The degree of calcination refers to the extent to which calcium carbonate (CaCO₃) has been thermally decomposed into free lime (CaO) and carbon dioxide (CO₂) during the calcination process. When the calcination process is complete, it is referred to as the "degree of true calcination," meaning that all CaCO₃ has been fully dissociated. This process typically occurs at high temperatures, often above 800°C, and is critical in industries such as cement production, lime manufacturing, and metallurgy. The degree of calcination is a key indicator of the efficiency and completeness of the thermal decomposition process.
Key Points Explained:
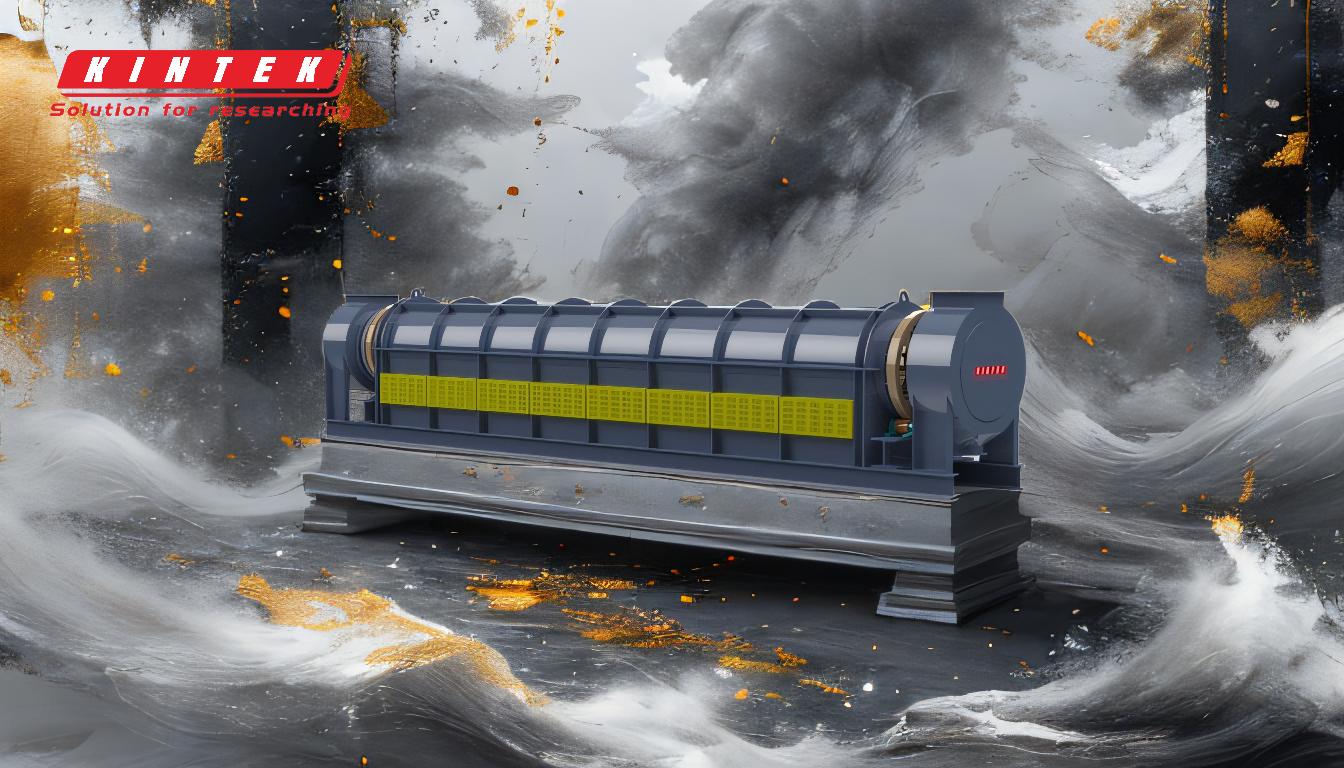
-
Definition of Calcination
Calcination is a thermal treatment process applied to ores and other solid materials to bring about thermal decomposition, phase transition, or the removal of volatile components. In the context of calcium carbonate, calcination involves heating CaCO₃ to produce CaO and CO₂. The degree of calcination measures how much of the CaCO₃ has been converted into CaO. -
Chemical Reaction of Calcination
The chemical reaction for the calcination of calcium carbonate is:
[ \text{CaCO}_3 \xrightarrow{\text{heat}} \text{CaO} + \text{CO}_2 ]
This reaction is endothermic, meaning it requires heat to proceed. The degree of calcination is directly related to the completeness of this reaction. -
Degree of True Calcination
The degree of true calcination is achieved when 100% of the CaCO₃ has been converted into CaO and CO₂. This is the ideal state for many industrial processes, as it ensures maximum yield of the desired product (CaO) and minimizes residual CaCO₃. -
Factors Influencing the Degree of Calcination
- Temperature: Higher temperatures generally increase the rate and completeness of calcination. However, excessively high temperatures can lead to sintering or other undesirable effects.
- Time: Longer calcination times allow for more complete dissociation of CaCO₃.
- Particle Size: Smaller particles calcine more quickly and completely due to their larger surface area.
- Atmosphere: The presence of CO₂ in the surrounding atmosphere can inhibit calcination, as it shifts the equilibrium back toward CaCO₃ formation.
-
Measurement of Calcination Degree
The degree of calcination can be measured using techniques such as:- Thermogravimetric Analysis (TGA): Measures weight loss as CO₂ is released during calcination.
- X-ray Diffraction (XRD): Identifies the presence of CaO and residual CaCO₃.
- Chemical Titration: Determines the amount of free lime (CaO) present.
-
Industrial Applications
The degree of calcination is critical in industries such as:- Cement Production: Calcination of limestone is a key step in producing clinker, the precursor to cement.
- Lime Manufacturing: High-purity lime (CaO) is produced through complete calcination.
- Metallurgy: Calcination is used to prepare ores for further processing.
-
Importance of Complete Calcination
Incomplete calcination can lead to:- Reduced product quality due to residual CaCO₃.
- Increased energy consumption, as additional heat is required to complete the reaction.
- Environmental concerns, as unreacted CaCO₃ can release CO₂ during later stages of processing.
By understanding and optimizing the degree of calcination, industries can improve process efficiency, product quality, and environmental sustainability.
Summary Table:
Aspect | Details |
---|---|
Definition | Extent of CaCO₃ decomposition into CaO and CO₂ during calcination. |
True Calcination | 100% conversion of CaCO₃ into CaO and CO₂. |
Key Factors | Temperature, time, particle size, and atmosphere. |
Measurement Techniques | TGA, XRD, and chemical titration. |
Industrial Applications | Cement production, lime manufacturing, and metallurgy. |
Importance | Ensures product quality, energy efficiency, and environmental sustainability. |
Optimize your calcination process today—contact our experts for tailored solutions!