The cooling rate in heat treatment significantly influences the microstructure and mechanical properties of metals and alloys. Rapid cooling, such as quenching, typically results in a harder and more brittle material due to the formation of martensite or other metastable phases. Slower cooling rates, like annealing, allow for the formation of softer and more ductile structures, such as pearlite or ferrite, as atoms have more time to diffuse and form equilibrium phases. The cooling rate also affects residual stresses, distortion, and the likelihood of cracking. Selecting the appropriate cooling rate is crucial to achieving the desired balance of hardness, strength, toughness, and ductility in the final product.
Key Points Explained:
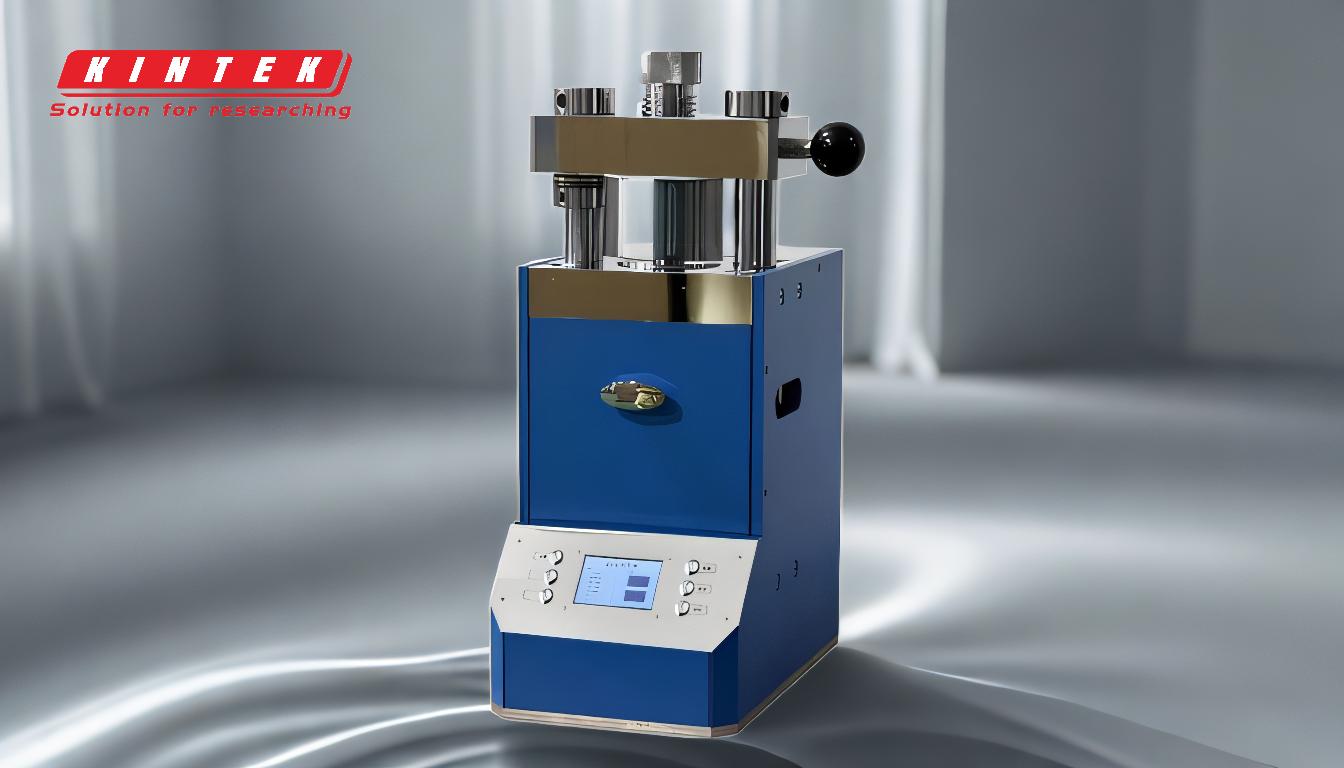
-
Microstructure Formation:
-
Rapid Cooling (Quenching):
- Forms martensite, a hard and brittle phase, due to suppressed diffusion.
- Prevents the formation of equilibrium phases like pearlite or ferrite.
- Results in a fine-grained structure with high hardness but low ductility.
-
Slow Cooling (Annealing):
- Allows atoms to diffuse and form equilibrium phases like pearlite or ferrite.
- Produces a coarser-grained structure with improved ductility and toughness but reduced hardness.
-
Rapid Cooling (Quenching):
-
Mechanical Properties:
-
Hardness and Strength:
- Rapid cooling increases hardness and strength due to the formation of martensite.
- Slow cooling reduces hardness but improves ductility and toughness.
-
Ductility and Toughness:
- Slow cooling enhances ductility and toughness by allowing the formation of softer phases.
- Rapid cooling reduces ductility, making the material more brittle.
-
Hardness and Strength:
-
Residual Stresses and Distortion:
-
Rapid Cooling:
- Generates high residual stresses due to uneven cooling and phase transformations.
- Increases the risk of distortion and cracking.
-
Slow Cooling:
- Minimizes residual stresses and distortion by allowing uniform cooling.
- Reduces the likelihood of cracking.
-
Rapid Cooling:
-
Phase Transformations:
-
Rapid Cooling:
- Suppresses diffusion, leading to non-equilibrium phases like martensite.
- Can result in retained austenite, which may affect mechanical properties.
-
Slow Cooling:
- Promotes diffusion, allowing the formation of equilibrium phases.
- Ensures a more stable and predictable microstructure.
-
Rapid Cooling:
-
Application-Specific Considerations:
-
High-Strength Applications:
- Rapid cooling is preferred for components requiring high hardness and wear resistance, such as gears and cutting tools.
-
Ductility and Formability:
- Slow cooling is suitable for components requiring good ductility and formability, such as structural parts and sheets.
-
High-Strength Applications:
-
Cooling Mediums and Techniques:
-
Quenching Media:
- Water, oil, and air are common quenching mediums, each providing different cooling rates.
- Water provides the fastest cooling, while air provides the slowest.
-
Controlled Cooling:
- Techniques like interrupted quenching or tempering can be used to achieve specific properties by controlling the cooling rate.
-
Quenching Media:
-
Thermal and Mechanical Stability:
-
Rapid Cooling:
- May lead to instability in mechanical properties over time due to retained stresses and metastable phases.
-
Slow Cooling:
- Provides more stable mechanical properties and reduces the risk of property changes over time.
-
Rapid Cooling:
-
Material-Specific Effects:
-
Steels:
- Cooling rate significantly affects the transformation of austenite to various phases like martensite, bainite, pearlite, or ferrite.
-
Non-Ferrous Alloys:
- Cooling rate can influence precipitation hardening and grain size in alloys like aluminum and titanium.
-
Steels:
By understanding the effects of cooling rate, manufacturers can tailor heat treatment processes to achieve the desired balance of properties for specific applications, ensuring optimal performance and longevity of the material.
Summary Table:
Aspect | Rapid Cooling (Quenching) | Slow Cooling (Annealing) |
---|---|---|
Microstructure | Forms martensite (hard, brittle) | Forms pearlite/ferrite (soft, ductile) |
Hardness & Strength | High hardness and strength | Reduced hardness, improved ductility and toughness |
Ductility & Toughness | Low ductility, brittle | High ductility and toughness |
Residual Stresses | High residual stresses, risk of distortion and cracking | Minimal residual stresses, reduced risk of cracking |
Phase Transformations | Non-equilibrium phases (e.g., martensite) | Equilibrium phases (e.g., pearlite, ferrite) |
Applications | High-strength parts (gears, cutting tools) | Ductile parts (structural components, sheets) |
Need help optimizing your heat treatment process? Contact our experts today for tailored solutions!