Powder metallurgy (PM) is a unique manufacturing process that distinguishes itself from traditional metalworking methods like casting, forging, and machining. Unlike these processes, PM involves compacting metal powders into a desired shape and then sintering them at high temperatures to create a solid, dense component. This method offers unparalleled advantages, including part-to-part uniformity, material flexibility, and cost efficiency. It is particularly suited for producing complex, high-precision parts with minimal material waste. Below, we explore the key differences and advantages of powder metallurgy compared to other manufacturing processes.
Key Points Explained:
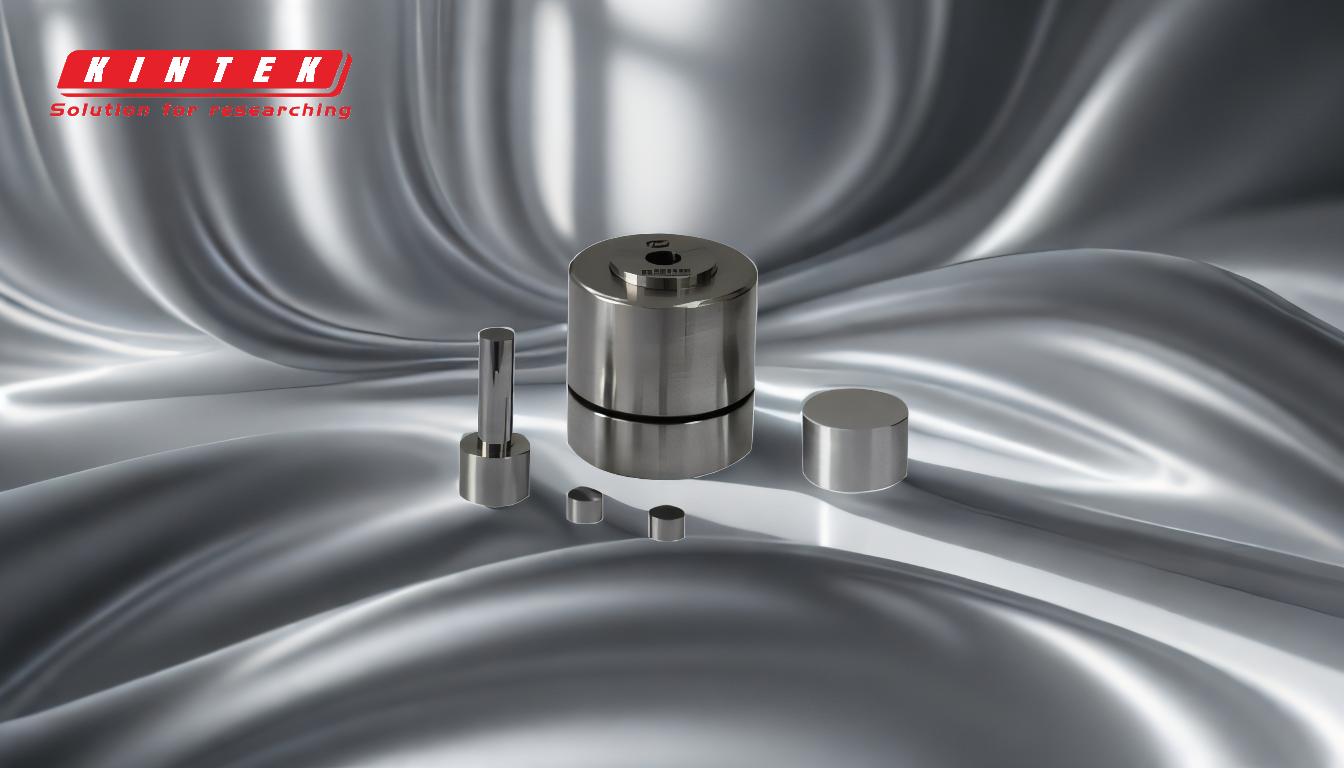
-
Part-to-Part Uniformity and Precision
- Powder metallurgy ensures consistent part dimensions and properties due to the controlled nature of the powder compaction and sintering process.
- Unlike casting or forging, which may suffer from inconsistencies due to cooling rates or material flow, PM produces parts with tight tolerances and minimal variation.
- This uniformity is critical for industries like automotive and aerospace, where precision and reliability are paramount.
-
Material Flexibility
- PM allows for the use of a wide range of materials, including metals, alloys, and composites, which can be tailored to specific applications.
- Unlike traditional processes that may struggle with certain alloys or combinations, PM can incorporate materials like tungsten, titanium, or even ceramic-metal composites.
- This flexibility enables the production of parts with unique properties, such as high strength, wear resistance, or thermal conductivity.
-
Shape Complexity and Design Freedom
- Powder metallurgy excels at producing complex geometries that would be difficult or impossible to achieve with machining, casting, or forging.
- The process can create intricate features like undercuts, thin walls, and internal channels without the need for secondary operations.
- This design freedom reduces the need for assembly and simplifies the manufacturing process.
-
Minimal Material Waste
- PM is a near-net-shape process, meaning the final part is very close to the desired dimensions, requiring little to no additional machining.
- Traditional processes like machining often generate significant scrap material, whereas PM uses almost all the raw material, making it more sustainable and cost-effective.
- This efficiency is particularly beneficial when working with expensive or rare materials.
-
Cost Effectiveness
- The ability to produce complex parts in a single step reduces labor and tooling costs compared to multi-step processes like machining or forging.
- PM also minimizes energy consumption, as sintering typically requires lower temperatures than melting metals in casting.
- For high-volume production, PM offers significant cost savings due to its scalability and efficiency.
-
Application Versatility
- Powder metallurgy is used across a wide range of industries, from automotive (e.g., gears, bearings) to medical (e.g., implants) and electronics (e.g., heat sinks).
- The process can produce parts with specific properties, such as porosity for self-lubricating bearings or high density for structural components.
- This versatility makes PM a preferred choice for applications requiring tailored material performance.
-
Environmental Benefits
- The reduced material waste and energy consumption of PM contribute to a smaller environmental footprint compared to traditional manufacturing methods.
- The ability to recycle metal powders further enhances the sustainability of the process.
- These benefits align with the growing demand for eco-friendly manufacturing solutions.
In summary, powder metallurgy stands out as a highly efficient, versatile, and precise manufacturing process. Its ability to produce complex, high-quality parts with minimal waste and cost makes it a superior choice for many applications. While traditional methods like casting and machining have their place, PM offers unique advantages that are increasingly valued in modern manufacturing.
Summary Table:
Aspect | Powder Metallurgy (PM) | Traditional Methods (Casting, Forging, Machining) |
---|---|---|
Part Uniformity | High precision, consistent dimensions, minimal variation. | Prone to inconsistencies due to cooling rates or material flow. |
Material Flexibility | Wide range of materials, including metals, alloys, and composites. | Limited by material compatibility and processing challenges. |
Shape Complexity | Produces intricate geometries with minimal secondary operations. | Limited by tooling constraints and complexity of machining. |
Material Waste | Near-net-shape process, minimal waste, sustainable. | Generates significant scrap material. |
Cost Efficiency | Lower labor, tooling, and energy costs; scalable for high-volume production. | Higher costs due to multi-step processes and energy-intensive operations. |
Applications | Versatile across industries (automotive, medical, electronics) with tailored properties. | Limited by material and design constraints. |
Environmental Impact | Reduced waste, energy efficiency, and recyclability. | Higher environmental footprint due to waste and energy consumption. |
Ready to leverage the benefits of powder metallurgy for your next project? Contact us today to learn more!