Hot isostatic pressing (HIP) is a highly effective manufacturing process that enhances material properties and structural integrity by applying high temperature and pressure simultaneously. This process eliminates internal voids, defects, and residual porosity, resulting in materials with improved density, mechanical performance, and durability. HIP is widely used in industries such as aerospace, automotive, and medical devices to produce components with superior wear resistance, corrosion resistance, and fatigue life. Additionally, HIP reduces production costs by minimizing scrap, improving yield, and optimizing material properties, making it a valuable addition to modern manufacturing processes.
Key Points Explained:
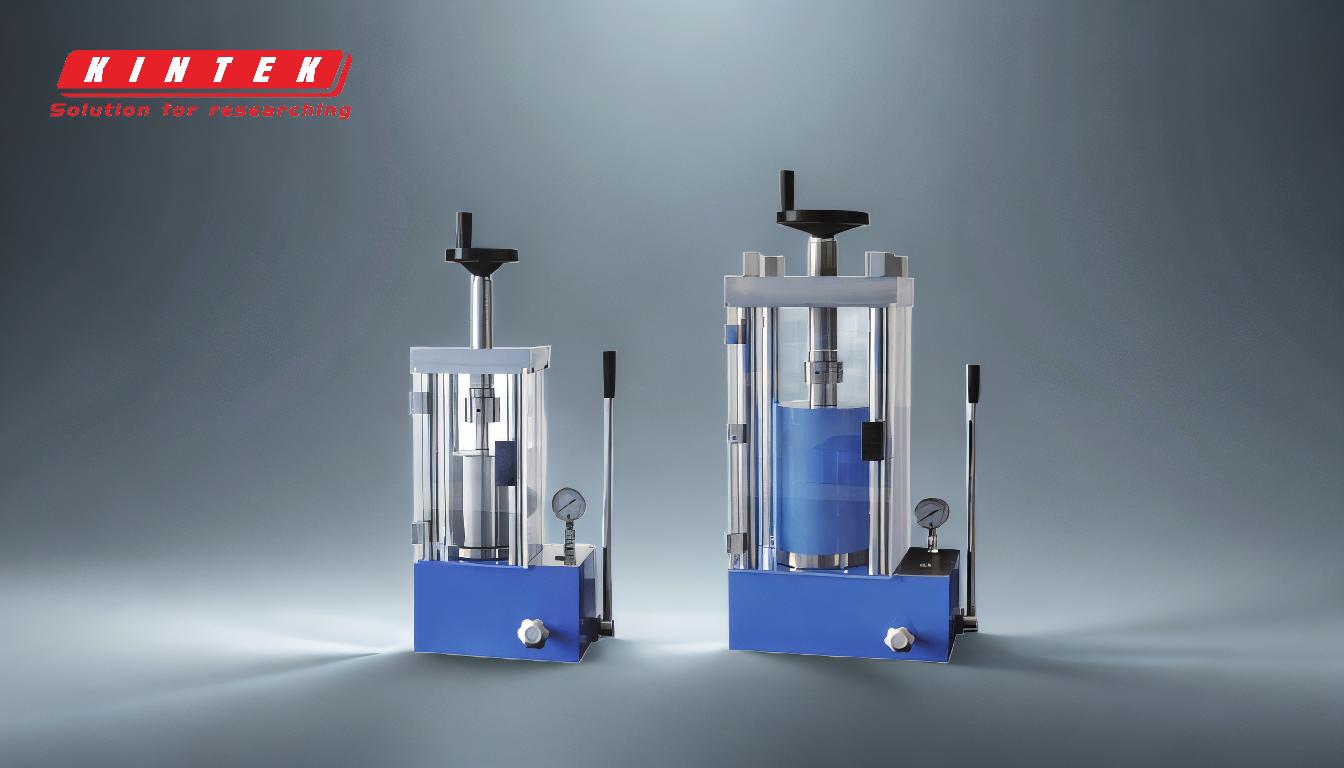
-
Improved Material Properties
- HIP significantly enhances material properties such as wear resistance, corrosion resistance, and mechanical performance.
- By eliminating internal voids and defects, HIP increases the density of materials, bringing it closer to the theoretical density.
- This process is particularly beneficial for materials used in harsh environments, as it improves their ability to withstand heat, wear, fatigue, and abrasion.
- For example, HIP can increase the fatigue life of materials by 10 to 100 times, making them more reliable for critical applications.
-
Enhanced Structural Integrity
- HIP eliminates residual porosity from sintered powder metallurgy (PM) parts, improving their structural integrity and density.
- This process combines compaction and sintering under high heat and pressure, solidifying powder particles and repairing voids and pores.
- The result is a high-strength, dense structure that shrinks and densifies during the process, ensuring uniform material properties throughout the part.
-
Cost-Effective Manufacturing
- Incorporating HIP into the manufacturing process reduces scrap and improves yield, leading to significant cost savings.
- It often allows the replacement of wrought components with castings, further reducing production costs.
- HIP minimizes quality assurance inspection requirements by improving material properties and reducing property scatter, which can offset the costs of the process.
- Additionally, HIP optimizes material properties, reducing the need for subsequent heat treatments and lowering overall production costs.
-
Versatility Across Manufacturing Methods
- HIP is compatible with various metal manufacturing methods, including casting, forging, powder metallurgy, and additive manufacturing.
- It is particularly useful for producing large or complex parts where traditional pressing dies may not be cost-effective.
- For example, cold isostatic pressing (CIP) is often used as a precursor to HIP for compacting products before sintering and final densification.
-
Improved Part Reliability and Service Life
- By enhancing material properties and eliminating defects, HIP significantly improves part reliability and extends service life.
- This makes HIP-treated components ideal for demanding applications in industries such as aerospace, where performance and durability are critical.
- The process also enables the production of smaller and lighter-weight parts with similar or superior performance, contributing to overall efficiency.
-
Environmental and Economic Benefits
- HIP reduces the need for radiographic inspections, as the process inherently improves material quality and reduces defects.
- The savings from reduced inspection requirements can often cover the costs of HIP, making it an economically viable option.
- By minimizing waste and optimizing material usage, HIP also contributes to more sustainable manufacturing practices.
In summary, hot isostatic pressing (HIP) offers numerous benefits, including enhanced material properties, improved structural integrity, cost savings, and increased part reliability. Its versatility and compatibility with various manufacturing methods make it a valuable tool for producing high-performance components in demanding industries. For more information on related processes, you can explore warm isostatic press.
Summary Table:
Benefit | Description |
---|---|
Improved Material Properties | Enhances wear, corrosion resistance, and mechanical performance. |
Enhanced Structural Integrity | Eliminates voids and porosity, ensuring uniform density and strength. |
Cost-Effective Manufacturing | Reduces scrap, improves yield, and lowers production costs. |
Versatility | Compatible with casting, forging, powder metallurgy, and additive manufacturing. |
Improved Reliability | Extends part service life and reliability for critical applications. |
Environmental Benefits | Minimizes waste and reduces inspection requirements, promoting sustainability. |
Unlock the full potential of hot isostatic pressing for your manufacturing needs—contact us today to learn more!