Hydrogen brazing is a specialized process that involves the use of hydrogen as a deoxidizing agent to reduce surface oxides and create strong, clean, and oxidation-free braze joints. The process is typically conducted in a controlled hydrogen atmosphere, often within a hydrogen furnace, to ensure precision and high-quality results. The temperature for hydrogen brazing varies depending on the materials being joined, but it generally falls within the range of 700°C to 1100°C (1292°F to 2012°F). This temperature range is sufficient to melt the filler metal while allowing hydrogen to effectively reduce oxides on the metal surfaces. Special materials like vacuum-grade OFE Copper 101 are often used to prevent issues such as water vapor formation, which can lead to defects like bulging or blistering. Hydrogen brazing is particularly effective for reducing oxides of iron, copper, nickel, and cobalt, but less so for oxides of aluminum, beryllium, titanium, and silicon, which may require alternative methods like vacuum brazing or the use of inert gases.
Key Points Explained:
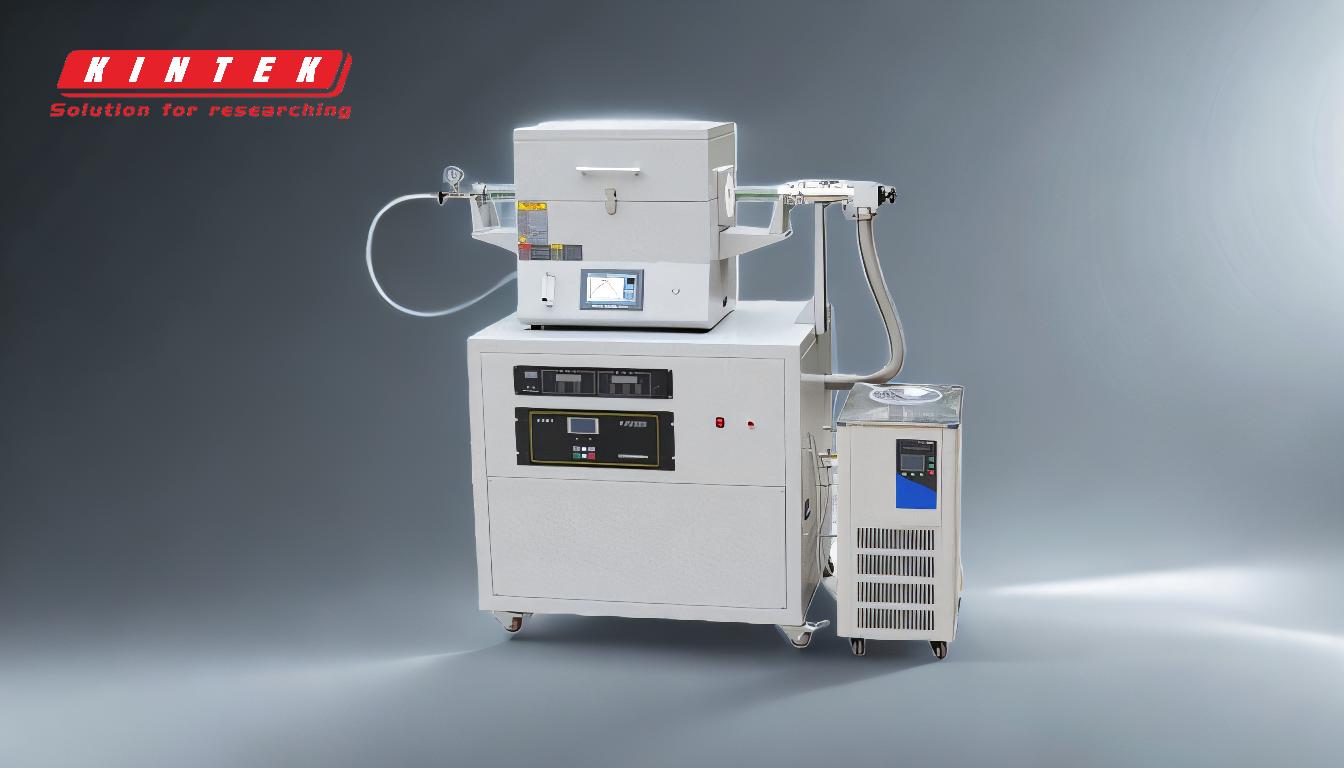
-
Hydrogen as a Deoxidizer:
- Hydrogen plays a crucial role in the brazing process by acting as a deoxidizer. It reduces surface oxides on metals such as iron, copper, nickel, and cobalt, which helps in creating strong and clean braze joints.
- However, hydrogen is less effective with oxides of aluminum, beryllium, titanium, and silicon. For these materials, alternative methods like vacuum brazing or the use of inert gases such as helium or argon are often required.
-
Temperature Range for Hydrogen Brazing:
- The temperature for hydrogen brazing typically ranges between 700°C to 1100°C (1292°F to 2012°F). This range is chosen to ensure that the filler metal melts properly while allowing hydrogen to effectively reduce the oxides on the metal surfaces.
- The exact temperature within this range depends on the specific materials being joined and the type of filler metal used.
-
Importance of Controlled Atmosphere:
- Hydrogen brazing is performed in a controlled hydrogen atmosphere, often within a hydrogen furnace. This controlled environment is essential to prevent oxidation and contamination during the brazing process.
- The result is a clean and bright surface on the brazed assemblies, which are ready for further assembly without the need for additional processing.
-
Material Considerations:
- Special materials like vacuum-grade OFE Copper 101 are often used in hydrogen brazing to prevent the formation of water vapor. Water vapor can cause defects such as bulging or blistering during the brazing process.
- The choice of materials is critical to ensure the success of the brazing process and to achieve high-quality, defect-free joints.
-
Applications and Advantages:
- Hydrogen brazing is widely used in industries where high-strength, clean, and oxidation-free joints are required. This includes applications in aerospace, electronics, and precision engineering.
- The process offers several advantages, including the elimination of the need for additional cleaning or processing after brazing, resulting in cost and time savings.
By understanding these key points, one can appreciate the complexity and precision involved in hydrogen brazing, as well as the importance of controlling the temperature and atmosphere to achieve optimal results.
Summary Table:
Aspect | Details |
---|---|
Temperature Range | 700°C to 1100°C (1292°F to 2012°F) |
Key Materials | Iron, Copper, Nickel, Cobalt (effective); Aluminum, Titanium (less effective) |
Controlled Atmosphere | Hydrogen furnace to prevent oxidation and contamination |
Special Materials | Vacuum-grade OFE Copper 101 to avoid water vapor defects |
Applications | Aerospace, electronics, precision engineering |
Need expert advice on hydrogen brazing? Contact us today for tailored solutions!