The hydrogen annealing process is a specialized thermal treatment method that utilizes hydrogen gas to enhance the properties of materials, particularly metals and alloys. This process is widely used in industries such as electronics, aerospace, and metallurgy due to its ability to improve material purity, mechanical properties, and surface finish. By leveraging the reducing properties of hydrogen, this method effectively removes surface oxides and impurities, resulting in high-quality materials with enhanced performance characteristics.
Key Points Explained:
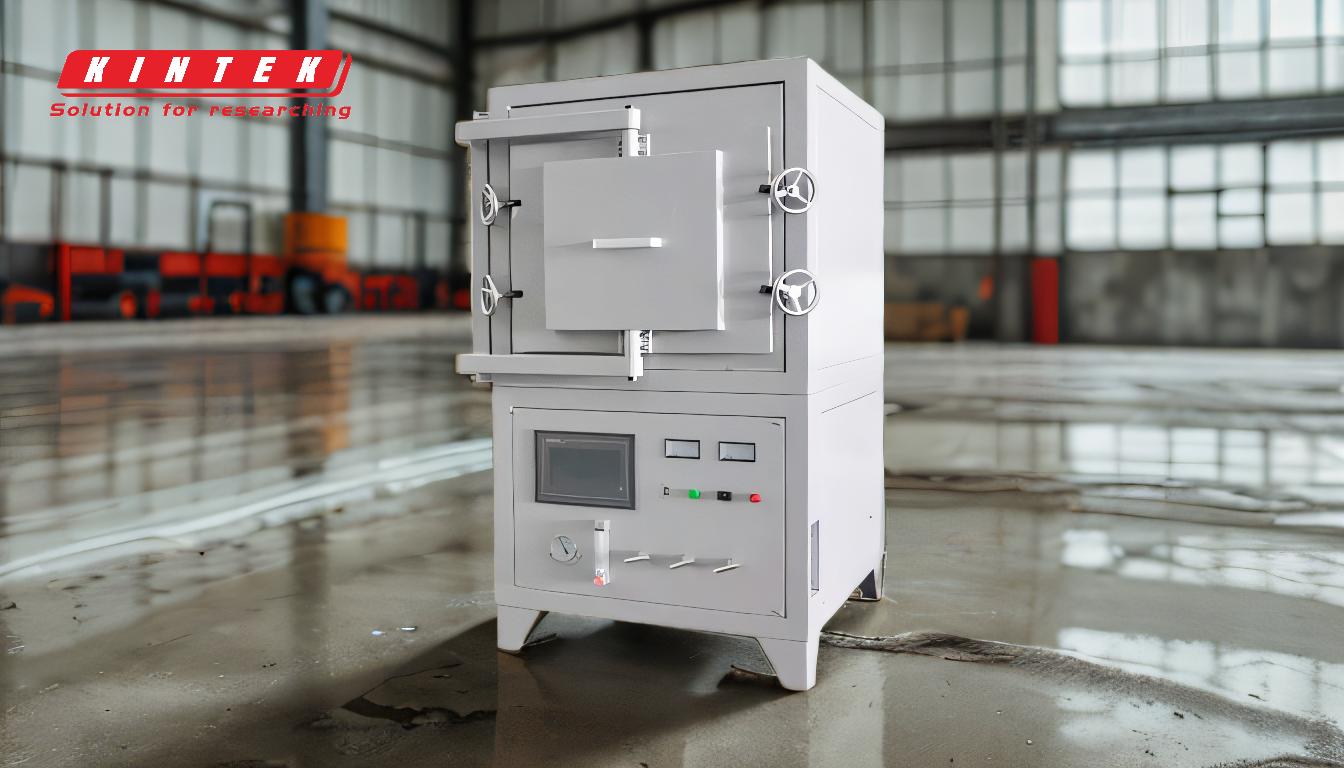
-
High Purity of Hydrogen:
- Hydrogen used in the annealing process typically has a purity level of >99.9995%. This high purity ensures that the material being treated is not contaminated by other gases or impurities, which is critical for achieving optimal results.
- The use of high-purity hydrogen is particularly beneficial for materials that require stringent quality standards, such as those used in semiconductor manufacturing or high-performance alloys.
-
Reduction of Surface Oxides:
- One of the primary functions of hydrogen in the annealing process is its ability to reduce surface oxides. When materials are exposed to high temperatures in the presence of hydrogen, the hydrogen reacts with the oxides on the material's surface, converting them into water vapor and effectively cleaning the surface.
- This reduction process is crucial for improving the material's surface quality and ensuring better adhesion for subsequent coatings or treatments.
-
Removal of Impurities:
- Hydrogen annealing also helps strip impurities like silica from the alloy. These impurities can negatively affect the material's mechanical properties and performance. By removing them, the process enhances the overall quality of the material.
- The removal of impurities is particularly important in the production of high-performance alloys, where even trace amounts of contaminants can lead to significant degradation in performance.
-
Prevention of Metal Oxidation:
- Hydrogen acts as a protective atmosphere during the annealing process, preventing the metal from oxidizing. Oxidation can lead to the formation of undesirable compounds on the material's surface, which can reduce the powders' aggregation ratio and negatively impact the material's properties.
- By preventing oxidation, hydrogen annealing ensures that the material retains its desired properties and achieves a bright, clean surface finish.
-
Superior Mechanical Qualities:
- The hydrogen annealing process results in materials with superior mechanical qualities, such as increased strength, ductility, and toughness. These improvements are due to the removal of impurities and the reduction of surface oxides, which can act as stress concentrators and weaken the material.
- Enhanced mechanical properties are particularly valuable in applications where materials are subjected to high stress or extreme conditions, such as in aerospace or automotive components.
-
Bright Surface Finish:
- A notable benefit of hydrogen annealing is the production of parts with a bright surface finish. This is achieved through the reduction of surface oxides and the prevention of oxidation, which can otherwise lead to a dull or discolored surface.
- A bright surface finish is not only aesthetically pleasing but also indicative of a high-quality material with minimal surface defects, which is important for applications where appearance and surface integrity are critical.
In summary, the hydrogen annealing process is a highly effective method for improving the purity, mechanical properties, and surface finish of materials. By leveraging the unique properties of hydrogen, this process ensures that materials meet the stringent quality standards required for advanced industrial applications.
Summary Table:
Key Benefits | Description |
---|---|
High Purity of Hydrogen | >99.9995% purity ensures no contamination, ideal for semiconductor manufacturing. |
Reduction of Surface Oxides | Removes oxides, improving surface quality and adhesion for coatings. |
Removal of Impurities | Strips silica and other impurities, enhancing material performance. |
Prevention of Metal Oxidation | Protects against oxidation, ensuring a bright, clean surface finish. |
Superior Mechanical Qualities | Increases strength, ductility, and toughness for high-stress applications. |
Bright Surface Finish | Achieves a high-quality, defect-free surface for critical applications. |
Learn how hydrogen annealing can optimize your materials—contact our experts today!