requirements.
Summary Table:
Key Aspect | Details |
---|---|
Primary Goal | Reduce brittleness, increase toughness, relieve internal stresses. |
Common Metals Tempered | Steel, cast iron, titanium, and certain aluminum alloys. |
Influencing Factors | Composition, tempering temperature, cooling rate. |
Applications | Construction, automotive, aerospace, medical devices, and tool manufacturing. |
Limitations | Not all metals can be tempered; requires precise temperature control. |
Alternatives | Annealing, quenching, or precipitation hardening for non-temperable metals. |
Discover how tempering can optimize your metal components—contact our experts today for tailored solutions!