Graphite is widely used in furnaces due to its unique properties that make it ideal for high-temperature applications. It is chemically inert, meaning it does not react with process gases like nitrogen and argon, which are commonly used in vacuum furnaces. Additionally, graphite is neutral to non-ferrous metals, preventing unwanted reactions during melting processes. Its ability to withstand extreme temperatures without degrading makes it a preferred material for furnace components such as crucibles and heating elements. This combination of thermal stability, chemical resistance, and mechanical strength enhances furnace productivity and ensures consistent performance in high-temperature environments.
Key Points Explained:
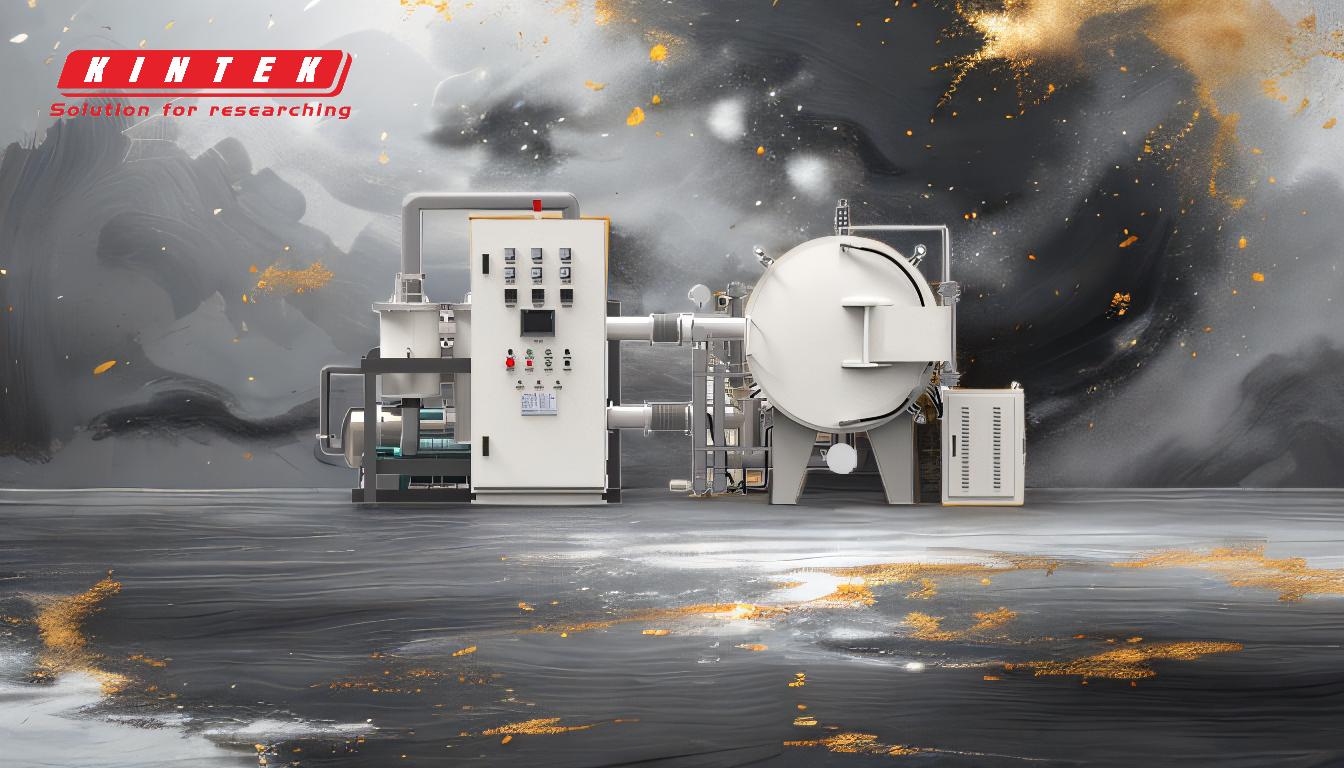
-
Chemical Inertness:
- Graphite does not react with process gases such as nitrogen and argon, making it suitable for use in vacuum furnaces. This inertness ensures that the furnace environment remains stable and uncontaminated, which is critical for processes like heat treatment and material synthesis. For more details, see graphite furnace.
-
High-Temperature Resistance:
- Graphite can withstand extremely high temperatures without melting or degrading. This property is essential for furnace applications where temperatures often exceed 1000°C. Its thermal stability ensures consistent performance and longevity of furnace components.
-
Neutrality to Non-Ferrous Metals:
- Unlike ferrous metals, graphite does not react with non-ferrous metals. This makes it ideal for use in crucibles, as it prevents carbon absorption and unwanted chemical reactions during metal melting processes. This neutrality ensures the purity of the molten metal.
-
Mechanical Strength and Durability:
- Graphite maintains its structural integrity even under high thermal stress. This durability reduces the need for frequent replacements, lowering maintenance costs and increasing furnace productivity.
-
Versatility in Applications:
- Graphite is used in various furnace components, including heating elements, crucibles, and insulation. Its versatility makes it a cornerstone material in industries such as metallurgy, aerospace, and semiconductor manufacturing.
-
Cost-Effectiveness:
- Despite its advanced properties, graphite is relatively cost-effective compared to other high-temperature materials. Its long lifespan and low maintenance requirements contribute to overall cost savings in furnace operations.
By leveraging these properties, graphite enhances the efficiency, reliability, and performance of furnaces, making it an indispensable material in high-temperature industrial processes.
Summary Table:
Property | Benefits |
---|---|
Chemical Inertness | Does not react with process gases, ensuring a stable furnace environment. |
High-Temperature Resistance | Withstands extreme temperatures (>1000°C) without degrading. |
Neutrality to Non-Ferrous Metals | Prevents unwanted reactions, ensuring molten metal purity. |
Mechanical Strength | Maintains structural integrity under thermal stress, reducing maintenance. |
Versatility | Used in heating elements, crucibles, and insulation across industries. |
Cost-Effectiveness | Long lifespan and low maintenance reduce operational costs. |
Discover how graphite can enhance your furnace performance—contact our experts today!