Hardening techniques are essential in materials science and engineering to enhance the mechanical properties of materials, particularly metals. These techniques are designed to increase hardness, strength, and wear resistance, making materials suitable for demanding applications. The primary hardening techniques include work hardening, heat treatment (such as quenching and tempering), case hardening (including carburizing, nitriding, and carbonitriding), precipitation hardening, and surface hardening methods like induction hardening and flame hardening. Each technique has unique mechanisms and applications, depending on the material type and desired properties. Understanding these techniques helps in selecting the appropriate method for specific engineering needs.
Key Points Explained:
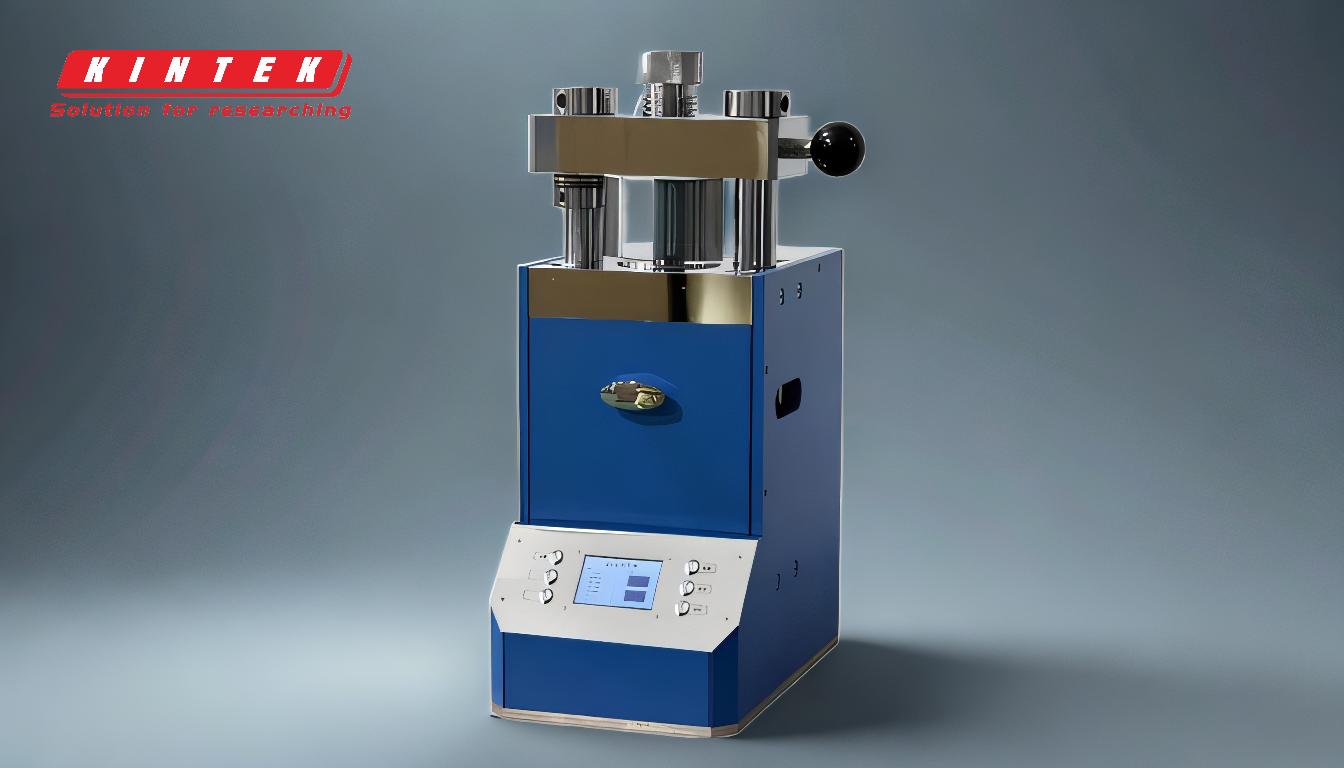
-
Work Hardening:
- Mechanism: Work hardening, also known as strain hardening, occurs when a metal is plastically deformed, increasing its dislocation density. This process makes the metal harder and stronger but reduces its ductility.
- Applications: Commonly used in manufacturing processes like rolling, drawing, and forging. It is particularly useful for materials that need to withstand significant stress without permanent deformation.
-
Heat Treatment:
-
Quenching:
- Mechanism: Rapid cooling of a metal from a high temperature to lock the microstructure in a hardened state, typically martensite.
- Applications: Used for steels to achieve high hardness and strength. Common in tools and automotive components.
-
Tempering:
- Mechanism: Heating quenched metal to a temperature below its critical point to reduce brittleness and improve toughness.
- Applications: Balances hardness and toughness, essential for components like springs and gears.
-
Quenching:
-
Case Hardening:
-
Carburizing:
- Mechanism: Introducing carbon into the surface layer of a low-carbon steel at high temperatures, followed by quenching to harden the surface.
- Applications: Used for gears, camshafts, and other components requiring a hard surface and tough core.
-
Nitriding:
- Mechanism: Introducing nitrogen into the surface of a metal to form hard nitrides, typically at lower temperatures than carburizing.
- Applications: Suitable for components like crankshafts and injection molds that require high surface hardness and wear resistance.
-
Carbonitriding:
- Mechanism: Simultaneous introduction of carbon and nitrogen into the surface layer, combining the benefits of carburizing and nitriding.
- Applications: Used for parts requiring high surface hardness and improved fatigue resistance.
-
Carburizing:
-
Precipitation Hardening:
- Mechanism: Heat treatment process where fine particles (precipitates) form within the metal matrix, impeding dislocation movement and increasing strength.
- Applications: Common in aerospace and high-performance alloys, such as aluminum and nickel-based superalloys.
-
Surface Hardening:
-
Induction Hardening:
- Mechanism: Using electromagnetic induction to heat the surface of a metal, followed by rapid quenching to harden the surface.
- Applications: Ideal for components like shafts and gears that require localized hardening.
-
Flame Hardening:
- Mechanism: Heating the metal surface with a high-temperature flame, followed by quenching.
- Applications: Used for large components or those with complex shapes, such as large gears and dies.
-
Induction Hardening:
Each hardening technique has specific advantages and is chosen based on the material properties and the intended application. Understanding these methods allows for the optimization of material performance in various engineering contexts.
Summary Table:
Technique | Mechanism | Applications |
---|---|---|
Work Hardening | Plastic deformation increases dislocation density, enhancing hardness. | Rolling, drawing, forging for stress-resistant materials. |
Heat Treatment | Quenching and tempering to achieve hardness and toughness. | Tools, automotive components, springs, and gears. |
Case Hardening | Carburizing, nitriding, or carbonitriding to harden the surface. | Gears, camshafts, crankshafts, and injection molds. |
Precipitation Hardening | Formation of precipitates to increase strength. | Aerospace alloys, aluminum, and nickel-based superalloys. |
Surface Hardening | Induction or flame hardening for localized surface hardening. | Shafts, gears, large components, and complex shapes. |
Need help selecting the right hardening technique for your materials? Contact our experts today!