When considering the longevity of furnaces, the type of furnace plays a significant role in determining how long it will last. Generally, boilers and electric furnaces have the longest lifespan, averaging 20 to 30 years, while most other furnaces last between 15 to 20 years. However, the actual lifespan of a furnace can vary based on factors such as maintenance, usage, and the quality of installation. This answer explores the types of furnaces that last the longest, the factors influencing their lifespan, and how to maximize their durability.
Key Points Explained:
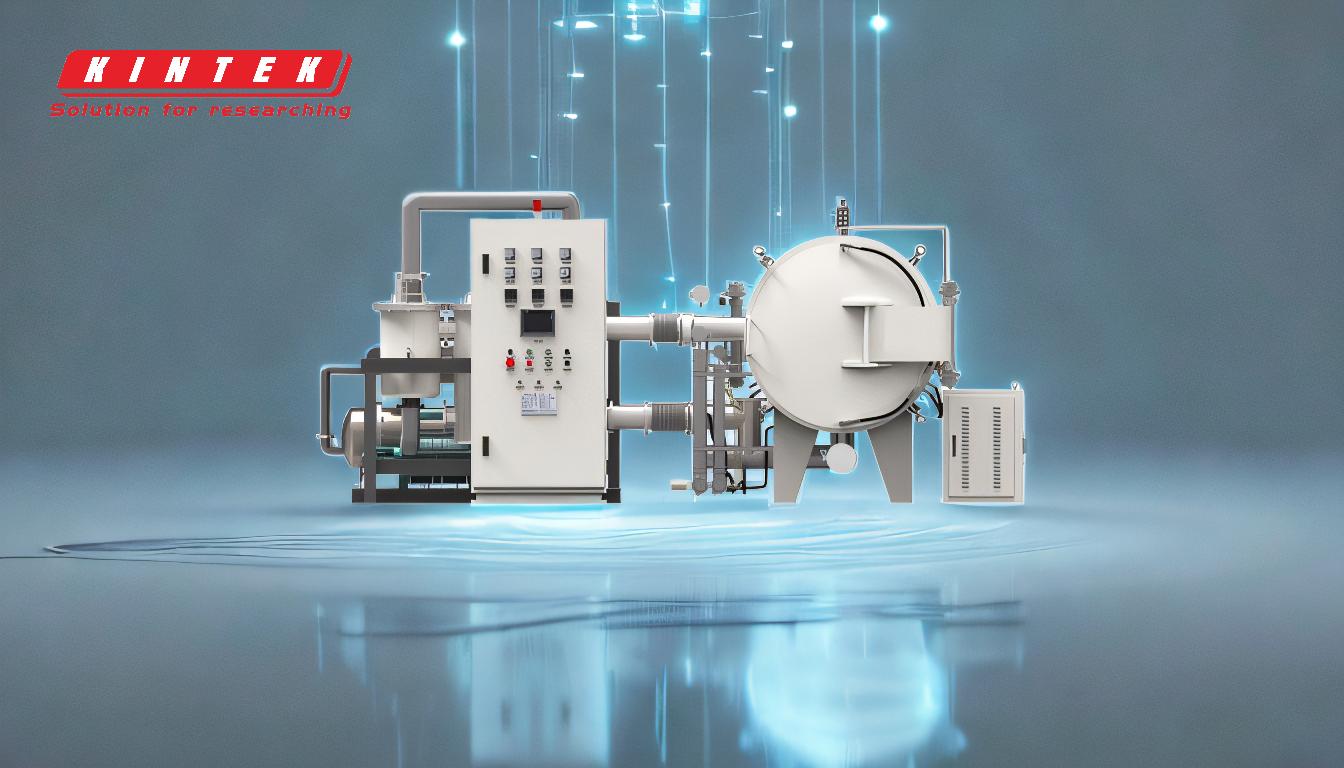
-
Types of Furnaces with the Longest Lifespan
- Boilers: Boilers are known for their durability and can last between 20 to 30 years. They operate by heating water and distributing it through radiators or underfloor heating systems. Because they have fewer moving parts compared to forced-air furnaces, they are less prone to mechanical failure.
- Electric Furnaces: Electric furnaces also have a lifespan of 20 to 30 years. They are simpler in design, with no combustion process, which reduces wear and tear. However, their operational costs can be higher due to electricity prices.
- Gas Furnaces: Gas furnaces typically last 15 to 20 years. While they are efficient and cost-effective to operate, their lifespan is shorter due to the complexity of their combustion systems and the stress placed on components like heat exchangers.
- Oil Furnaces: Oil furnaces have a similar lifespan to gas furnaces, averaging 15 to 20 years. They require regular maintenance to prevent soot buildup and ensure efficient operation.
-
Factors Influencing Furnace Lifespan
- Maintenance: Regular maintenance is crucial for extending the lifespan of any furnace. This includes cleaning or replacing filters, inspecting burners, and ensuring proper airflow. Neglecting maintenance can lead to premature wear and failure.
- Usage Patterns: Furnaces that are used heavily, especially in extreme climates, may wear out faster. Conversely, furnaces in milder climates or those used sparingly tend to last longer.
- Installation Quality: Proper installation by a qualified professional ensures that the furnace operates efficiently and reduces the risk of early breakdowns. Poor installation can lead to issues like improper airflow or gas leaks, which can shorten the furnace's lifespan.
- Fuel Type: The type of fuel used can also impact longevity. Electric furnaces, for example, have fewer mechanical components and no combustion process, which contributes to their longer lifespan compared to gas or oil furnaces.
-
How to Maximize the Lifespan of a Furnace
- Schedule Regular Maintenance: Annual inspections and tune-ups by a licensed HVAC technician can identify and address potential issues before they become major problems.
- Replace Filters Regularly: Dirty filters restrict airflow, forcing the furnace to work harder and increasing wear on components. Replace filters every 1 to 3 months, depending on usage.
- Invest in a High-Quality Furnace: While upfront costs may be higher, high-quality furnaces are often built with durable materials and advanced technology, leading to a longer lifespan.
- Optimize Thermostat Settings: Using a programmable or smart thermostat can reduce the workload on the furnace by adjusting temperatures based on your schedule.
- Ensure Proper Sizing: A furnace that is too large or too small for your home will operate inefficiently, leading to increased wear and tear. A professional can help determine the right size for your needs.
-
Considerations When Choosing a Furnace
- Energy Efficiency: High-efficiency furnaces may cost more upfront but can save money in the long run through lower energy bills. Look for furnaces with a high Annual Fuel Utilization Efficiency (AFUE) rating.
- Cost of Operation: Electric furnaces may have a longer lifespan, but their operational costs can be higher due to electricity prices. Gas furnaces, while shorter-lived, are often more cost-effective to operate.
- Climate and Usage Needs: Consider your local climate and how often you will use the furnace. In colder climates, a durable and efficient furnace is essential for comfort and cost savings.
- Warranty and Support: Choose a furnace with a strong warranty and reliable customer support. This can provide peace of mind and reduce long-term costs.
By understanding the types of furnaces that last the longest and the factors that influence their lifespan, you can make an informed decision when purchasing and maintaining a furnace. Regular maintenance, proper installation, and thoughtful usage can help ensure that your furnace provides reliable heating for many years.
Summary Table:
Furnace Type | Lifespan | Key Features |
---|---|---|
Boilers | 20-30 years | Fewer moving parts, durable, less prone to failure |
Electric Furnaces | 20-30 years | Simple design, no combustion, higher operational costs |
Gas Furnaces | 15-20 years | Efficient, cost-effective, shorter lifespan due to combustion complexity |
Oil Furnaces | 15-20 years | Requires regular maintenance, prone to soot buildup |
Ensure your furnace lasts for decades—contact our experts today for maintenance and installation advice!