Heat treatment is a critical process in metallurgy that involves controlled heating and cooling to alter the microstructure of metals or alloys, thereby achieving desired mechanical properties. The two fundamental principles of heat treatment are hardening and annealing. Hardening aims to increase the strength and wear resistance of the material, while annealing focuses on softening the material, improving ductility, and reducing internal stresses. These principles are essential for tailoring the properties of metals to meet specific industrial requirements.
Key Points Explained:
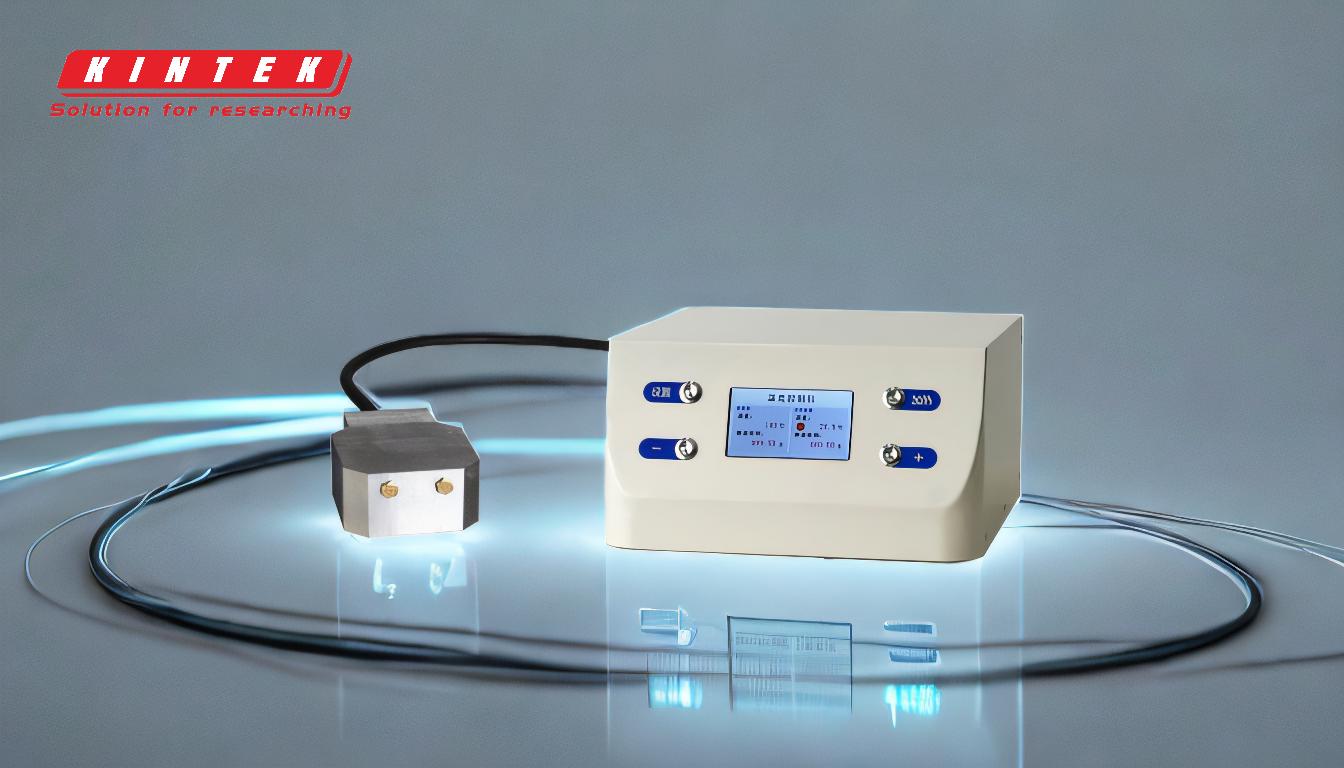
-
Hardening:
- Objective: The primary goal of hardening is to increase the hardness and strength of the metal. This is achieved by heating the metal to a specific temperature (above its critical temperature) and then rapidly cooling it, typically through quenching in water, oil, or air.
- Microstructural Changes: During hardening, the metal undergoes a phase transformation. For example, in steel, the austenite phase transforms into martensite, a hard and brittle structure. This transformation is responsible for the increased hardness.
- Applications: Hardening is widely used in the manufacturing of tools, gears, and components that require high wear resistance and durability. It is particularly important in industries such as automotive, aerospace, and construction.
-
Annealing:
- Objective: Annealing is designed to soften the metal, improve its ductility, and relieve internal stresses. This process involves heating the metal to a specific temperature and then allowing it to cool slowly, often in a furnace.
- Microstructural Changes: During annealing, the metal's microstructure is refined, and any dislocations or defects are reduced. This results in a more uniform and stress-free structure, which enhances the metal's workability.
- Applications: Annealing is commonly used in the production of sheet metal, wires, and other forms that require further processing. It is also essential in the manufacturing of components that need to be machined or formed without cracking.
-
Controlled Heating and Cooling:
- Importance: Both hardening and annealing rely on precise control of heating and cooling rates. The temperature and duration of heating, as well as the cooling medium and rate, must be carefully controlled to achieve the desired properties.
- Equipment: Heat treatment furnaces, quenching tanks, and temperature control systems are essential for maintaining the required conditions. Advanced technologies, such as induction heating and vacuum furnaces, are often used for precise heat treatment processes.
-
Material Selection and Heat Treatment Compatibility:
- Material Considerations: Not all metals and alloys respond to heat treatment in the same way. The effectiveness of hardening and annealing depends on the material's composition and initial microstructure. For example, carbon steels are more responsive to hardening than some stainless steels.
- Heat Treatment Compatibility: It is crucial to select the appropriate heat treatment method based on the material's properties and the desired outcome. Improper heat treatment can lead to undesirable results, such as excessive brittleness or insufficient hardness.
-
Quality Control and Testing:
- Testing Methods: After heat treatment, the material's properties must be verified through various testing methods, such as hardness testing, tensile testing, and microscopic examination. These tests ensure that the heat treatment has achieved the desired results.
- Quality Assurance: Consistent quality control is essential to maintain the reliability and performance of heat-treated components. This includes monitoring the heat treatment process, inspecting the final product, and documenting the results.
In summary, the principles of hardening and annealing are foundational to the heat treatment process, enabling the customization of metal properties to meet specific industrial needs. Understanding these principles and their applications is crucial for anyone involved in the selection, processing, or quality control of metal components.
Summary Table:
Principle | Objective | Process | Applications |
---|---|---|---|
Hardening | Increase hardness and strength | Heat above critical temperature, then rapid cooling (quenching) | Tools, gears, automotive, aerospace, construction |
Annealing | Soften metal, improve ductility, reduce internal stresses | Heat to specific temperature, then slow cooling | Sheet metal, wires, machined components |
Heating/Cooling | Precise control of temperature and cooling rates | Use of furnaces, quenching tanks, and temperature control systems | Customizing metal properties for specific needs |
Material Selection | Compatibility with heat treatment methods | Select materials based on composition and desired outcomes | Ensuring effective hardening or annealing |
Quality Control | Verify properties through testing (hardness, tensile, microscopic analysis) | Monitor process, inspect final product, document results | Ensuring reliability and performance of heat-treated components |
Need expert advice on heat treatment processes? Contact us today to optimize your metal properties!