When brazing stainless steel, the choice of the best stainless steel grade depends on the application, the brazing method, and the filler metal used. The process involves careful selection of materials, thorough cleaning, and precise control of temperature and atmosphere to ensure strong, corrosion-resistant joints. The main considerations include the compatibility of the filler metal with the stainless steel, the brazing environment (air, reducing atmosphere, or vacuum), and the heating method (flame, induction, or furnace). Commonly used filler metals include silver-based, copper-based, nickel-based, and precious metal alloys, each suited for specific conditions and requirements.
Key Points Explained:
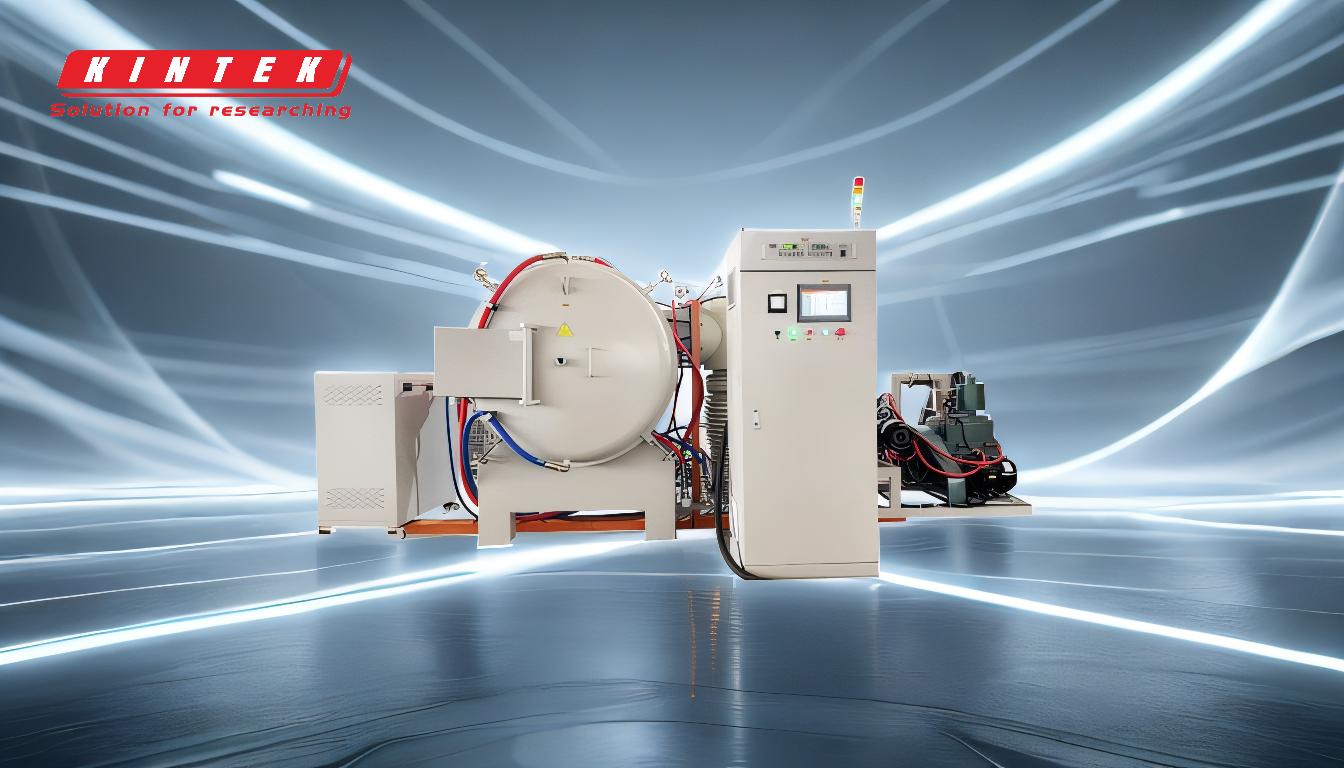
-
Importance of Stainless Steel Composition:
- Stainless steel contains chromium, which forms chromium oxide on the surface. This oxide layer can interfere with brazing, so it must be managed during the process.
- The choice of stainless steel grade (e.g., 304, 316) depends on the application's corrosion resistance and mechanical strength requirements. For example, 316 stainless steel is often preferred for its superior corrosion resistance.
-
Role of the Brazing Atmosphere:
- Dry Hydrogen: Used to reduce chromium oxide during brazing, especially in high-temperature applications. The effectiveness depends on the dew point and temperature.
- Reducing Atmosphere: Helps prevent oxidation and ensures a clean surface for brazing.
- Vacuum Brazing: Eliminates the need for flux and provides a clean environment, ideal for high-precision applications.
-
Filler Metal Selection:
- Silver-Based Filler Metals: Commonly used for their good flow characteristics and compatibility with stainless steel. They are suitable for low to medium-temperature brazing.
- Copper-Based Filler Metals: Ideal for high-temperature applications and provide strong joints.
- Nickel-Based Filler Metals: Excellent for high-temperature and corrosive environments, often used in aerospace and chemical industries.
- Precious Metal Filler Metals: Used in specialized applications requiring high corrosion resistance and strength.
-
Cleaning and Surface Preparation:
- Strict cleaning is essential to remove grease, oil, and other contaminants that can interfere with brazing.
- Immediate brazing after cleaning prevents recontamination of the surface.
-
Brazing Methods:
- Flame Brazing: Suitable for small-scale or manual operations but requires careful control of heat input.
- Induction Brazing: Provides localized heating, ideal for precision work.
- Furnace Brazing: Ensures uniform heating and is suitable for mass production.
-
Temperature Control:
- The filler metal's liquidus temperature should be at least 30°C lower than the stainless steel's solidus temperature to prevent melting of the base material.
- A smaller temperature difference between the solidus and liquidus of the filler metal requires precise furnace temperature control.
-
Chemical Stability and Compatibility:
- The filler metal should exhibit high chemical stability at brazing temperatures, with low oxidation and vapor pressure.
- The main components of the filler metal should be close to those of the stainless steel in the periodic table to ensure good corrosion resistance of the brazed joint.
By considering these factors, the best stainless steel for brazing can be selected based on the specific requirements of the application, ensuring strong, durable, and corrosion-resistant joints.
Summary Table:
Factor | Details |
---|---|
Stainless Steel Grade | 304 or 316, depending on corrosion resistance and mechanical strength needs |
Brazing Atmosphere | Dry hydrogen, reducing atmosphere, or vacuum for clean, precise brazing |
Filler Metals | Silver-based, copper-based, nickel-based, or precious metal alloys |
Cleaning | Essential to remove contaminants for strong joints |
Brazing Methods | Flame, induction, or furnace brazing for varying applications |
Temperature Control | Precise control to prevent base material melting |
Chemical Compatibility | Filler metal should match stainless steel's corrosion resistance |
Need help selecting the right stainless steel for brazing? Contact our experts today for tailored solutions!