Sputtering in a vacuum is a precise and controlled process used for thin film deposition, where atoms or molecules are ejected from a solid target material and deposited onto a substrate. This process occurs in a vacuum chamber to minimize contamination and ensure high purity. A plasma is generated by ionizing an inert gas (typically argon), and the resulting ions are accelerated toward the target material, causing atoms to be ejected. These ejected atoms travel through the vacuum and deposit onto the substrate, forming a thin film. The process is widely used in industries requiring high precision, such as semiconductor manufacturing, optics, and coatings.
Key Points Explained:
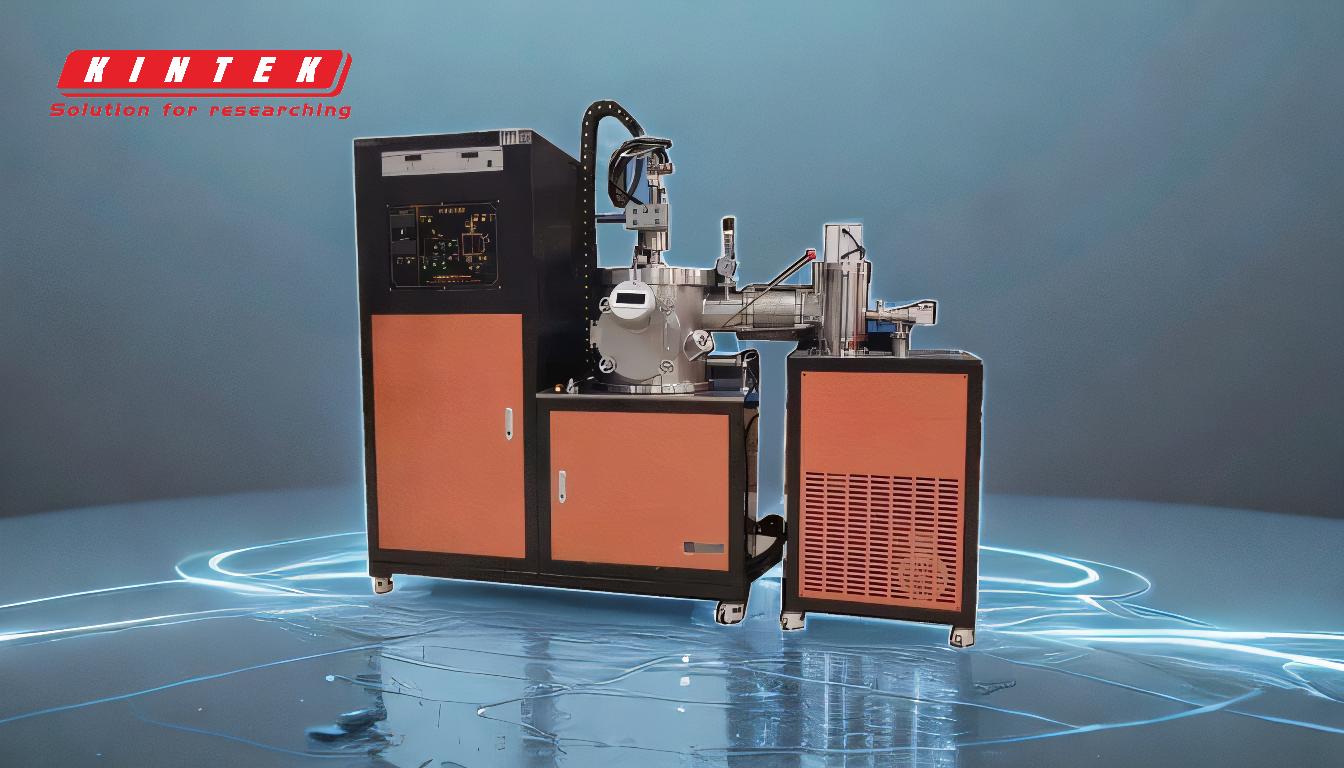
-
Vacuum Environment:
- Sputtering requires a vacuum chamber to remove residual gases and contaminants, ensuring a clean environment for the deposition process.
- The vacuum pressure typically ranges from 10^-1 to 10^-3 mbar, balancing the need for a low-pressure environment with the introduction of the sputtering gas.
-
Target and Substrate Setup:
- The target material (source) and the substrate (destination) are placed inside the vacuum chamber.
- The target is connected as the cathode, and the substrate is connected as the anode, creating an electric field between them.
-
Plasma Generation:
- A plasma is created by ionizing a sputtering gas, usually an inert gas like argon or xenon.
- Ionization occurs through the application of a high voltage or electromagnetic excitation, generating positively charged gas ions and free electrons.
-
Ion Bombardment:
- The positively charged ions are accelerated toward the negatively charged target due to the electric field.
- When these ions strike the target, they transfer their kinetic energy to the target atoms, causing them to be ejected from the surface.
-
Ejection and Transport of Target Atoms:
- The ejected target atoms are in the form of neutral particles.
- These particles travel through the vacuum and deposit onto the substrate.
-
Thin Film Formation:
- The ejected atoms condense on the substrate, forming a thin film.
- The film's properties, such as thickness, uniformity, and purity, are controlled by adjusting parameters like gas pressure, voltage, and target-substrate distance.
-
Magnetron Sputtering (Optional):
- In magnetron sputtering, a magnetic field is used to confine the plasma near the target surface, increasing the efficiency of ion bombardment.
- This method enhances the deposition rate and allows for better control over film properties.
-
Applications:
- Sputtering is widely used in industries requiring high precision, such as:
- Semiconductor manufacturing (e.g., deposition of conductive and insulating layers).
- Optical coatings (e.g., anti-reflective and reflective layers).
- Decorative and functional coatings (e.g., wear-resistant and corrosion-resistant layers).
- Sputtering is widely used in industries requiring high precision, such as:
By following these steps, sputtering in a vacuum enables the production of high-quality thin films with precise control over their properties, making it a critical process in advanced manufacturing and materials science.
Summary Table:
Key Aspect | Details |
---|---|
Vacuum Environment | Pressure: 10^-1 to 10^-3 mbar; ensures a clean, contamination-free process. |
Target and Substrate Setup | Target (cathode) and substrate (anode) create an electric field. |
Plasma Generation | Inert gas (e.g., argon) ionized to generate plasma. |
Ion Bombardment | Ions accelerate toward the target, ejecting atoms. |
Thin Film Formation | Ejected atoms deposit on the substrate, forming a high-purity thin film. |
Applications | Semiconductor manufacturing, optical coatings, and functional coatings. |
Discover how sputtering can enhance your manufacturing process—contact our experts today!