The Hot Isostatic Pressing (HIP) process is a manufacturing technique that utilizes high temperature and high pressure to densify, bond, or shape materials and components. This process is conducted inside a pressure vessel, where an inert gas serves as the pressure-transmitting medium. The vessel contains a resistance-heated furnace to achieve the necessary temperatures. Components are loaded cold, subjected to simultaneous heating and pressurization, cooled within the vessel, and then removed. HIP is widely used to improve material properties, eliminate defects, and enhance the structural integrity of parts.
Key Points Explained:
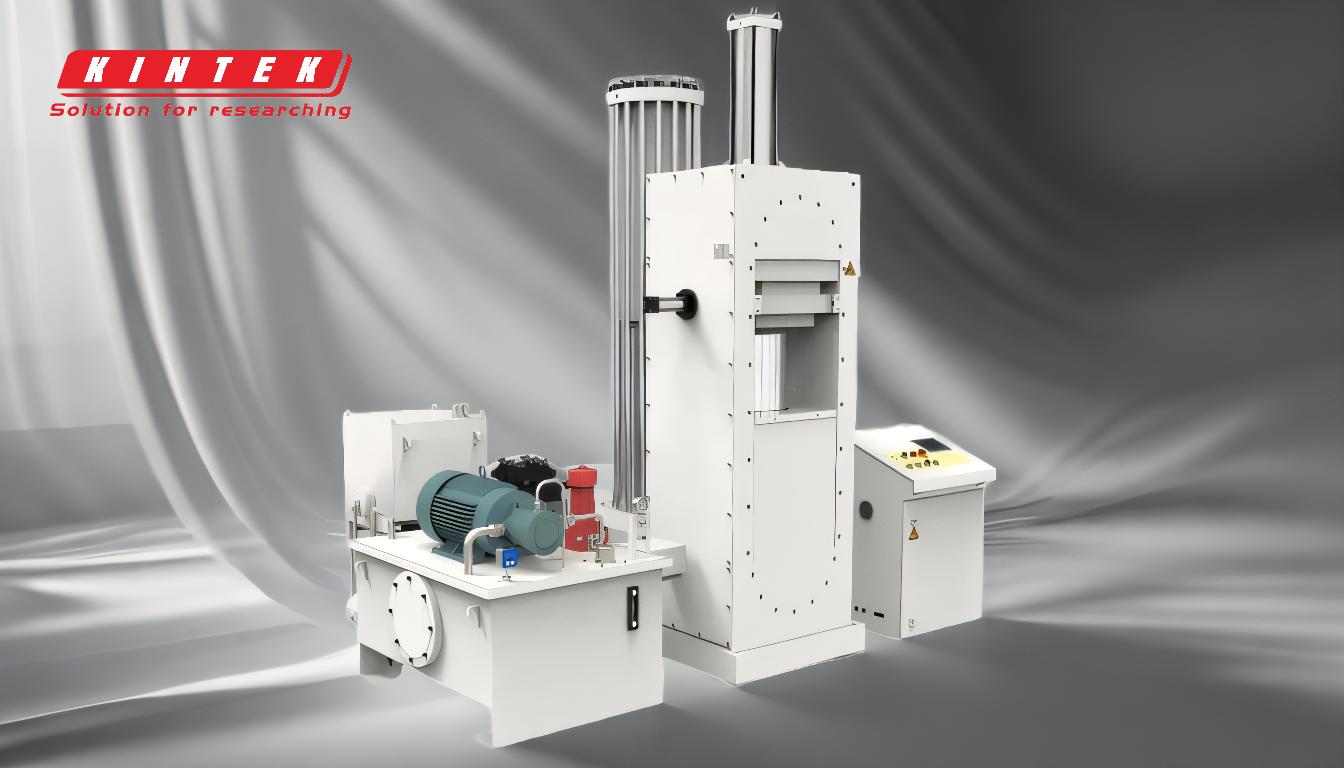
-
Purpose of HIP Process:
- The HIP process is primarily used to densify materials, bond dissimilar materials, or form components into their final shapes. It is particularly effective in eliminating internal porosity, cracks, and voids in materials, which enhances their mechanical properties such as strength, fatigue resistance, and durability.
-
Key Components of HIP:
- Pressure Vessel: The HIP process takes place inside a robust pressure vessel designed to withstand high pressures and temperatures. This vessel is the core component where the transformation of materials occurs.
- Inert Gas: An inert gas, such as argon, is used as the pressure-transmitting medium. It ensures that the materials being processed do not react chemically with the gas, maintaining the integrity of the components.
- Resistance-Heated Furnace: Inside the pressure vessel, a furnace provides the necessary heat. The furnace is typically resistance-heated, allowing precise control over the temperature during the process.
-
Process Steps:
- Cold Loading: Components are loaded into the pressure vessel at room temperature. This step ensures that the materials are not pre-stressed or deformed before the process begins.
- Simultaneous Heating and Pressurization: Once loaded, the vessel is sealed, and both heat and pressure are applied simultaneously. The combination of high temperature and high pressure causes the material to densify or bond.
- Cooling: After the desired temperature and pressure are maintained for a specific duration, the components are cooled inside the vessel. This controlled cooling prevents thermal shock and ensures uniform material properties.
- Removal: Once cooled, the components are removed from the vessel, now with improved density, strength, and structural integrity.
-
Applications of HIP:
- Aerospace: HIP is extensively used in the aerospace industry to produce high-strength, lightweight components such as turbine blades and structural parts.
- Medical: In the medical field, HIP is used to manufacture biocompatible implants with superior mechanical properties and longevity.
- Automotive: The automotive industry utilizes HIP to produce durable and high-performance parts, such as engine components and transmission parts.
- Energy: HIP is employed in the energy sector to create robust components for nuclear reactors and other high-stress environments.
-
Advantages of HIP:
- Improved Material Properties: HIP significantly enhances the mechanical properties of materials by eliminating internal defects.
- Versatility: The process can be applied to a wide range of materials, including metals, ceramics, and composites.
- Complex Geometries: HIP allows for the processing of complex-shaped components that would be difficult to manufacture using traditional methods.
- Enhanced Bonding: HIP is effective in bonding dissimilar materials, creating components with unique properties and functionalities.
In summary, the HIP process is a powerful manufacturing technique that leverages high temperature and high pressure to improve material properties, eliminate defects, and produce high-performance components across various industries. Its ability to densify, bond, and shape materials makes it an invaluable tool in modern manufacturing.
Summary Table:
Aspect | Details |
---|---|
Purpose | Densify materials, bond dissimilar materials, and shape components. |
Key Components | Pressure vessel, inert gas (e.g., argon), resistance-heated furnace. |
Process Steps | Cold loading, simultaneous heating/pressurization, cooling, removal. |
Applications | Aerospace, medical, automotive, and energy industries. |
Advantages | Improved material properties, versatility, complex geometries, enhanced bonding. |
Unlock the potential of the HIP process for your manufacturing needs—contact us today to learn more!