Operating an electric arc furnace (EAF) involves a series of well-defined steps to ensure efficient and safe melting of scrap metal into steel. The process begins with the delivery and preparation of scrap metal, followed by charging the furnace, initiating the meltdown, and refining the molten metal. Key operational considerations include electrode management, power control, and the addition of materials like limestone and oxygen to facilitate slag formation and oxidation. The furnace operates on three-phase electric current, generating intense heat through an electric arc between electrodes and the metal charge. Safety protocols, such as preventing short circuits and managing power levels, are critical throughout the process.
Key Points Explained:
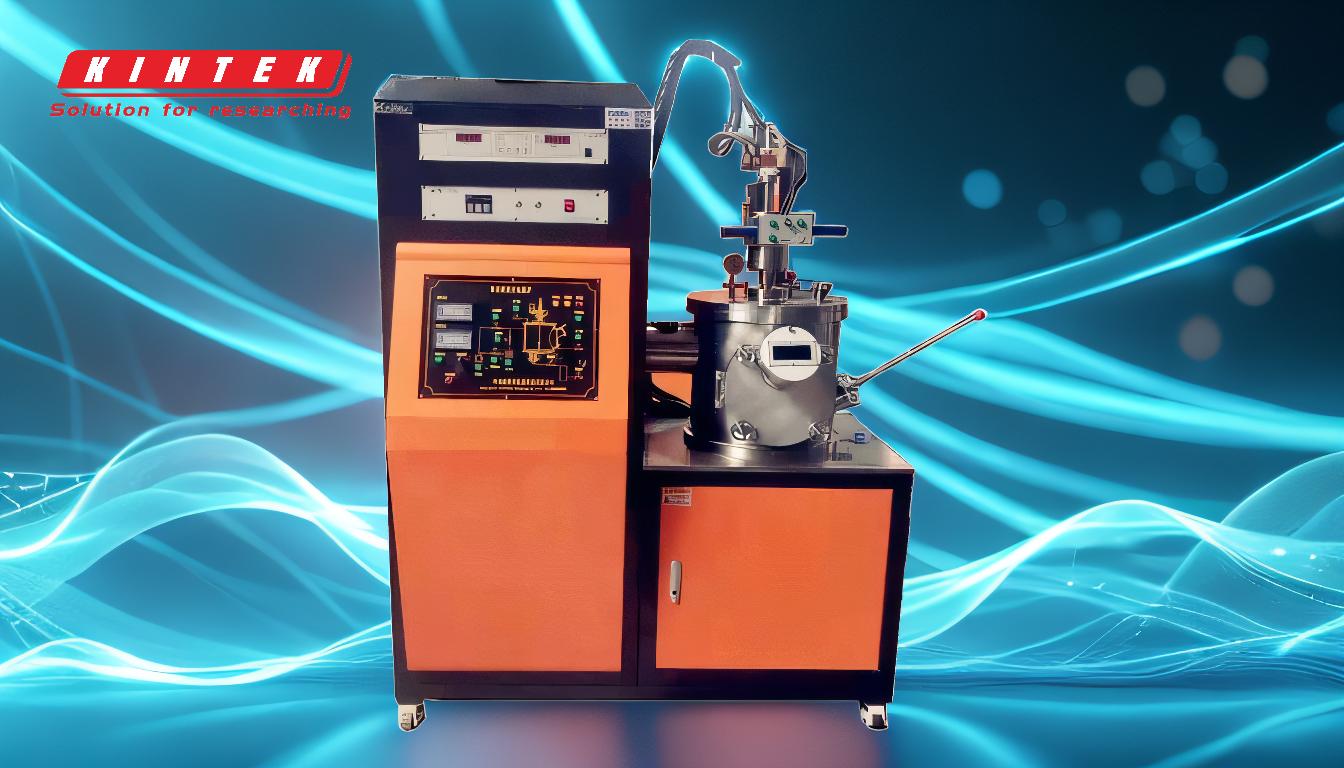
-
Scrap Metal Delivery and Preparation
- Scrap metal is delivered to a scrap bay adjacent to the melt shop.
- The scrap is sorted and loaded into a scrap basket, which is then transported to the melt shop for charging into the furnace.
- Preheating the scrap with exhaust gas can improve energy efficiency.
-
Charging the Furnace
- The furnace roof is swung open, and the scrap basket charges the furnace with a mix of heavy and light scrap.
- Burnt lime and spar may be added to accelerate slag formation.
- The roof is then swung back into place to seal the furnace.
-
Electrode Management and Power Application
- Before powering on, electrodes are raised to prevent short circuits.
- The furnace is powered on at low voltage for the first 10 minutes to stabilize the process.
- Once the electrodes are buried in the scrap, the voltage is increased to maximize melting efficiency.
-
Meltdown Process
- An electric arc is formed between the electrodes and the scrap, generating temperatures up to 3275°F (1800°C).
- The intense heat melts the scrap, with carbon, silicon, and manganese oxidizing during the process.
- Oxygen may be injected to enhance oxidation and refine the molten metal.
-
Energy Consumption and Efficiency
- The process typically requires 350 kWh to 370 kWh of energy per ton of scrap.
- Preheating scrap and optimizing slag formation can reduce energy consumption.
-
Refining and Finalizing the Melt
- After meltdown, the molten metal undergoes refining to adjust its chemical composition.
- Slag is removed, and the molten steel is tapped from the furnace for further processing or casting.
-
Safety and Operational Considerations
- Strict checks are required before powering on to prevent short circuits or equipment damage.
- Power levels must be carefully managed to avoid overloading the system.
- Regular maintenance of electrodes and furnace components is essential for safe and efficient operation.
By following these steps and considerations, operators can effectively manage an electric arc furnace to produce high-quality steel while maintaining safety and energy efficiency.
Summary Table:
Step | Key Actions | Purpose |
---|---|---|
Scrap Metal Delivery & Prep | Sort, load, and preheat scrap metal. | Improve energy efficiency and prepare for melting. |
Charging the Furnace | Add heavy/light scrap, burnt lime, and spar; seal furnace. | Accelerate slag formation and ensure proper melting. |
Electrode Management & Power | Raise electrodes, power on at low voltage, then increase voltage. | Prevent short circuits and optimize melting efficiency. |
Meltdown Process | Generate electric arc (up to 3275°F); oxidize carbon, silicon, and manganese. | Melt scrap and refine molten metal. |
Energy Consumption & Efficiency | Use 350-370 kWh per ton; preheat scrap and optimize slag formation. | Reduce energy consumption and improve efficiency. |
Refining & Finalizing Melt | Adjust chemical composition, remove slag, and tap molten steel. | Produce high-quality steel for further processing. |
Safety & Operational Checks | Prevent short circuits, manage power levels, and maintain equipment. | Ensure safe and efficient furnace operation. |
Ready to optimize your steel production process? Contact us today for expert guidance on electric arc furnaces!