Sintering is a widely used process in powder metallurgy and ceramics, offering numerous advantages such as improved material density, strength, and wear resistance. However, it also has several limitations that can affect the quality and uniformity of the final product. These limitations include challenges in achieving uniform sizes, the destruction of micro- and nanostructures during the process, and the inability to use 100% sintered materials in certain applications like blast furnaces. Additionally, while advanced sintering furnaces, such as vacuum and hot press sintering furnaces, mitigate some of these issues, they come with their own set of challenges, including high equipment costs and the need for professional operation and maintenance.
Key Points Explained:
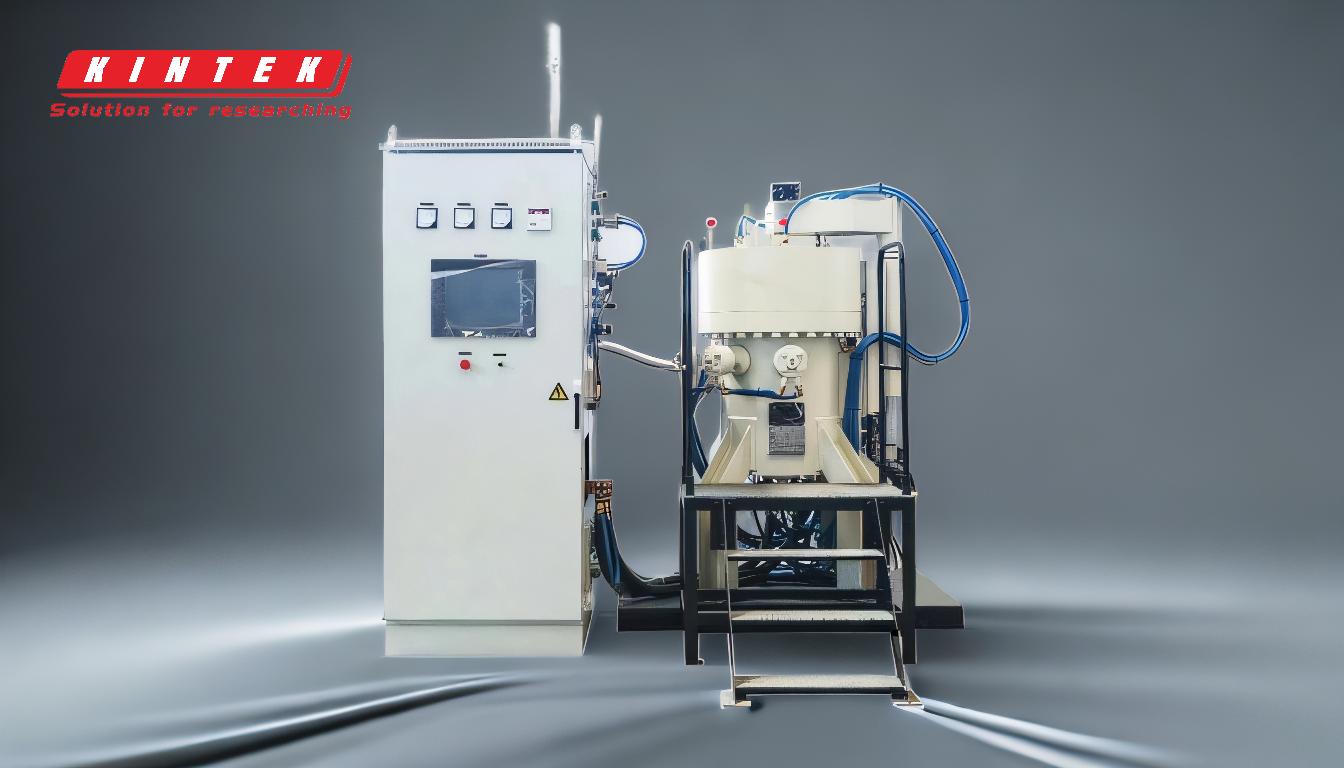
-
Inability to Use 100% Sintered Materials in Certain Applications:
- Sintering cannot produce materials that are 100% sintered, such as iron ore, for use in blast furnaces. This limitation restricts the application of sintered materials in industries where fully sintered products are required.
-
Difficulty in Achieving Uniform Sizes:
- One of the significant limitations of sintering is the challenge in creating uniform sizes. This inconsistency can lead to variations in the final product's properties, affecting its performance and reliability.
-
Destruction of Micro- and Nanostructures:
- The sintering process often destroys micro- and nanostructures that were present before sintering. This can negatively impact the material's properties, such as strength and wear resistance, which are crucial for high-performance applications.
-
Contamination and Adverse Reactions:
- Traditional sintering processes can lead to contamination from harmful substances in the atmosphere, such as water, oxygen, and nitrogen. These contaminants can cause adverse reactions like decarburization, carburization, reduction, oxidation, and nitriding, which degrade the material's quality.
-
High Equipment and Operational Costs:
- Advanced sintering furnaces, such as vacuum sintering furnaces and hot press sintering furnaces, offer several advantages, including reduced contamination and improved material properties. However, these furnaces come with high equipment costs and require professional operation and maintenance, which can be a barrier for smaller enterprises.
-
Complexity in Ensuring Uniformity and Stability:
- Ensuring the uniformity and stability of pressure and temperature during the sintering process is crucial. Any deviation can lead to product defects, making the process more complex and requiring precise control systems.
-
Economic Considerations:
- While sintering can offer economic benefits by reducing production cycles and labor costs, the initial investment in high-quality sintering equipment can be substantial. This economic consideration is particularly relevant for medium-sized sintering furnaces, which are the most common but still require a significant investment.
-
Material-Specific Limitations:
- Different materials have specific requirements and limitations when it comes to sintering. For example, ceramic materials may require specialized sintering furnaces to achieve the desired properties, adding another layer of complexity to the process.
In summary, while sintering is a versatile and valuable process in material science, it comes with several limitations that need to be carefully managed. These include challenges in achieving uniform sizes, the destruction of micro- and nanostructures, contamination issues, high equipment and operational costs, and the complexity of ensuring process uniformity. Understanding these limitations is crucial for optimizing the sintering process and achieving high-quality final products.
Summary Table:
Limitation | Description |
---|---|
Inability to use 100% sintered materials | Cannot produce fully sintered materials for applications like blast furnaces. |
Difficulty in achieving uniform sizes | Inconsistent sizes lead to variations in final product properties. |
Destruction of micro- and nanostructures | Sintering can destroy pre-existing micro- and nanostructures. |
Contamination and adverse reactions | Atmospheric contaminants cause reactions like oxidation and decarburization. |
High equipment and operational costs | Advanced furnaces are costly and require professional maintenance. |
Complexity in uniformity and stability | Precise control of pressure and temperature is essential to avoid defects. |
Economic considerations | High initial investment in equipment, despite long-term economic benefits. |
Material-specific limitations | Different materials require specialized sintering processes. |
Need help overcoming sintering challenges? Contact our experts today for tailored solutions!