The correct brazing temperature depends on several factors, including the materials being joined, the type of filler metal used, and the specific application requirements. Generally, brazing temperatures range from 450°C to 900°C, but the optimal temperature must be carefully selected to ensure proper joint formation without damaging the base materials. Factors such as thermal expansion, metallurgical compatibility, and the need for post-brazing heat treatment also play a role in determining the ideal temperature. For specialized equipment like a rotating furnace, the temperature must be precisely controlled to achieve uniform heating and consistent results.
Key Points Explained:
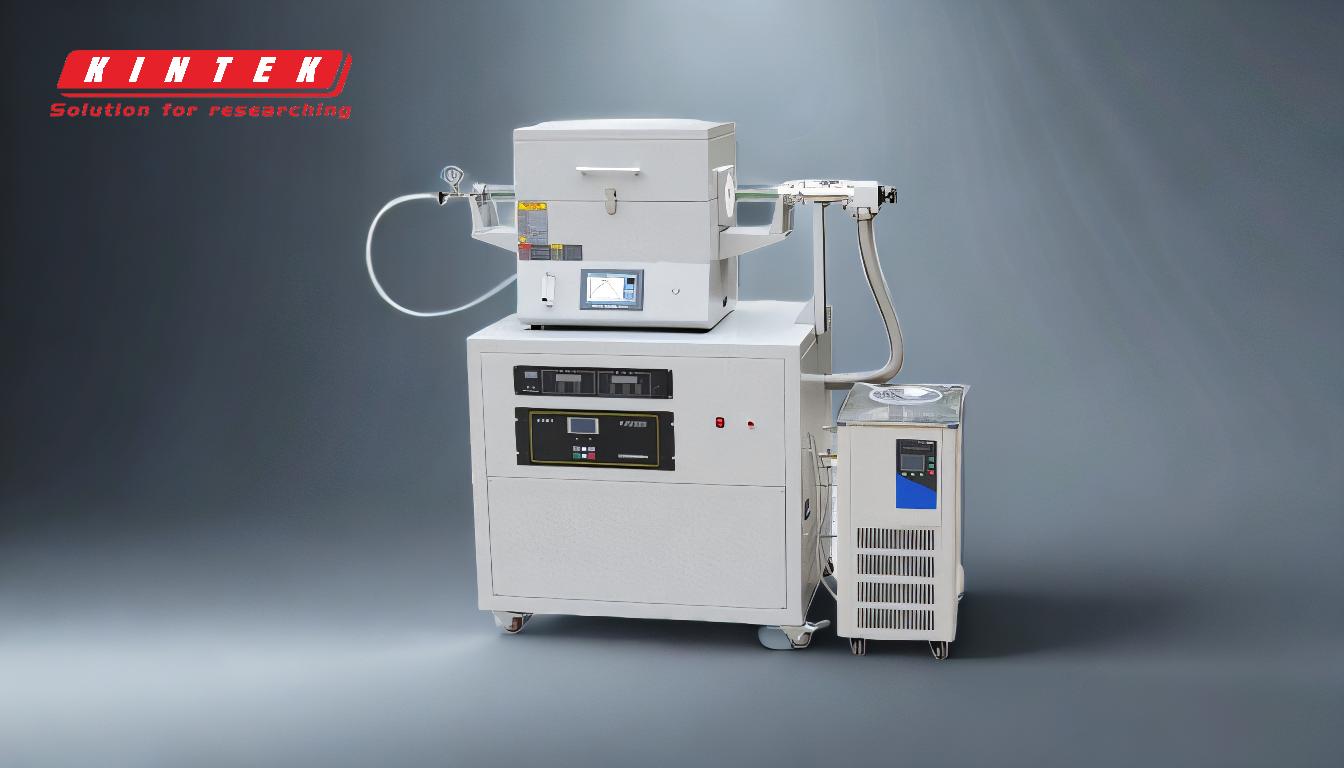
-
Definition of Brazing Temperature:
- Brazing temperature refers to the range at which the filler metal melts and flows into the joint, creating a strong bond between the base materials. This temperature is typically below the melting point of the base metals but above the melting point of the filler metal.
-
Typical Brazing Temperature Range:
- The brazing temperature usually falls between 450°C and 900°C, depending on the materials involved. For example:
- Aluminum alloys: 580°C to 620°C.
- Copper and copper alloys: 600°C to 850°C.
- Stainless steel: 800°C to 900°C.
- The brazing temperature usually falls between 450°C and 900°C, depending on the materials involved. For example:
-
Factors Influencing Brazing Temperature:
- Base Material Properties: The thermal conductivity, melting point, and thermal expansion of the base materials must be considered.
- Filler Metal Composition: Different filler metals (e.g., silver-based, copper-based, or nickel-based) have varying melting points and flow characteristics.
- Joint Design: The geometry and clearance of the joint affect how the filler metal flows and bonds.
- Application Requirements: Some applications may require specific temperatures to achieve desired mechanical or thermal properties.
-
Importance of Temperature Control:
- Precise temperature control is critical to avoid overheating, which can weaken the base materials, or underheating, which may result in incomplete bonding. Equipment like a rotating furnace ensures uniform heating, which is especially important for complex or large components.
-
Special Considerations for Rotating Furnaces:
- Rotating furnaces are designed to provide consistent heat distribution, making them ideal for brazing applications. The rotation ensures that all parts of the workpiece are exposed to the same temperature, reducing the risk of uneven heating and improving joint quality.
-
Post-Brazing Heat Treatment:
- In some cases, post-brazing heat treatment may be necessary to relieve stresses or enhance the mechanical properties of the joint. The temperature and duration of this treatment must align with the brazing process to avoid compromising the joint integrity.
-
Practical Tips for Determining Brazing Temperature:
- Refer to material datasheets and filler metal specifications for recommended temperature ranges.
- Conduct trial runs to test the temperature settings and adjust as needed.
- Use temperature measurement tools, such as thermocouples or infrared thermometers, to monitor the process in real-time.
By understanding these factors and leveraging specialized equipment like a rotating furnace, you can achieve optimal brazing results tailored to your specific application.
Summary Table:
Material | Brazing Temperature Range |
---|---|
Aluminum Alloys | 580°C to 620°C |
Copper & Copper Alloys | 600°C to 850°C |
Stainless Steel | 800°C to 900°C |
Need help selecting the right brazing temperature for your project? Contact our experts today!