A melting furnace is primarily used to liquefy materials, typically metals, for casting or further processing. While the term "melting furnace" is widely used, it can also be referred to as a "foundry furnace" or "smelting furnace," depending on the context and application. These furnaces are designed to reach high temperatures to melt materials, unlike sintering furnaces, which focus on heating powder compacts to enhance mechanical properties without liquefaction. The distinction between melting and sintering furnaces lies in their purpose and the processes they facilitate.
Key Points Explained:
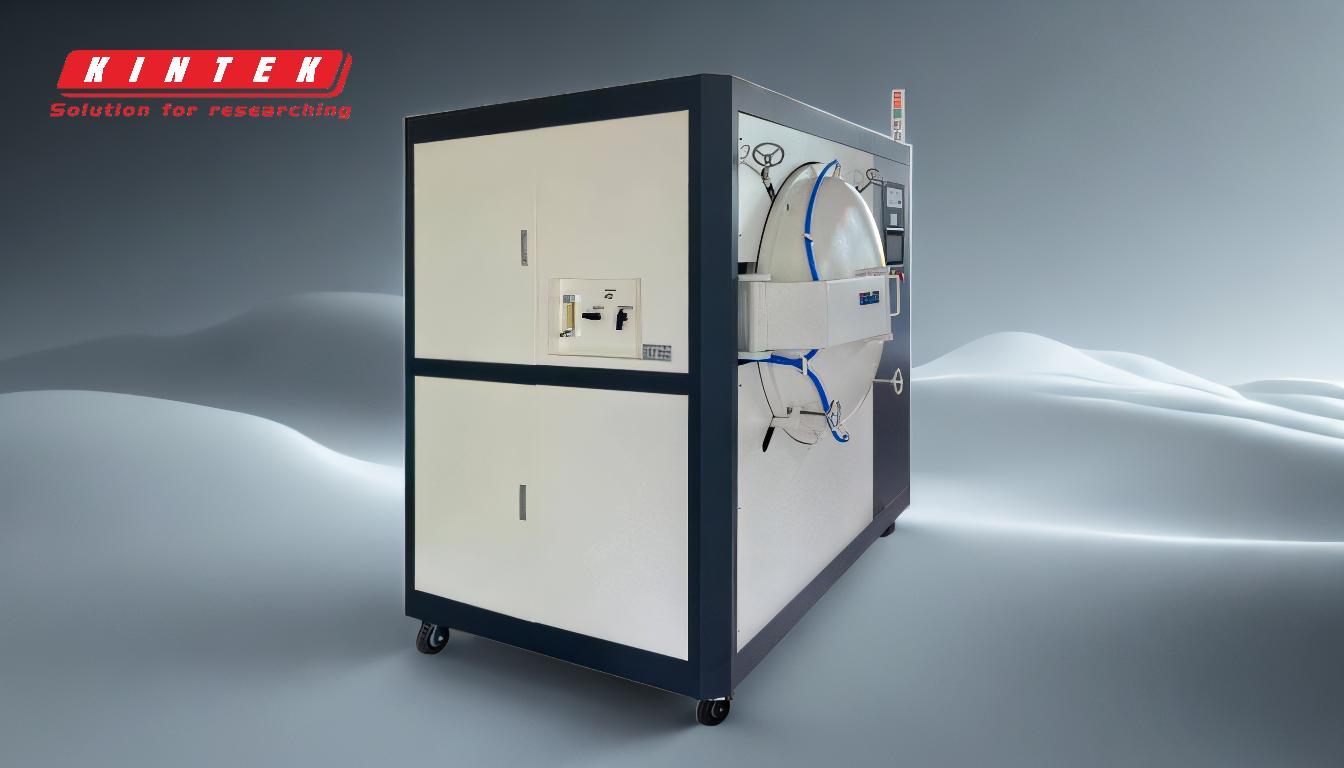
-
Primary Function of a Melting Furnace:
- A melting furnace is designed to heat materials, particularly metals, to their melting point, converting them into a liquid state. This is essential for processes like casting, alloying, or recycling metals. The furnace must achieve and maintain extremely high temperatures to ensure complete liquefaction.
-
Alternative Names for a Melting Furnace:
- Foundry Furnace: This term is often used interchangeably with a melting furnace, especially in industrial settings where metals are melted for casting into molds. Foundry furnaces are integral to metalworking and manufacturing industries.
- Smelting Furnace: Smelting refers to the process of extracting metal from its ore by heating and melting. A smelting furnace is specifically designed for this purpose, often used in mining and metallurgical operations.
-
Comparison with Sintering Furnaces:
- Unlike a melting furnace, a sintering furnace does not aim to liquefy materials. Instead, it heats powder compacts to bond particles together, enhancing mechanical strength, density, and translucency. This process is crucial in powder metallurgy and ceramic manufacturing.
- The sintering process involves lower temperatures compared to melting, as the goal is to shape the material into its final form without reaching a liquid state.
-
Types of Melting Furnaces:
- Induction Furnace: Uses electromagnetic induction to generate heat and melt metals. It is highly efficient and commonly used in foundries.
- Arc Furnace: Utilizes an electric arc to produce high temperatures, suitable for melting scrap metal and producing steel.
- Crucible Furnace: A small-scale furnace where materials are placed in a crucible and heated to melting point, often used in laboratories or small workshops.
-
Applications of Melting Furnaces:
- Metal Casting: Used to melt metals for casting into molds, producing components for automotive, aerospace, and construction industries.
- Alloy Production: Essential for creating alloys by melting and mixing different metals to achieve desired properties.
- Recycling: Melting furnaces are used to recycle scrap metal, reducing waste and conserving resources.
-
Key Considerations for Purchasing a Melting Furnace:
- Temperature Range: Ensure the furnace can reach and maintain the required temperatures for the materials being processed.
- Energy Efficiency: Consider the furnace's energy consumption and operational costs.
- Capacity: Choose a furnace size that matches the volume of material to be melted.
- Safety Features: Look for features like temperature control, insulation, and ventilation to ensure safe operation.
By understanding the distinctions and applications of melting furnaces, purchasers can make informed decisions based on their specific needs, whether for industrial metalworking, recycling, or laboratory research.
Summary Table:
Term | Description |
---|---|
Melting Furnace | Heats materials, typically metals, to their melting point for casting or recycling. |
Foundry Furnace | Used interchangeably with melting furnace, especially in metal casting industries. |
Smelting Furnace | Designed for extracting metal from ore by heating and melting, common in mining. |
Need help choosing the right furnace for your needs? Contact our experts today!