Quenching heat treatment on aluminum is a critical process used to enhance the material's mechanical properties, such as strength and hardness, by rapidly cooling it from a high temperature. This process is essential in industries like aerospace and automotive, where aluminum components require specific performance characteristics. Unlike steel, aluminum does not undergo a martensitic transformation, but quenching still plays a vital role in achieving desired material properties. Below, we explore the key aspects of quenching heat treatment on aluminum, its purpose, and its applications.
Key Points Explained:
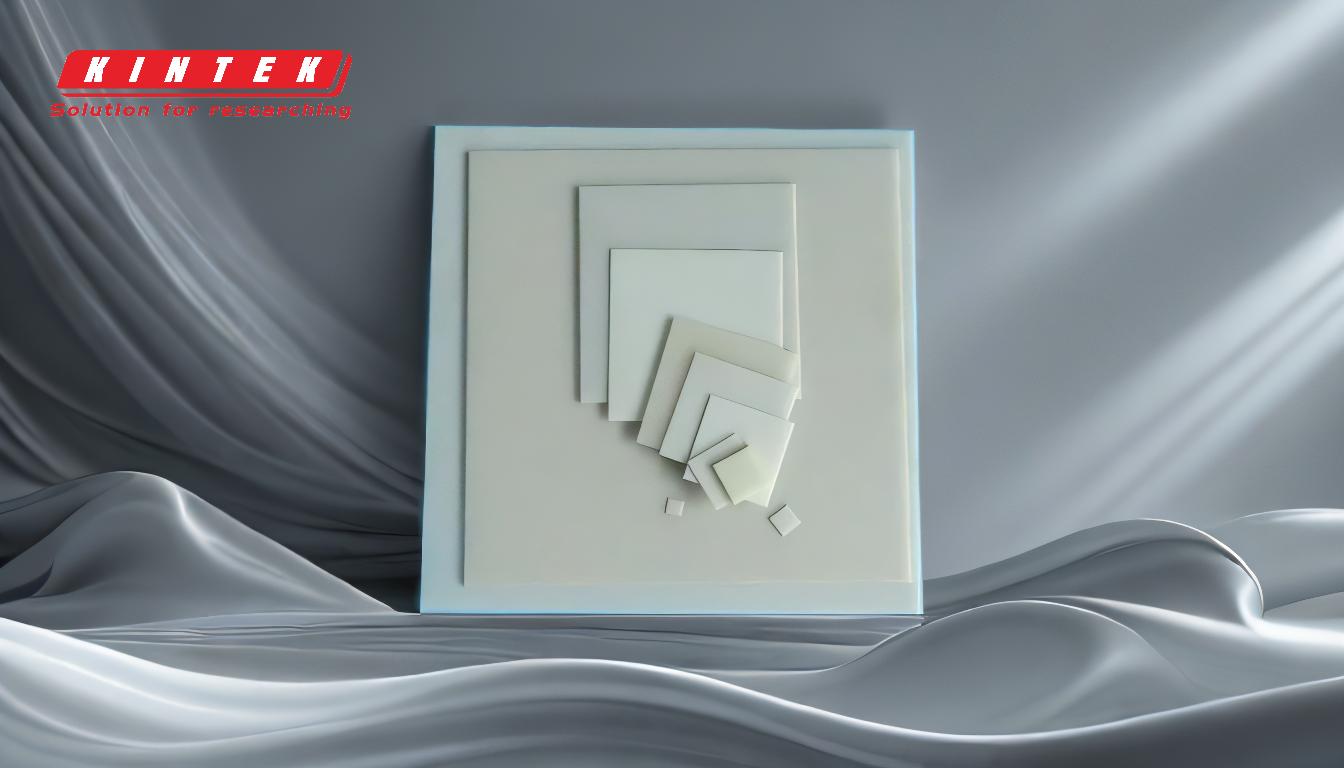
-
What is Quenching Heat Treatment?
- Quenching is a heat treatment process that involves heating a metal to a specific temperature and then rapidly cooling it to lock in a desired microstructure. For aluminum, this process is typically performed after solution heat treatment, where the material is heated to dissolve alloying elements into a solid solution.
- Rapid cooling prevents the alloying elements from precipitating out of the solution, which helps achieve a uniform and stable microstructure.
-
Purpose of Quenching in Aluminum Heat Treatment
- Enhancing Mechanical Properties: Quenching helps improve the strength, hardness, and wear resistance of aluminum alloys by maintaining a supersaturated solid solution of alloying elements.
- Preventing Precipitation: Rapid cooling prevents the formation of coarse precipitates, which can weaken the material.
- Preparing for Aging: Quenching is often followed by an aging process (natural or artificial), where the material is reheated to allow controlled precipitation of strengthening phases.
-
Quenching Mediums for Aluminum
- Water: The most common quenching medium for aluminum due to its high cooling rate. However, it can cause distortion or cracking if not controlled properly.
- Polymer Solutions: These provide a more controlled cooling rate, reducing the risk of distortion while still achieving the desired properties.
- Air: Used for thicker sections or alloys that are less sensitive to cooling rates.
-
Steps in the Quenching Process for Aluminum
- Heating: The aluminum is heated to a temperature just below its melting point (typically between 450°C and 550°C) to dissolve alloying elements.
- Soaking: The material is held at this temperature to ensure uniform heating and complete dissolution of alloying elements.
- Quenching: The aluminum is rapidly cooled using a suitable medium to lock in the solid solution.
- Aging: After quenching, the material may undergo natural aging (at room temperature) or artificial aging (at elevated temperatures) to achieve the desired mechanical properties.
-
Applications of Quenched Aluminum
- Aerospace: Aluminum alloys are widely used in aircraft components due to their high strength-to-weight ratio, which is achieved through quenching and aging.
- Automotive: Quenched aluminum is used in engine components, wheels, and structural parts to improve performance and reduce weight.
- Consumer Electronics: Aluminum alloys are used in casings and frames for devices, where strength and durability are essential.
-
Challenges in Aluminum Quenching
- Distortion and Warping: Rapid cooling can cause dimensional changes, especially in complex shapes.
- Residual Stresses: Quenching can introduce internal stresses, which may require additional stress-relief treatments.
- Cooling Rate Control: Achieving the right cooling rate is critical to avoid defects like cracking or incomplete hardening.
-
Comparison with Steel Quenching
- Unlike steel, aluminum does not form martensite during quenching. Instead, the goal is to maintain a supersaturated solid solution that can be further strengthened through aging.
- Aluminum quenching typically involves lower temperatures and different cooling mediums compared to steel.
By understanding the quenching heat treatment process for aluminum, manufacturers can optimize the material's properties for specific applications. This process is a cornerstone of modern metallurgy, enabling the production of lightweight, high-performance components across various industries.
Summary Table:
Key Aspect | Details |
---|---|
Purpose | Enhances strength, hardness, and wear resistance; prevents coarse precipitates. |
Quenching Mediums | Water (most common), polymer solutions, air. |
Steps | Heating, soaking, quenching, aging. |
Applications | Aerospace, automotive, consumer electronics. |
Challenges | Distortion, residual stresses, cooling rate control. |
Comparison with Steel | No martensite formation; lower temperatures and different cooling mediums. |
Optimize your aluminum components with expert heat treatment solutions—contact us today!