Heat treatment is a critical process in metallurgy, but it is prone to defects if not carefully controlled. Common defects include surface decarburization, quenching cracks, soft spots, and microstructural irregularities. These defects arise due to improper temperature control, inadequate cooling rates, or insufficient gas circulation. Addressing these issues requires precise process adjustments, such as optimizing cycle times, ensuring uniform temperature distribution, and implementing proper quenching techniques. By understanding the root causes and applying remedial measures, manufacturers can minimize defects and improve the quality of heat-treated components.
Key Points Explained:
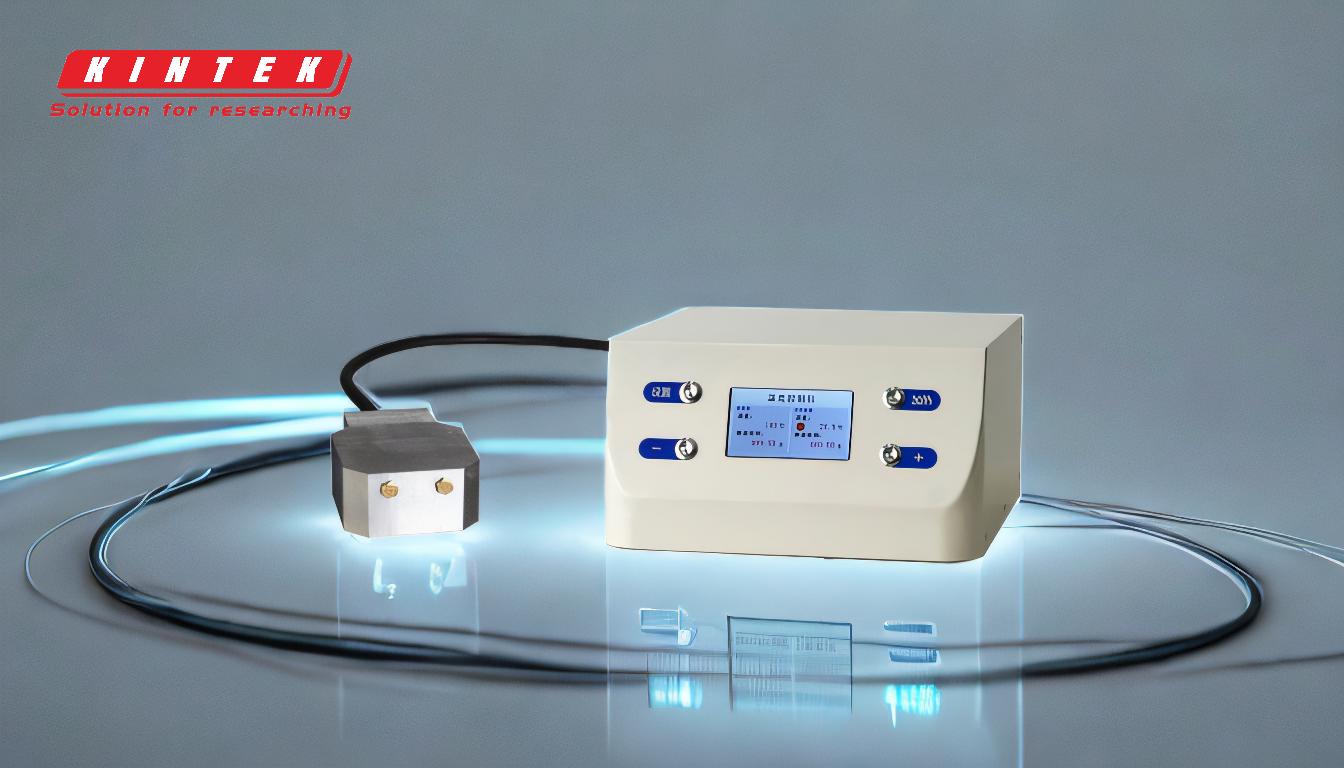
-
Surface Decarburization
- Definition: Loss of carbon from the surface layer of steel during heat treatment, leading to reduced hardness and strength.
- Causes: Exposure to oxidizing atmospheres at high temperatures or insufficient protective gas circulation.
- Remedial Measures: Use controlled atmospheres (e.g., inert gases) to prevent oxidation, or apply protective coatings to the material surface.
-
Quenching Cracks
- Definition: Cracks that form during rapid cooling (quenching) due to thermal stresses and uneven cooling rates.
- Causes: Improper quenching medium, excessive cooling rates, or inadequate part design (e.g., sharp corners).
- Remedial Measures: Optimize quenching medium (e.g., oil, water, or polymer), reduce cooling rates, or redesign parts to avoid stress concentration areas.
-
Soft Spots
- Definition: Areas on the material surface that remain softer than the surrounding regions due to inconsistent cooling or heating.
- Causes: Non-uniform temperature distribution, inadequate gas circulation, or improper quenching techniques.
- Remedial Measures: Ensure uniform heating and cooling by improving furnace design, enhancing gas circulation, and using proper quenching methods.
-
Microstructural Defects
- Definition: Irregularities in the material's microstructure, such as grain growth or phase transformation issues.
- Causes: Incorrect temperature or time settings during heating or cooling, or improper material selection.
- Remedial Measures: Adjust heat treatment parameters (temperature, time, and cooling rate) based on material properties and desired outcomes.
-
Heat Treatment Deformation and Ovality
- Definition: Warping or distortion of parts during heat treatment, often due to uneven heating or cooling.
- Causes: Non-uniform temperature distribution, improper part support during heating, or rapid cooling rates.
- Remedial Measures: Use fixtures to support parts during heating, optimize furnace design for uniform temperature, and control cooling rates.
-
Process Control and Design Modifications
- Importance: Proper process control is essential to prevent defects and ensure consistent quality.
-
Key Factors:
- Uniform temperature distribution throughout the hot zone.
- Proper gas circulation to maintain partial pressure or quench gas flow.
- Accurate cycle times and temperatures tailored to the material and application.
- Design Considerations: Anticipate potential issues (e.g., stress concentrations) and modify part designs to minimize risks.
By addressing these key points and implementing corrective measures, manufacturers can significantly reduce heat treatment defects, ensuring high-quality outcomes for their products.
Summary Table:
Defect Type | Causes | Remedial Measures |
---|---|---|
Surface Decarburization | Oxidizing atmospheres, insufficient gas circulation | Use controlled atmospheres, apply protective coatings |
Quenching Cracks | Improper quenching medium, excessive cooling rates, poor part design | Optimize quenching medium, reduce cooling rates, redesign parts |
Soft Spots | Non-uniform temperature, inadequate gas circulation, improper quenching | Improve furnace design, enhance gas circulation, use proper quenching methods |
Microstructural Defects | Incorrect temperature/time settings, improper material selection | Adjust heat treatment parameters based on material properties |
Deformation and Ovality | Uneven heating/cooling, improper part support, rapid cooling rates | Use fixtures, optimize furnace design, control cooling rates |
Need help optimizing your heat treatment process? Contact our experts today for tailored solutions!