Vacuum casting is a manufacturing process used to create high-quality, detailed replicas of original parts or prototypes. It involves creating a silicone mold from a master model, then using a vacuum to draw liquid resin into the mold, ensuring a bubble-free and precise replication. The process is widely used in industries such as automotive, aerospace, and consumer goods for producing small to medium batches of parts with excellent surface finish and dimensional accuracy. Below is a detailed explanation of the vacuum casting process, broken down into key steps and considerations.
Key Points Explained:
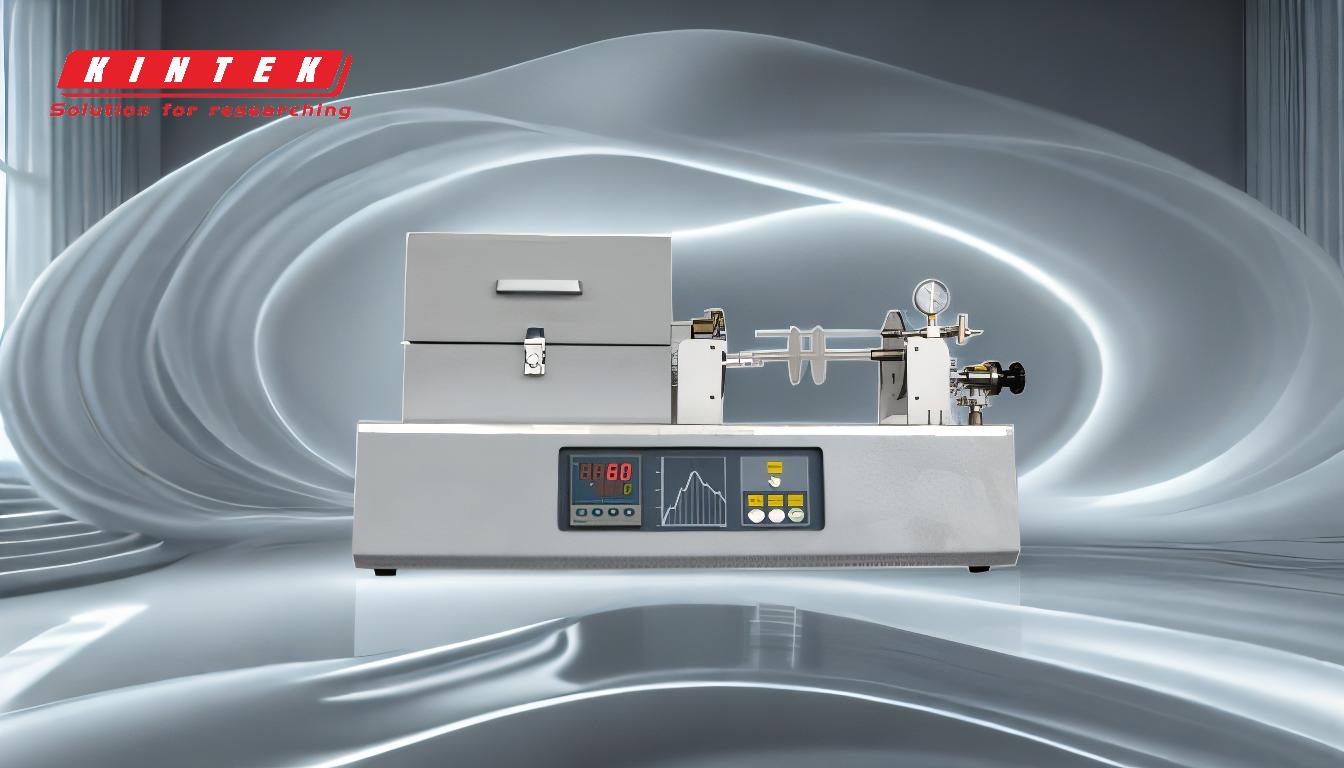
-
Master Model Preparation
- The process begins with the creation of a master model, which is typically produced using 3D printing, CNC machining, or hand sculpting.
- The master model must have a high-quality surface finish, as any imperfections will be replicated in the final cast parts.
- Post-processing steps, such as sanding or polishing, are often applied to the master model to achieve the desired surface quality.
-
Silicone Mold Creation
- The master model is placed in a casting box, and liquid silicone rubber is poured around it.
- The silicone is then cured, usually in an oven, to form a flexible and durable mold.
- Once cured, the mold is cut open to remove the master model, leaving behind a cavity that perfectly matches the shape of the original part.
-
Degassing and Resin Preparation
- The liquid resin used for casting is carefully selected based on the desired properties of the final part, such as strength, flexibility, or transparency.
- The resin is mixed with any required additives, such as colorants or fillers, and then degassed to remove air bubbles.
- Degassing is typically done in a vacuum chamber to ensure the resin is free of bubbles, which could otherwise cause defects in the final part.
-
Vacuum Casting Process
- The prepared resin is poured into the silicone mold, and the entire assembly is placed in a vacuum chamber.
- The vacuum removes any remaining air bubbles from the resin and ensures it fully fills the mold cavity.
- Once the resin has filled the mold, the vacuum is released, and the mold is allowed to cure, either at room temperature or in an oven, depending on the resin type.
-
Demolding and Finishing
- After the resin has fully cured, the silicone mold is carefully opened, and the cast part is removed.
- The part may require minor post-processing, such as trimming excess material or applying a surface finish (e.g., painting or polishing).
- The silicone mold can be reused multiple times, typically producing 20-30 high-quality parts before it begins to degrade.
-
Advantages of Vacuum Casting
- High accuracy and surface finish, making it ideal for replicating intricate details.
- Cost-effective for small to medium production runs compared to traditional manufacturing methods.
- Wide range of material options, including polyurethane resins that mimic various engineering plastics.
- Fast turnaround times, especially when combined with rapid prototyping techniques for the master model.
-
Applications of Vacuum Casting
- Prototyping: Producing functional prototypes for testing and validation.
- Low-volume production: Manufacturing small batches of parts for niche markets or limited editions.
- Replication: Creating exact replicas of existing parts for restoration or replacement purposes.
- Customization: Producing parts with unique colors, textures, or material properties.
By following these steps, vacuum casting provides a versatile and efficient method for producing high-quality parts with excellent dimensional accuracy and surface finish. It is particularly valuable in industries where rapid prototyping and low-volume production are essential.
Summary Table:
Step | Key Details |
---|---|
Master Model Prep | Created via 3D printing, CNC machining, or hand sculpting; requires high finish. |
Silicone Mold Creation | Liquid silicone poured around the master model, cured, and cut for cavity. |
Degassing & Resin Prep | Resin selected for properties, degassed in a vacuum chamber to remove bubbles. |
Vacuum Casting Process | Resin poured into mold, vacuum removes air, and mold cures for precise replication. |
Demolding & Finishing | Mold opened, part removed, and post-processed for final quality. |
Advantages | High accuracy, cost-effective, material versatility, and fast turnaround. |
Applications | Prototyping, low-volume production, replication, and customization. |
Ready to explore vacuum casting for your next project? Contact us today to get started!