Isostatic presses are versatile tools used across various industries for consolidating powders, healing defects in castings, and enhancing material properties. They are employed in pharmaceuticals, explosives, chemicals, food, nuclear fuel, ceramics, metals, composites, plastics, and carbon. The technology is also increasingly used in additive manufacturing to improve dimensional accuracy and reduce residual stresses. Isostatic presses come in two main types: cold isostatic presses (CIP) and hot isostatic presses (HIP). CIP operates at room temperature and is used in applications like solid-state battery production, while HIP is used for densification, diffusion bonding, and powder metallurgy. The process is particularly valuable for producing high-performance ceramics and new alloy products that are challenging to manufacture using traditional methods.
Key Points Explained:
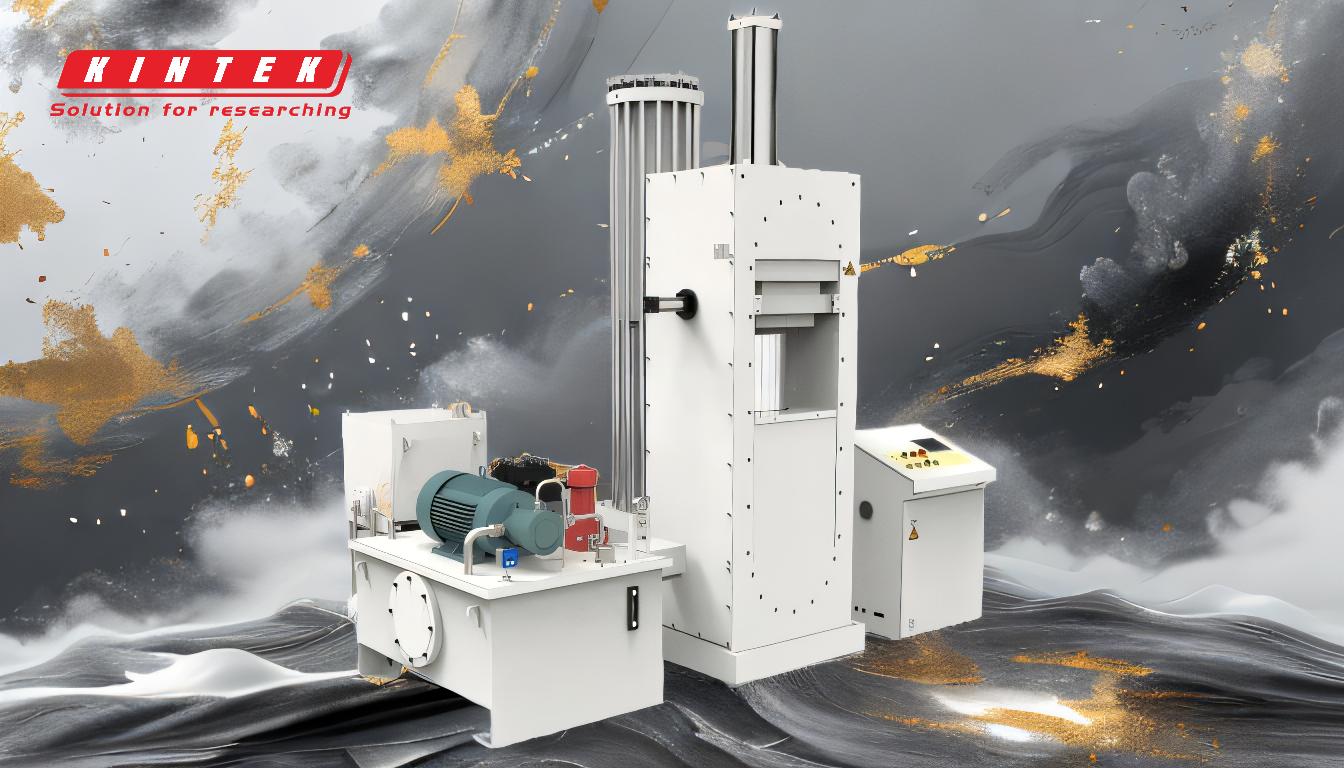
-
Applications Across Industries:
- Isostatic presses are used in a wide range of industries, including pharmaceuticals, explosives, chemicals, food, and nuclear fuel. They are also essential in industries dealing with ceramics, metals, composites, plastics, and carbon.
- In additive manufacturing, isostatic pressing is used as a post-processing technique to ensure dimensional accuracy and stability, reducing or eliminating residual stresses or distortions.
-
Types of Isostatic Presses:
-
Cold Isostatic Presses (CIP):
- Operate at room temperature and use liquid as the pressure medium with rubber or plastic sheathing molds.
- Can apply higher pressures (100-630MPa) and are widely used in solid-state battery production, such as preparing garnet-based ultra-thin flexible composite solid electrolyte membranes and Li6.34l0.15La3Zr1.75Ta0.25012 solid electrolyte.
- Also used in patents for preparing negative electrode-free all-solid-state batteries.
-
Hot Isostatic Presses (HIP):
- Used for densification, diffusion bonding, and powder metallurgy products. These applications are chosen based on the needs of the products being processed.
-
Cold Isostatic Presses (CIP):
-
Material Consolidation and Defect Healing:
- Isostatic pressing is used for the consolidation of powders or defect healing of castings. This process is applied to a range of materials, including ceramics, metals, composites, plastics, and carbon.
- The uniform pressure applied during isostatic pressing helps in achieving consistent material properties and high-performance products.
-
Production of High-Performance Materials:
- Isostatic pressing technology is used to produce new alloy products that are difficult to manufacture using traditional casting technology.
- It is an excellent forming process for high-performance zirconia and alumina ceramic products that require high strength and durability.
-
Advantages in Additive Manufacturing:
- In additive manufacturing, isostatic pressing helps in achieving dimensional accuracy and stability for parts. This ensures that the parts meet required specifications and maintain consistent material properties.
- The process reduces or eliminates residual stresses or distortions, which is crucial for the performance and reliability of additive manufactured parts.
By understanding these key points, equipment and consumable purchasers can better appreciate the versatility and importance of isostatic press technology in various industrial applications.
Summary Table:
Aspect | Details |
---|---|
Applications | Pharmaceuticals, explosives, chemicals, food, nuclear fuel, ceramics, etc. |
Types | Cold Isostatic Presses (CIP), Hot Isostatic Presses (HIP) |
CIP Uses | Solid-state battery production, high-pressure applications |
HIP Uses | Densification, diffusion bonding, powder metallurgy |
Key Benefits | Material consolidation, defect healing, high-performance material production |
Additive Manufacturing Role | Improves dimensional accuracy, reduces residual stresses |
Learn how isostatic presses can optimize your production process—contact us today for expert advice!