The relationship between temperature and hardness is a critical aspect of material science, particularly in understanding how materials behave under varying thermal conditions. As temperature increases, the hardness of a material generally decreases due to the increased atomic vibrations and reduced interatomic forces. However, at a certain point, a significant change in hardness occurs, known as the hot or red hardness, which is especially important in materials like heat-treated alloys. This phenomenon is crucial for applications where materials are subjected to high temperatures, such as in industrial machinery or aerospace components.
Key Points Explained:
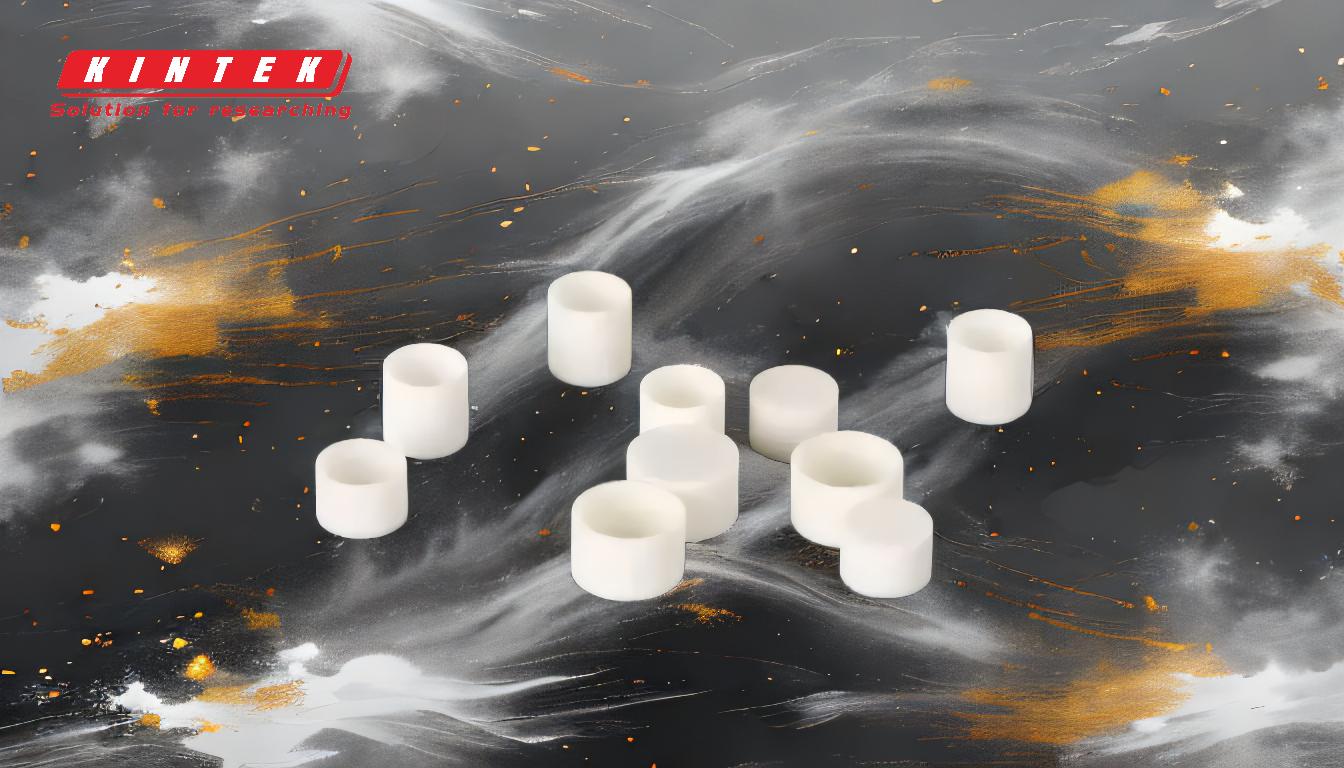
-
Temperature and Hardness Relationship:
- General Trend: As temperature increases, the hardness of a material typically decreases. This is because higher temperatures cause atoms to vibrate more vigorously, reducing the material's resistance to deformation.
- Atomic Level Explanation: At elevated temperatures, the increased kinetic energy of atoms weakens the bonds between them, making it easier for the material to deform under stress.
-
Hot or Red Hardness:
- Definition: Hot or red hardness refers to the hardness of a material at high temperatures, where a drastic change in hardness occurs.
- Significance: This property is particularly important for materials used in high-temperature environments, such as turbine blades or engine components, where maintaining hardness at elevated temperatures is crucial for performance and durability.
-
Heat-Treated Alloys:
- Impact of Heat Treatment: Heat-treated alloys, such as those used in tool steels, exhibit enhanced hardness at room temperature due to the formation of specific microstructures like martensite.
- Behavior at High Temperatures: When these alloys are exposed to high temperatures, the microstructures can undergo changes, leading to a significant drop in hardness. Understanding this behavior is essential for selecting the right materials for high-temperature applications.
-
Practical Implications:
- Material Selection: Engineers must consider the hot hardness of materials when designing components that will operate at high temperatures. Materials with high hot hardness are preferred for applications like cutting tools, which need to maintain their edge even when heated.
- Thermal Stability: Ensuring that materials retain their hardness at high temperatures is crucial for the longevity and reliability of components in industries such as aerospace, automotive, and manufacturing.
-
Experimental Observations:
- Testing Methods: Hardness at elevated temperatures is often measured using specialized equipment like hot hardness testers, which can simulate the conditions materials will face in real-world applications.
- Data Interpretation: The data obtained from these tests helps in understanding the thermal stability of materials and in making informed decisions about material selection and heat treatment processes.
In summary, the relationship between temperature and hardness is complex and varies depending on the material and its treatment. Understanding this relationship, especially the concept of hot hardness, is essential for material selection and design in high-temperature applications. This knowledge ensures that materials perform reliably under the thermal stresses they will encounter in service.
Summary Table:
Aspect | Description |
---|---|
General Trend | Hardness decreases as temperature increases due to atomic vibrations. |
Hot or Red Hardness | Drastic change in hardness at high temperatures, crucial for high-temperature applications. |
Heat-Treated Alloys | Enhanced hardness at room temperature; significant drop at high temperatures. |
Practical Implications | Material selection and thermal stability are key for high-temperature performance. |
Testing Methods | Hot hardness testers simulate real-world conditions to measure thermal stability. |
Need help selecting materials for high-temperature applications? Contact our experts today!