Introduction
Table of Contents
- Warm Isostatic Pressing: An Overview
Welcome to our blog post on Warm Isostatic Pressing (WIP), an advanced manufacturing technology that is revolutionizing the industry. In this article, we will explore the definition and functionality of WIP, along with its applications in pressing powdered products. We will also delve into the features of the WIP process and the significance of temperature control. So, whether you're a business professional or a manufacturing enthusiast, get ready to discover the wonders of Warm Isostatic Pressing and its impact on the manufacturing industry. Let's dive in!
Warm Isostatic Pressing: An Overview
Definition and functionality of Warm Isostatic Pressing (WIP)
Warm Isostatic Pressing (WIP) is a cutting-edge technology that enables isostatic pressing at a temperature that does not exceed the boiling point of the liquid medium. It is a variant of cold isostatic pressing (CIP) that includes a heating element.
The WIP process involves utilizing flexible materials as a jacket mold and hydraulic pressure as a pressure medium to shape and press powdered products. It applies uniform pressure to the powder material from all directions, resulting in the production of complex parts and components with precision and efficiency.
Application of WIP in pressing powdered products
Warm isostatic pressing is commonly used for powders, binders, and other materials that have special temperature requirements or cannot be molded at room temperature. This technology has revolutionized the manufacturing industry by enabling the production of complex parts and components.
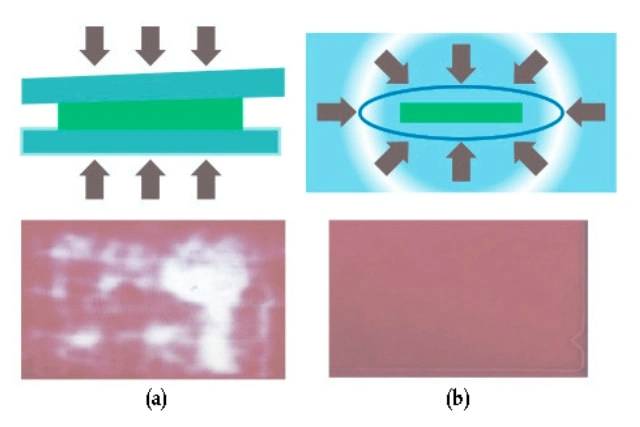
Features of the WIP process and the significance of temperature control
The WIP process involves heating the liquid medium first and then continuously injecting the heated liquid medium into a sealed pressing cylinder through a booster source. This ensures the accuracy of temperature control during the pressing process.
The significance of temperature control in WIP is crucial as it allows for precise shaping and pressing of the powder material. The controlled temperature ensures that the material reaches its desired plasticity and can be molded effectively.
Overall, Warm Isostatic Pressing (WIP) offers a unique and efficient method for shaping and pressing powdered products. Its application in various industries has led to the development of complex components and improved manufacturing processes. With proper temperature control, WIP provides a reliable and precise solution for producing high-quality parts.
Applications of Warm Isostatic Pressing
Use of WIP in manufacturing industry
Warm Isostatic Pressing (WIP) is a cutting-edge technology that has revolutionized the manufacturing industry. It enables isostatic pressing at a temperature that does not exceed the boiling point of the liquid medium. WIP is commonly used for powders, binders, and other materials that have special temperature requirements or cannot be molded at room temperature.
One of the main applications of WIP in the manufacturing industry is the production of complex parts and components with precision and efficiency. WIP employs warm water or a similar medium to apply uniform pressure to powdered products from all directions. This ensures that the final product has a high level of density and uniformity.
WIP can be used for a wide range of materials, including plastics and laminated products. It can be customized to meet specific requirements and can operate at different pressures and temperatures. The equipment used for WIP can be gas or liquid pressurized, and both cold and hot wall versions are available.
Production of complex parts and components with WIP
Warm isostatic pressing has enabled the production of complex parts and components that would be difficult or impossible to manufacture using traditional methods. By applying uniform pressure from all directions, WIP ensures that the final product has consistent density and eliminates any defects or voids.
The process of warm isostatic pressing involves heating the liquid medium, such as water or oil thermal fluid, and continuously injecting it into a sealed pressing cylinder. The pressing cylinder is equipped with a heating element to ensure accurate temperature control. The flexibility of the materials used as a jacket mold allows for the shaping and pressing of various powder materials.
One of the advantages of using WIP for the production of complex parts is the ability to achieve high levels of precision and efficiency. WIP can produce parts with intricate geometries and tight tolerances, making it suitable for applications in industries such as aerospace, automotive, and medical.
In addition to its use in manufacturing, warm isostatic pressing has also found applications in the field of Additive Manufacturing (AM). Hot Isostatic Pressing (HIP) is used to consolidate metal powders and metal matrix composites, eliminate porosity in sintered parts, produce metal-clad parts through diffusion bonding, and eliminate defects in castings. HIP plays a crucial role in improving the quality and performance of critical components produced through powder-based Additive Manufacturing.
Overall, warm isostatic pressing is a versatile and efficient technology that has transformed the manufacturing industry. Its applications range from the production of complex parts and components to improving the quality of Additive Manufacturing processes. With its ability to achieve high levels of precision and efficiency, WIP is becoming increasingly indispensable in various industries.
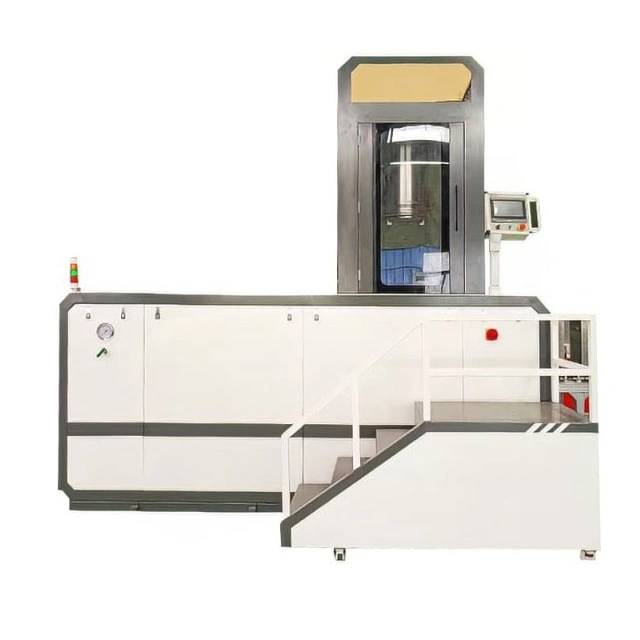
Structures Suitable for Warm Isostatic Pressing Equipment
Bolt Structure: Ideal for Small and Medium-Sized Isostatic Pressing Equipment
The bolt structure is well-suited for small and medium-sized isostatic pressing equipment. It offers several advantages, including high temperature control accuracy, good uniformity in the hot zone, and a compact structure. One of the key benefits of the bolt structure is that it generates no noise and doesn't cause oil or water pollution on the site.
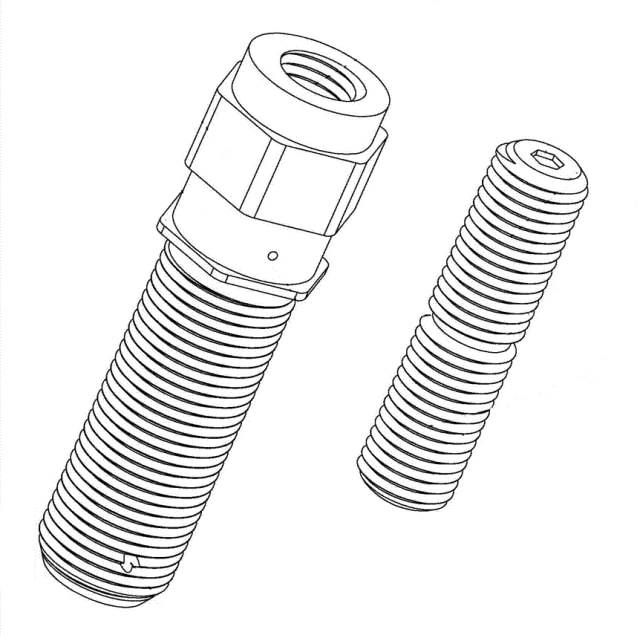
Moment Tooth Structure: Ideal for Medium and Large Isostatic Pressing Equipment
The moment tooth structure is specifically designed for medium and large isostatic pressing equipment. It shares similar characteristics with the bolt structure, including high temperature control accuracy, good uniformity in the hot zone, and a compact structure. Like the bolt structure, the moment tooth structure is also noise-free and doesn't cause oil or water pollution on the site.
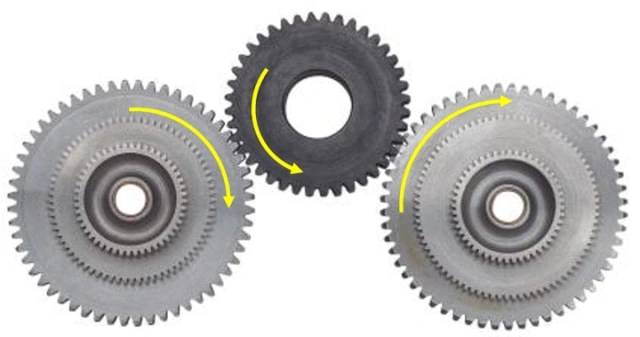
Steel Wire Winding Structure: Ideal for Large-Scale Warm Isostatic Pressing Equipment
The steel wire winding structure is ideal for large-scale warm isostatic pressing equipment. This structure is typically utilized in equipment with a cylinder diameter greater than 400mm and a working pressure exceeding 250MPa. It offers high temperature control accuracy, good uniformity in the hot zone, and a compact structure. Additionally, the steel wire winding structure generates low noise and doesn't cause oil or water pollution on the site.
In summary, the selection of the appropriate structure for warm isostatic pressing equipment depends on the size and requirements of the equipment. The bolt structure is suitable for small and medium-sized equipment, while the moment tooth structure is ideal for medium and large equipment. The steel wire winding structure is specifically designed for large-scale equipment. Each structure offers excellent temperature control accuracy, uniformity in the hot zone, and a compact design, ensuring efficient and reliable warm isostatic pressing processes.
Conclusion
Warm Isostatic Pressing (WIP) is a highly advanced manufacturing technology that offers numerous benefits in the production of powdered products. With its precise temperature control and uniform pressure distribution, WIP allows for the creation of complex parts and components with exceptional strength and density. The applications of WIP in the manufacturing industry are vast, ranging from aerospace and automotive to medical and energy sectors. The different structures suitable for warm isostatic pressing equipment provide flexibility and scalability for various production requirements. Overall, WIP proves to be a game-changer in the manufacturing world, offering enhanced quality and performance for a wide range of products.
CONTACT US FOR A FREE CONSULTATION
KINTEK LAB SOLUTION's products and services have been recognized by customers around the world. Our staff will be happy to assist with any inquiry you might have. Contact us for a free consultation and talk to a product specialist to find the most suitable solution for your application needs!