The heat treatment process is a controlled method of heating and cooling metals and other materials to alter their physical, mechanical, and sometimes chemical properties. It is widely used in industries to enhance characteristics such as hardness, strength, ductility, toughness, and resistance to wear. Common heat treatment processes include annealing, hardening, tempering, and case hardening, each serving specific purposes like softening metals, improving durability, or increasing surface hardness. These processes often involve precise temperature control and protective atmospheres, such as vacuum or inert gases, to prevent oxidation and achieve desired material properties. Heat treatment is essential in manufacturing to ensure materials meet the required performance standards for various applications.
Key Points Explained:
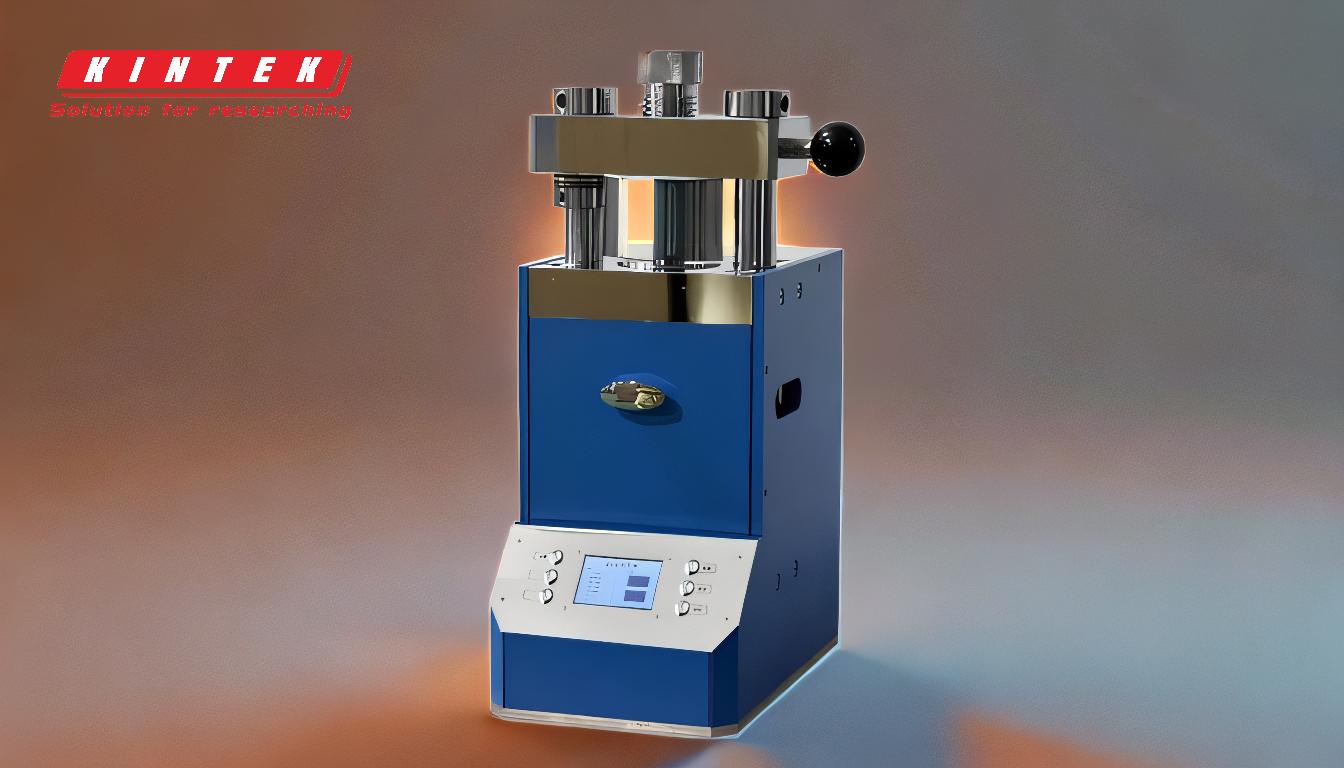
-
Definition and Purpose of Heat Treatment:
- Heat treatment is a group of industrial processes that involve heating and cooling materials, primarily metals, to achieve specific physical and mechanical properties.
- The primary goals include increasing hardness, improving strength, enhancing ductility, and achieving better wear resistance or toughness.
- It is applicable to both ferrous (e.g., steel) and non-ferrous metals (e.g., aluminum, copper) and is also used in materials like glass.
-
Common Heat Treatment Processes:
- Annealing: A process that involves heating a material to a specific temperature and then slowly cooling it to soften the metal, improve ductility, and reduce internal stresses.
- Hardening: Involves heating the metal to a high temperature and then rapidly cooling it (quenching) to increase hardness and strength.
- Tempering: Follows hardening and involves reheating the metal to a lower temperature to reduce brittleness and improve toughness.
- Case Hardening: A surface treatment that hardens the outer layer of the metal while maintaining a softer, more ductile core. Techniques include carburizing, nitriding, and carbonitriding.
- Brazing: A joining process that uses a filler metal to bond two or more metals at high temperatures in a controlled atmosphere.
- Sintering: A process used in powder metallurgy where metal powders are heated to just below their melting point to form a solid mass.
-
Controlled Atmospheres in Heat Treatment:
- Heat treatment often requires protective atmospheres, such as vacuum, hydrogen, nitrogen, or argon, to prevent oxidation and surface contamination.
- Vacuum Heat Treatment: Uses a vacuum-sealed furnace to create an oxygen-free environment, resulting in a cleaner, more durable finish.
- Bright Annealing: Minimizes oxidation by using pure hydrogen, nitrogen, or argon atmospheres, producing a bright, clean surface.
-
Applications and Benefits:
- Heat treatment is essential in industries like automotive, aerospace, construction, and tool manufacturing to enhance material performance.
- It improves the versatility, durability, and longevity of metals, making them suitable for demanding applications.
- Specific benefits include increased wear resistance, improved machinability, and enhanced mechanical properties.
-
Factors Affecting Heat Treatment:
- Temperature: Precise control of heating and cooling temperatures is critical to achieving the desired material properties.
- Cooling Rate: The speed at which the material is cooled (e.g., quenching vs. slow cooling) significantly impacts the final properties.
- Atmosphere: The environment during heat treatment (e.g., vacuum, inert gas) affects surface quality and prevents oxidation.
-
Importance in Manufacturing:
- Heat treatment is a cornerstone of modern manufacturing, enabling the production of high-performance components.
- It allows manufacturers to tailor material properties to specific applications, ensuring reliability and efficiency in end-use products.
By understanding these key points, equipment and consumable purchasers can make informed decisions about the heat treatment processes and materials best suited for their needs.
Summary Table:
Aspect | Details |
---|---|
Purpose | Alters physical, mechanical, and chemical properties of metals and materials. |
Common Processes | Annealing, hardening, tempering, case hardening, brazing, sintering. |
Controlled Atmospheres | Vacuum, hydrogen, nitrogen, argon to prevent oxidation. |
Applications | Automotive, aerospace, construction, tool manufacturing. |
Key Benefits | Increased hardness, strength, wear resistance, and durability. |
Critical Factors | Temperature, cooling rate, and atmosphere control. |
Optimize your material performance with the right heat treatment process—contact our experts today!