Annealing is a heat treatment process that involves heating a material above its recrystallization temperature, holding it at that temperature for a specific period, and then cooling it to alter its physical and chemical properties. The cooling process is a critical part of annealing, as it determines the final microstructure and properties of the material. While furnace cooling is a common method, especially for achieving slow and controlled cooling, it is not always mandatory. The cooling method depends on the material, desired properties, and specific annealing type. For instance, some annealing processes may allow for air cooling or other controlled cooling methods. The key is to ensure that the cooling rate is appropriate to achieve the desired microstructure and stress relief.
Key Points Explained:
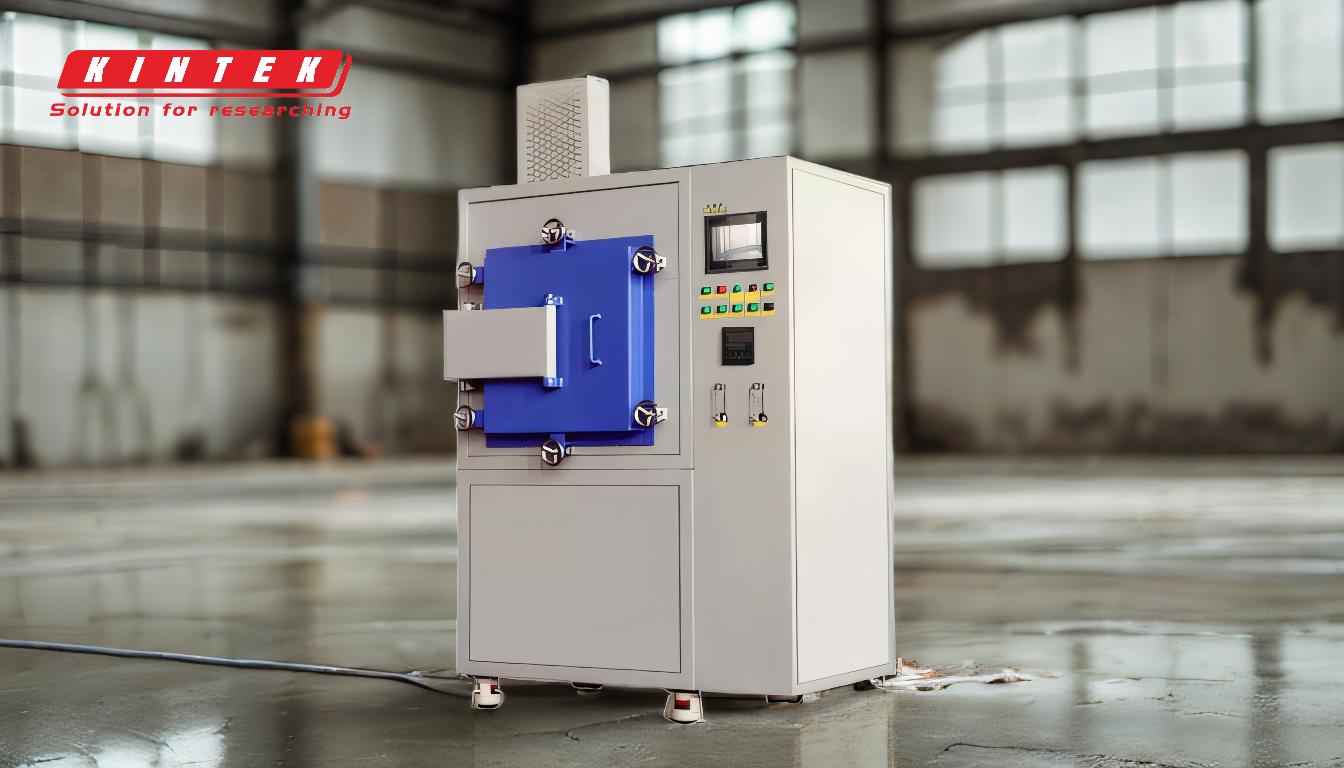
-
Purpose of Annealing:
- Annealing is used to alter a material's physical and chemical properties, such as reducing internal stresses, improving ductility, and refining grain microstructure.
- It is suitable for both ferrous and non-ferrous alloys and is often used to prepare materials for further machining or to enhance their workability.
-
Heating Phase:
- The material is heated above its recrystallization temperature, where the crystalline structure becomes fluid but remains in a solid form.
- This allows defects in the material to repair themselves, leading to a more uniform and homogeneous internal structure.
-
Cooling Phase:
- The cooling process is critical in determining the final properties of the material.
- Slow and controlled cooling, such as furnace cooling, is often used to achieve a soft, ductile microstructure.
- Rapid cooling may be used in some cases, but it can lead to increased hardness and reduced ductility.
-
Types of Cooling in Annealing:
- Furnace Cooling: This is the most common method, especially for full annealing. The material is cooled slowly inside the furnace, allowing for a uniform and controlled cooling rate.
- Air Cooling: In some cases, materials can be removed from the furnace and allowed to cool in air. This method is faster than furnace cooling but still provides controlled cooling.
- Forced Cooling: In processes like bright annealing, cold air or other cooling mediums may be forced through the furnace to cool the material more quickly while maintaining surface quality.
-
Importance of Controlled Cooling:
- Controlled cooling ensures that the material achieves the desired microstructure, such as a refined grain structure or reduced internal stresses.
- It also prevents the formation of undesirable phases or structures that could compromise the material's properties.
-
Special Considerations for Bright Annealing:
- In bright annealing, the cooling process is carefully managed to prevent oxidation or contamination of the material's surface.
- Non-return valves are used to prevent oxygen or other gases from entering the furnace, ensuring the material remains bright and free from oxide scale.
-
Types of Annealing and Cooling Methods:
- Full Annealing: Typically involves furnace cooling to achieve a soft, ductile structure.
- Process Annealing: May use slower cooling rates to relieve stresses without significantly altering the microstructure.
- Spheroidizing: Often involves prolonged heating and slow cooling to produce a spheroidal microstructure, which improves machinability.
-
Material-Specific Considerations:
- The cooling method may vary depending on the material. For example, steel often requires slow cooling to achieve the desired properties, while some non-ferrous alloys may tolerate faster cooling rates.
In summary, while furnace cooling is a common and effective method for annealing, it is not always required. The choice of cooling method depends on the material, the type of annealing being performed, and the desired final properties. Controlled cooling, whether through furnace cooling, air cooling, or other methods, is essential to achieve the desired microstructure and stress relief in the material.
Summary Table:
Aspect | Details |
---|---|
Purpose of Annealing | Reduces internal stresses, improves ductility, and refines grain structure. |
Heating Phase | Material heated above recrystallization temperature for defect repair. |
Cooling Phase | Determines final microstructure; slow cooling for soft, ductile properties. |
Cooling Methods | Furnace cooling (common), air cooling, or forced cooling for specific needs. |
Controlled Cooling | Ensures desired microstructure and prevents undesirable phases. |
Bright Annealing | Prevents oxidation; uses non-return valves for surface quality. |
Material Considerations | Cooling method varies by material (e.g., steel vs. non-ferrous alloys). |
Need help selecting the right annealing process for your materials? Contact our experts today!