Chemical vapor deposition (CVD) is a critical process in semiconductor manufacturing, used to deposit high-quality, high-performance thin films onto substrates. It involves exposing a substrate to volatile precursors in a vacuum environment, where chemical reactions occur to form a solid film. The process is highly controlled, ensuring uniformity and precision, which are essential for semiconductor devices. CVD is widely used due to its ability to produce films with excellent electrical, thermal, and mechanical properties. However, it requires sophisticated equipment, making it costly and time-consuming, especially for large-scale production. The process is environmentally friendly and controllable, making it a preferred method for producing advanced materials in the semiconductor industry.
Key Points Explained:
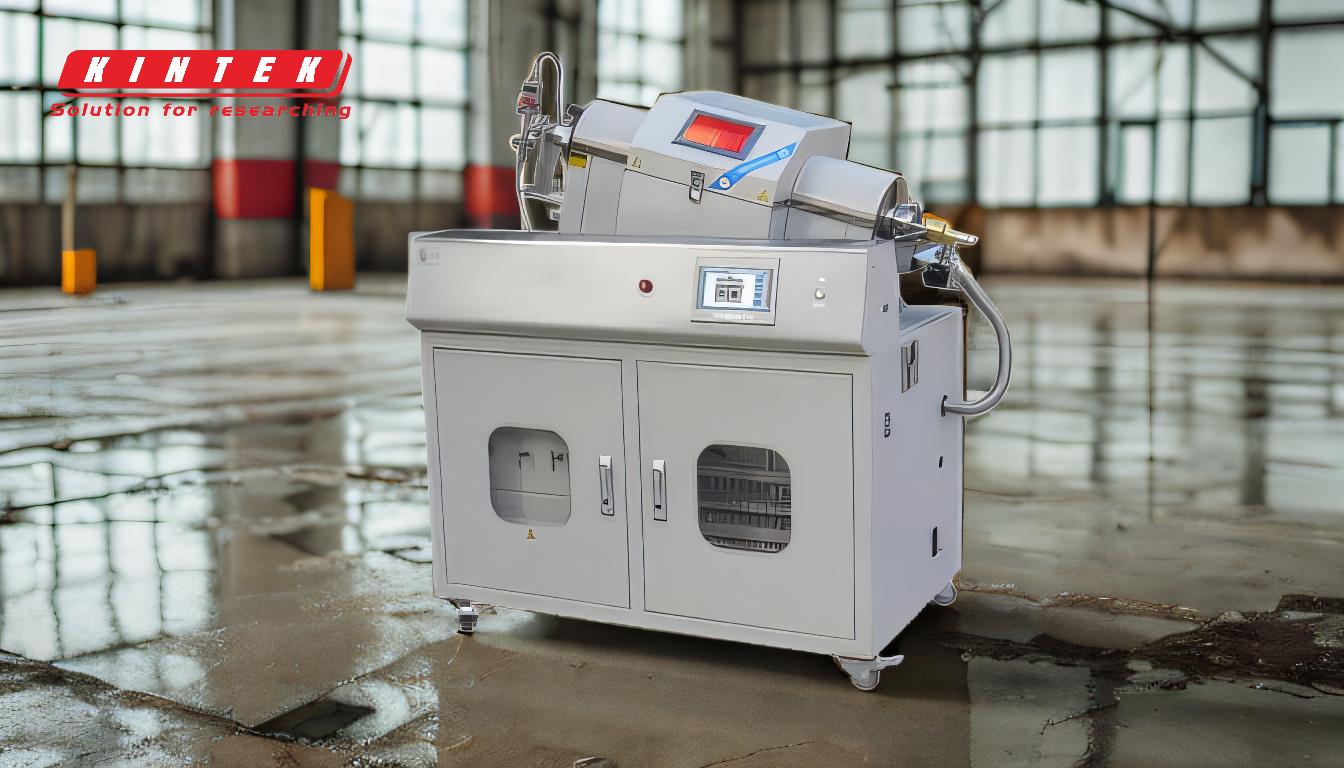
-
Definition and Purpose of CVD:
- CVD is a deposition method used to produce high-quality solid materials, particularly thin films, in semiconductor manufacturing.
- It involves chemical reactions between gaseous precursors and a substrate surface to form a solid film.
- The process is carried out under vacuum conditions to ensure precision and uniformity.
-
Key Steps in the CVD Process:
- Transport of Reacting Gases: Precursor chemicals are introduced into the CVD reactor and transported to the substrate surface through fluid transport and diffusion.
- Adsorption: The precursor molecules adhere to the substrate surface.
- Surface Reactions: Chemical reactions occur on the substrate surface, leading to the formation of the desired thin film.
- Nucleation and Growth: The film grows as more precursor molecules react and deposit on the surface.
- Desorption and Removal of By-products: Gaseous by-products are desorbed from the surface and removed from the reactor.
-
Types of Chemical Reactions in CVD:
- Decomposition: Precursor molecules decompose into atoms and molecules upon exposure to heat or other energy sources.
- Reaction with Other Gases: Precursors react with other gases or vapors near the substrate to form the desired film.
- Surface Catalysis: Reactions are often catalyzed by the substrate surface, enhancing film growth.
-
Advantages of CVD:
- High-Quality Films: Produces films with excellent electrical, thermal, and mechanical properties.
- Uniformity: Ensures uniform deposition, which is critical for semiconductor devices.
- Environmental Friendliness: Uses controlled chemical reactions, reducing waste and harmful by-products.
- Versatility: Can deposit a wide range of materials, including metals, ceramics, and polymers.
-
Challenges and Limitations:
- Cost and Complexity: Requires sophisticated equipment and controlled environments, making it expensive.
- Time-Consuming: The process can be slow, especially for large-scale production.
- Limited Scalability: Not always suitable for mass production due to the high cost and complexity.
-
Applications in Semiconductor Manufacturing:
- Thin Film Deposition: Used to deposit insulating, conducting, and semiconducting layers in integrated circuits.
- Coating of Substrates: Enhances the properties of substrates, such as improving conductivity or resistance.
- Production of Advanced Materials: Used to create materials with specific properties, such as graphene or carbon nanotubes.
-
Example of CVD in Action:
- Carbon Coating on LiFePO4: In a study by Tian et al., CVD was used to coat carbon on LiFePO4 by heating solid glucose in a quartz tube. The glucose decomposed into vapor, which condensed as small carbon clusters on the LiFePO4 surface. This process produced a uniform carbon layer, enhancing the material's rate capacity, cycling lifetime, and power density.
-
Future Prospects:
- Improved Efficiency: Research is ongoing to develop more efficient CVD processes that reduce production time and cost.
- New Materials: CVD is being explored for the deposition of novel materials, such as 2D materials and complex oxides.
- Scalability: Efforts are being made to adapt CVD for large-scale industrial applications without compromising quality.
In summary, CVD is a versatile and precise method for depositing thin films in semiconductor manufacturing. While it offers numerous advantages, including high-quality films and environmental friendliness, it also presents challenges related to cost, complexity, and scalability. Ongoing research aims to address these challenges, making CVD an even more valuable tool in the production of advanced materials.
Summary Table:
Aspect | Details |
---|---|
Definition | A method to deposit high-quality thin films using chemical reactions. |
Key Steps | Transport, Adsorption, Surface Reactions, Nucleation, Desorption. |
Advantages | High-quality films, uniformity, environmental friendliness, versatility. |
Challenges | Costly, time-consuming, limited scalability. |
Applications | Thin film deposition, substrate coating, advanced material production. |
Future Prospects | Improved efficiency, new materials, scalability for industrial use. |
Discover how CVD can revolutionize your semiconductor production—contact our experts today!