Brazing is a widely used joining process that involves melting a filler metal to join two or more base metals without melting the base materials. The choice of brazing rods depends on the materials being joined, the application, and the specific brazing method used. The most common brazing rods are made from materials like aluminum-silicon alloys, copper-phosphorus alloys, silver-based alloys, and nickel-based alloys. Each type has unique properties that make it suitable for specific applications, such as high-temperature environments, corrosion resistance, or electrical conductivity.
Key Points Explained:
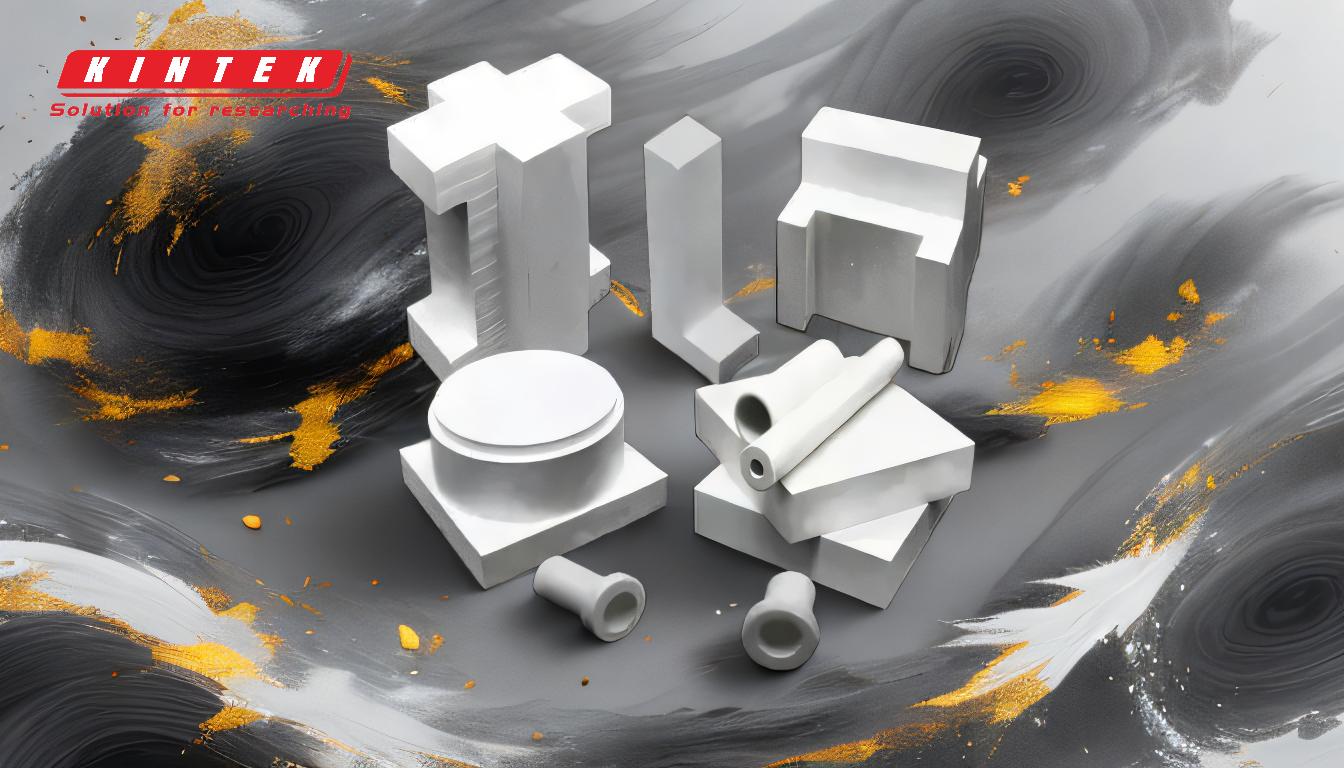
-
Aluminum-Silicon Brazing Rods:
- Composition: These rods are typically made from aluminum alloys with silicon content ranging from 7% to 12%.
- Applications: They are commonly used for brazing aluminum and aluminum alloys, particularly in the automotive and HVAC industries.
- Advantages: They offer excellent corrosion resistance and are suitable for joining thin aluminum sheets.
- Limitations: They require careful temperature control to avoid melting the base material.
-
Copper-Phosphorus Brazing Rods:
- Composition: These rods are made from copper with a small percentage of phosphorus, often around 6-8%.
- Applications: They are widely used for brazing copper and copper alloys, such as brass and bronze, in plumbing, refrigeration, and electrical applications.
- Advantages: They are self-fluxing, meaning they do not require additional flux, and they provide strong, leak-proof joints.
- Limitations: They are not suitable for ferrous metals or high-stress applications.
-
Silver-Based Brazing Rods:
- Composition: These rods contain silver as the primary component, often combined with copper, zinc, and cadmium.
- Applications: They are used for brazing a wide range of metals, including stainless steel, copper, and nickel alloys, in industries like aerospace, electronics, and jewelry making.
- Advantages: They offer excellent flow characteristics, high strength, and good electrical conductivity.
- Limitations: They are more expensive than other types of brazing rods and may require flux for certain applications.
-
Nickel-Based Brazing Rods:
- Composition: These rods are made from nickel alloys, often with additions of chromium, boron, and silicon.
- Applications: They are used for brazing high-temperature alloys, such as those found in gas turbines, jet engines, and power generation equipment.
- Advantages: They provide excellent strength and corrosion resistance at high temperatures.
- Limitations: They require specialized equipment and precise temperature control.
-
Other Types of Brazing Rods:
- Gold-Based Brazing Rods: Used in specialized applications like semiconductor manufacturing and high-reliability electronics due to their excellent conductivity and resistance to oxidation.
- Titanium-Based Brazing Rods: Used in aerospace and medical applications where high strength-to-weight ratios and biocompatibility are required.
- Magnesium-Based Brazing Rods: Used for joining magnesium alloys in lightweight structures, such as those in the automotive and aerospace industries.
In conclusion, the most common brazing rods are tailored to specific materials and applications, ensuring strong, durable, and reliable joints. The choice of brazing rod depends on factors such as the base metals, the required joint strength, and the operating environment.
Summary Table:
Brazing Rod Type | Composition | Applications | Advantages | Limitations |
---|---|---|---|---|
Aluminum-Silicon | Aluminum alloys with 7-12% silicon | Automotive, HVAC industries | Excellent corrosion resistance, suitable for thin aluminum sheets | Requires careful temperature control |
Copper-Phosphorus | Copper with 6-8% phosphorus | Plumbing, refrigeration, electrical applications | Self-fluxing, strong, leak-proof joints | Not suitable for ferrous metals or high-stress applications |
Silver-Based | Silver with copper, zinc, cadmium | Aerospace, electronics, jewelry making | Excellent flow, high strength, good electrical conductivity | Expensive, may require flux |
Nickel-Based | Nickel with chromium, boron, silicon | Gas turbines, jet engines, power generation | High strength, corrosion resistance at high temperatures | Requires specialized equipment and precise temperature control |
Gold-Based | Gold alloys | Semiconductor manufacturing, high-reliability electronics | Excellent conductivity, oxidation resistance | High cost |
Titanium-Based | Titanium alloys | Aerospace, medical applications | High strength-to-weight ratio, biocompatibility | Specialized use cases |
Magnesium-Based | Magnesium alloys | Automotive, aerospace lightweight structures | Lightweight, suitable for magnesium alloys | Limited to specific applications |
Need help selecting the right brazing rod for your project? Contact our experts today!