Creating a vacuum in a furnace involves a systematic process that requires specific equipment and techniques to remove air and other gases from the furnace chamber. This process is crucial for applications like heat treatment, where a controlled environment is necessary to prevent oxidation and contamination. The vacuum is achieved using a combination of mechanical pumps, vacuum valves, and other components that work together to reduce the pressure inside the furnace. Proper spacing of workpieces, controlled heating, and cooling processes are also essential to maintain the vacuum and ensure the desired outcomes.
Key Points Explained:
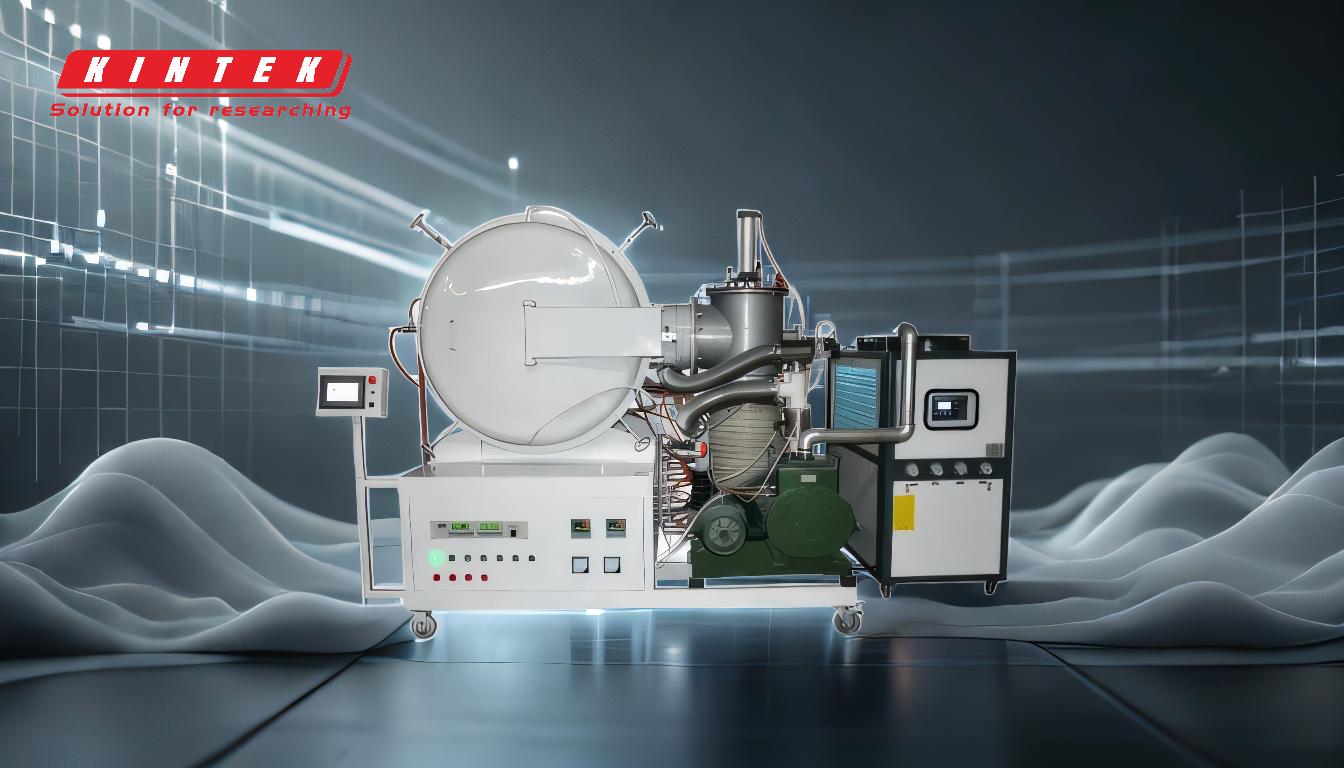
-
Initial Evacuation Process:
- The first step in creating a vacuum is to close all vacuum valves and start the mechanical pump. Once the pump is operating normally, the low vacuum valve to the furnace body is opened slowly to pre-extract air from the furnace chamber. This step is critical to prevent oil spray from the mechanical pump exhaust port, which could contaminate the furnace environment.
-
Mechanical Pump Functionality:
- A mechanical pump, often a positive displacement pump, is used to create a rough or partial vacuum. This type of pump transports gas from the inlet port to the outlet port, effectively reducing the pressure inside the furnace. However, due to mechanical limitations, these pumps can only achieve a low vacuum. For higher vacuum levels, additional pumps like diffusion pumps or turbomolecular pumps are required.
-
Heating in a Vacuum Environment:
- Heating in a vacuum furnace primarily relies on radiation. Proper spacing of workpieces within the furnace is essential to ensure uniform heating. This method of heating prevents oxidation and contamination, which are common issues in non-vacuum environments.
-
Cooling Process:
- Cooling in a vacuum furnace can be controlled using a pre-set program or by turning off the heating to allow natural cooling. It is crucial to ensure that cooling water is not stopped during this process, as it could damage the furnace seal and compromise the vacuum.
-
Removal of Water Vapor:
- During the initial evacuation, the furnace is pumped until it reaches a slowly dropping rate before introducing partial pressure or turning on the heat. This step helps remove water vapor, which is particularly challenging to eliminate in humid environments. Proper removal of water vapor reduces the risk of discoloration and other issues that could affect the quality of the workpiece.
-
Vacuum System Components:
- The vacuum system in a furnace includes various components such as vacuum pumps, vacuum measuring devices, and vacuum valves. These components work together to remove air from the furnace chamber, reducing the pressure below standard atmospheric pressure to create a vacuum. The efficiency of these components directly impacts the quality of the vacuum achieved.
-
Quenching Process:
- For quenching, the water tank on the bottom frame is moved to just below the furnace hood. The furnace door is opened, and the chain is used to lower the basket (workpiece) into the water. This process is essential for rapid cooling and achieving the desired material properties.
By following these steps and understanding the role of each component, a vacuum can be effectively created and maintained in a furnace, ensuring optimal conditions for various industrial processes.
Summary Table:
Step | Key Process | Purpose |
---|---|---|
Initial Evacuation | Close vacuum valves, start mechanical pump, and slowly open low vacuum valve. | Pre-extract air to prevent contamination and oil spray. |
Mechanical Pump | Use positive displacement pumps to create a rough vacuum. | Reduce pressure inside the furnace for initial vacuum creation. |
Heating in Vacuum | Rely on radiation with proper workpiece spacing. | Ensure uniform heating and prevent oxidation/contamination. |
Cooling Process | Use pre-set programs or natural cooling with continuous cooling water flow. | Maintain furnace seal integrity and prevent damage during cooling. |
Removal of Water Vapor | Pump until slow drop rate, then introduce partial pressure or heat. | Eliminate water vapor to prevent discoloration and quality issues. |
Vacuum System Components | Include pumps, measuring devices, and valves to remove air. | Achieve and maintain desired vacuum levels for industrial processes. |
Quenching Process | Move water tank, open furnace door, and lower workpiece into water. | Rapidly cool workpieces to achieve desired material properties. |
Need expert guidance on creating a vacuum in your furnace? Contact us today for tailored solutions!