The floating catalyst method is a chemical vapor deposition (CVD) technique used to synthesize carbon nanotubes (CNTs) and other nanomaterials. In this process, a catalyst precursor is introduced into a high-temperature reactor in a gaseous or vapor form, where it decomposes to form metal catalyst nanoparticles. These nanoparticles act as nucleation sites for the growth of carbon nanotubes or other nanostructures. The method is characterized by its ability to produce high-quality, continuous, and scalable nanomaterials. It is widely used in research and industrial applications due to its efficiency and versatility in controlling the properties of the synthesized materials.
Key Points Explained:
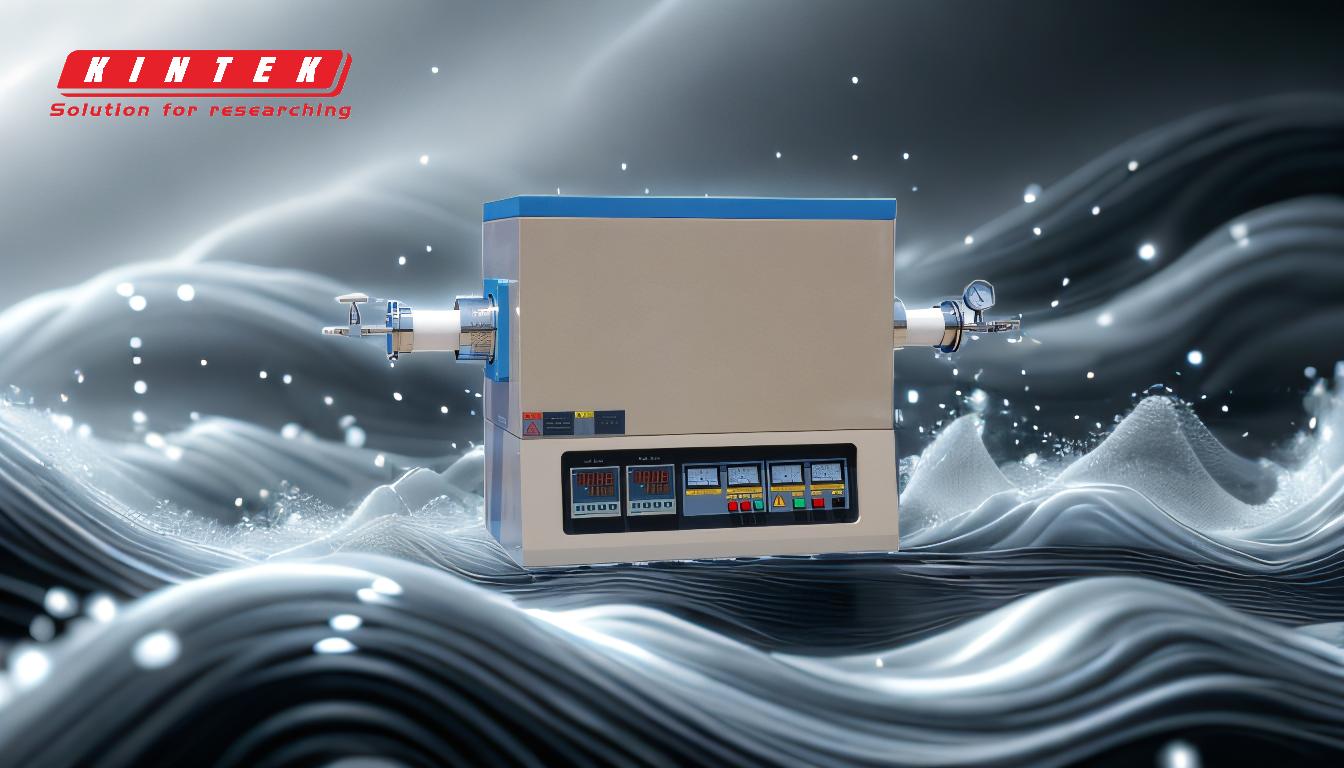
-
Definition and Overview of the Floating Catalyst Method:
- The floating catalyst method is a type of chemical vapor deposition (CVD) process.
- It involves the introduction of a catalyst precursor in a gaseous or vapor form into a high-temperature reactor.
- The catalyst precursor decomposes at high temperatures to form metal nanoparticles, which serve as nucleation sites for nanomaterial growth.
-
Mechanism of the Process:
- The catalyst precursor, often a volatile metal compound (e.g., ferrocene), is vaporized and carried into the reactor by a carrier gas.
- Inside the reactor, the precursor decomposes at elevated temperatures (typically 600–1200°C) to release metal atoms.
- These metal atoms aggregate to form nanoparticles, which float in the gas stream and catalyze the growth of carbon nanotubes or other nanostructures.
-
Advantages of the Floating Catalyst Method:
- Scalability: The method is suitable for large-scale production of nanomaterials due to its continuous nature.
- High-Quality Output: It produces high-purity and well-aligned carbon nanotubes with fewer defects.
- Versatility: It can be adapted to synthesize various types of nanostructures by adjusting parameters such as temperature, gas flow rate, and catalyst concentration.
-
Applications of the Floating Catalyst Method:
- Carbon Nanotube Production: Widely used for synthesizing single-walled and multi-walled carbon nanotubes.
- Nanocomposites: The synthesized nanomaterials can be integrated into polymers, metals, or ceramics to enhance their mechanical, electrical, or thermal properties.
- Energy Storage: Used in the development of electrodes for batteries and supercapacitors.
- Electronics: Applied in the fabrication of field-effect transistors, sensors, and other electronic devices.
-
Key Parameters Influencing the Process:
- Temperature: Determines the decomposition rate of the catalyst precursor and the growth rate of nanomaterials.
- Gas Flow Rate: Affects the distribution and size of catalyst nanoparticles.
- Catalyst Concentration: Influences the density and morphology of the synthesized nanostructures.
- Reactor Design: The geometry and dimensions of the reactor impact the uniformity and quality of the final product.
-
Challenges and Limitations:
- Catalyst Contamination: Residual catalyst particles can remain in the final product, requiring post-synthesis purification.
- Control of Nanostructure Properties: Achieving precise control over the diameter, length, and alignment of nanomaterials can be challenging.
- Energy Consumption: The high temperatures required for the process can lead to significant energy consumption.
-
Future Prospects:
- Improved Catalyst Design: Development of more efficient and selective catalyst precursors to enhance the quality and yield of nanomaterials.
- Process Optimization: Advancements in reactor design and process control to achieve better scalability and cost-effectiveness.
- New Applications: Exploration of novel applications in fields such as biomedical engineering, environmental remediation, and advanced materials.
The floating catalyst method is a powerful and versatile technique for synthesizing high-quality nanomaterials, with significant potential for further development and application in various industries.
Summary Table:
Aspect | Details |
---|---|
Definition | A chemical vapor deposition (CVD) technique for nanomaterial synthesis. |
Mechanism | Catalyst precursor decomposes in a reactor to form nanoparticles for growth. |
Advantages | Scalable, high-quality output, versatile. |
Applications | Carbon nanotubes, nanocomposites, energy storage, electronics. |
Key Parameters | Temperature, gas flow rate, catalyst concentration, reactor design. |
Challenges | Catalyst contamination, control of nanostructure properties, energy use. |
Future Prospects | Improved catalysts, process optimization, new applications. |
Discover how the floating catalyst method can revolutionize your research or production—contact our experts today for more information!