Spark Plasma Sintering (SPS) and conventional sintering are two distinct methods used to densify powdered materials into solid forms, but they differ significantly in their mechanisms, efficiency, and outcomes. SPS utilizes a pulsed direct current to generate plasma and heat the material internally, allowing for rapid heating rates, shorter processing times, and finer microstructures. In contrast, conventional sintering relies on external heating, often requiring longer durations and higher temperatures to achieve similar results. SPS also integrates pressure, which helps break oxide layers on powder surfaces and enhances densification. This method is particularly advantageous for creating materials with unique properties, as it operates at lower temperatures and pressures compared to traditional techniques.
Key Points Explained:
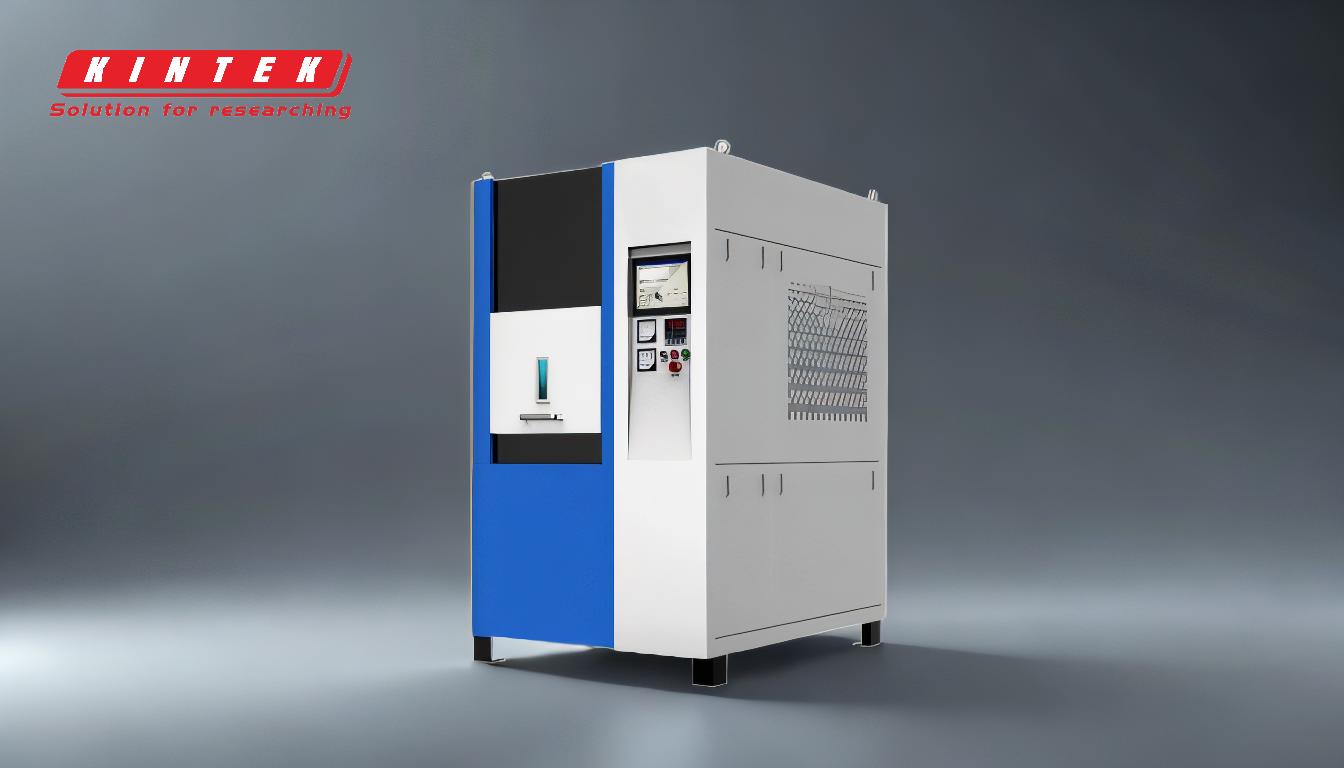
-
Mechanism of Heating:
- Conventional Sintering: Uses external heating sources, such as furnaces, to gradually raise the temperature of the material. This process is slower and relies on heat transfer from the outside to the inside of the material.
- Spark Plasma Sintering (SPS): Employs an ON-OFF DC pulse current to generate plasma and heat the material internally. This internal heating allows for faster and more uniform temperature distribution, significantly reducing processing time.
-
Processing Time:
- Conventional Sintering: Can take hours or even days to complete, depending on the material and desired density. The slow heating rates are necessary to avoid thermal stresses and ensure uniform densification.
- Spark Plasma Sintering (SPS): Typically completes in just a few minutes due to its high heating rates. This rapid processing is achieved through the direct application of electrical energy to the powder particles.
-
Temperature and Pressure Requirements:
- Conventional Sintering: Often requires higher temperatures and, in some cases, additional pressure to achieve densification. The process may also involve longer dwell times at elevated temperatures.
- Spark Plasma Sintering (SPS): Operates at lower temperatures and lower mould pressures compared to conventional methods. The integration of pressure during sintering helps break oxide films on powder surfaces, enhancing densification.
-
Microstructure and Material Properties:
- Conventional Sintering: May result in larger grain sizes and less uniform microstructures due to slower heating rates and longer exposure to high temperatures. This can affect the mechanical properties of the final product.
- Spark Plasma Sintering (SPS): Produces finer and more homogeneous microstructures, leading to materials with improved mechanical and thermal properties. The rapid heating and cooling rates prevent excessive grain growth, resulting in superior material characteristics.
-
Applications and Material Suitability:
- Conventional Sintering: Suitable for a wide range of materials but may not be ideal for materials that require precise control over microstructure or those that degrade at high temperatures.
- Spark Plasma Sintering (SPS): Particularly advantageous for advanced materials, such as ceramics, composites, and nanomaterials, where fine microstructures and unique properties are desired. It also allows for the sintering of materials that are difficult to process using conventional methods.
-
Energy Efficiency:
- Conventional Sintering: Generally less energy-efficient due to longer processing times and higher energy consumption.
- Spark Plasma Sintering (SPS): More energy-efficient as it reduces both the time and temperature required for sintering, leading to lower overall energy consumption.
In summary, Spark Plasma Sintering offers significant advantages over conventional sintering, including faster processing times, lower temperature and pressure requirements, and the ability to produce materials with superior microstructures and properties. These benefits make SPS a preferred method for advanced material fabrication, particularly in applications where precision and performance are critical.
Summary Table:
Aspect | Conventional Sintering | Spark Plasma Sintering (SPS) |
---|---|---|
Heating Mechanism | External heating sources (e.g., furnaces); slower heat transfer | Internal heating via pulsed DC current; rapid and uniform heating |
Processing Time | Hours to days, depending on material and density | Minutes due to high heating rates |
Temperature & Pressure | Higher temperatures and pressures required | Lower temperatures and mould pressures |
Microstructure | Larger grain sizes, less uniform | Finer, more homogeneous microstructures |
Applications | Suitable for a wide range of materials | Ideal for advanced materials (ceramics, composites, nanomaterials) |
Energy Efficiency | Less energy-efficient due to longer processing times | More energy-efficient; reduces time and temperature requirements |
Ready to explore how Spark Plasma Sintering can revolutionize your material fabrication? Contact our experts today!