The strength of a brazing joint is a critical factor in determining the reliability and durability of the joined components. A well-designed and properly executed brazed joint can achieve a strength that surpasses that of the parent metal. This is due to the formation of a metallurgical bond between the filler metal and the base materials, which results in a joint that is both strong and resilient. The strength of the brazed joint depends on several factors, including the choice of filler metal, the design of the joint, the cleanliness of the surfaces, and the brazing process parameters.
Key Points Explained:
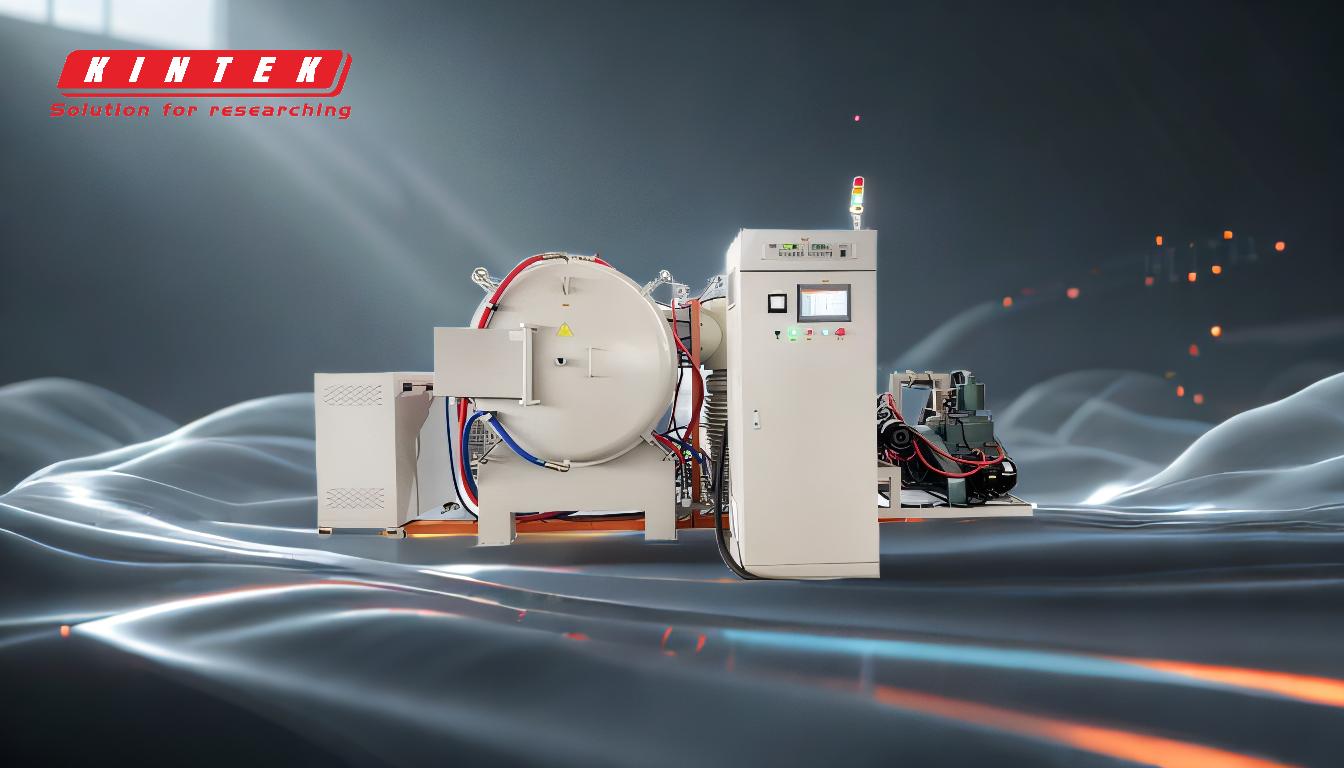
-
Strength of a Brazed Joint vs. Parent Metal:
- A correctly designed and brazed joint can achieve a strength that exceeds that of the parent metal. This is because the filler metal used in brazing forms a metallurgical bond with the base materials, creating a joint that is often stronger than the individual components.
- The strength of the brazed joint is influenced by the properties of the filler metal, which is typically chosen to have a lower melting point than the base materials but with sufficient strength and ductility to withstand the intended application.
-
Factors Influencing Brazed Joint Strength:
- Joint Design: The design of the joint plays a crucial role in determining its strength. A well-designed joint ensures proper distribution of stress and maximizes the surface area for bonding. Common joint designs include lap joints, butt joints, and scarf joints.
- Surface Preparation: Cleanliness of the surfaces to be brazed is essential. Any contaminants, such as oil, grease, or oxides, can weaken the bond. Proper cleaning and the use of fluxes or protective atmospheres are necessary to ensure a strong joint.
- Filler Metal Selection: The choice of filler metal is critical. The filler metal must have good wetting characteristics, appropriate melting temperature, and compatibility with the base materials. Common filler metals include silver-based alloys, copper-based alloys, and nickel-based alloys.
- Brazing Process Parameters: The temperature, heating rate, and cooling rate during the brazing process must be carefully controlled to ensure a strong bond. Overheating can lead to excessive grain growth, while insufficient heating can result in incomplete bonding.
-
Types of Brazed Joints and Their Strength:
- Lap Joints: These joints are commonly used in brazing because they provide a large surface area for bonding. The strength of a lap joint depends on the overlap length and the thickness of the materials being joined.
- Butt Joints: Butt joints are less common in brazing because they offer a smaller bonding area compared to lap joints. However, they can still be strong if properly designed and executed.
- Scarf Joints: Scarf joints are designed to increase the bonding area by cutting the ends of the materials at an angle. This type of joint can provide higher strength compared to butt joints.
-
Testing the Strength of Brazed Joints:
- The strength of brazed joints can be tested using various methods, including tensile testing, shear testing, and peel testing. These tests help to evaluate the joint's ability to withstand different types of stress.
- Non-destructive testing methods, such as ultrasonic testing and X-ray inspection, can also be used to assess the quality and integrity of the brazed joint without damaging it.
-
Applications of Strong Brazed Joints:
- Brazed joints are used in a wide range of industries, including aerospace, automotive, electronics, and HVAC (heating, ventilation, and air conditioning). In these applications, the strength and reliability of the brazed joint are critical to the performance and safety of the final product.
In summary, the strength of a brazing joint is a result of careful design, proper material selection, and precise control of the brazing process. When these factors are correctly managed, a brazed joint can achieve a strength that exceeds that of the parent metal, making it a reliable and durable joining method for various applications.
Summary Table:
Key Factor | Impact on Joint Strength |
---|---|
Joint Design | Ensures proper stress distribution and maximizes bonding surface area. |
Surface Preparation | Clean surfaces prevent contaminants from weakening the bond. |
Filler Metal Selection | Must have good wetting, appropriate melting temperature, and compatibility with base metals. |
Brazing Process | Controlled temperature, heating, and cooling rates ensure a strong, durable bond. |
Need help achieving stronger brazing joints? Contact our experts today for tailored solutions!